
Spalling Concrete and How to Fix It
Spalling or spalled concrete is frequently encountered when coating or lining a concrete substrate.
- High Performance Coatings
Concrete Spalling: Understanding, Preparing, and Repairing with Modern Solutions
Concrete spalling is a common challenge that contractors and facility managers face when maintaining or renovating concrete structures. Understanding how to properly identify, prepare, and repair spalled concrete is crucial for ensuring long-lasting results and successful coating applications.
What is Concrete Spalling?
A spall within a concrete surface is technically defined as "a fragment, usually in the shape of a flake, detached from a larger mass by a blow, by the action of weather, by pressure, or by expansion within the larger mass." These defects are categorized by size:
- Small spalls: Roughly circular depressions not greater than 20 mm in depth and 150 mm in any dimension
- Large spalls: May be circular, oval, or elongated, measuring more than 20 mm in depth and 150 mm in greatest dimension
When spalling occurs, it's essential to address it properly before applying any coating or lining to ensure optimal adhesion and performance.
Pre-Repair Assessment: The Foundation of Success
Before jumping into repairs, a thorough evaluation of the concrete substrate is crucial. This assessment should include:
Visual Inspection
- Detailed examination of the cleaned concrete surface
- Documentation of spall locations and sizes
- Identification of patterns that might indicate underlying issues
Damage Assessment
- Physical damage evaluation
- Chemical damage or attack identification
- Contamination detection
- Concrete defects and curing issues
- Moisture concerns
- Structural integrity evaluation
- Reinforcing steel condition assessment
Surface Preparation: Following Industry Standards
Proper surface preparation is the key to successful concrete repair and coating applications. Two critical industry standards guide this process:
SSPC-SP13/NACE 6 Surface Preparation of Concrete
This standard outlines the required degree of cleanliness for concrete surfaces prior to coating or repair application.
ICRI 310.2R Selecting and Specifying Concrete Surface Preparation
This document governs the level of profile required and provides acceptable means and methods to achieve various surface conditions. The ICRI CSP (Concrete Surface Profile) coupons offer visual representations of required surface profiles, complementing the technical specifications.
Choosing the Right Repair Material
Product selection is critical to repair success. Consider these factors when selecting repair materials:
- Project-specific service conditions and exposures
- Required application thicknesses
- Curing schedules and timeline constraints
- Compatibility with subsequent coating or lining materials
- Environmental conditions during and after application
The CSA Cement Advantage: A Modern Solution
Calcium sulfoaluminate (CSA) cements represent a significant advancement in concrete repair technology. These materials, such as Tnemec's Series 217 MortarCrete, offer several key advantages:
Rapid Strength Development
CSA cements typically achieve near-target 28-day strength in as little as 24 hours, making them ideal for projects requiring quick return to service.
Low Shrinkage Properties
The unique chemistry of CSA cements results in minimal shrinkage during curing. While requiring a higher water-to-cement ratio than Portland cement, CSA cements consume most of this water during hydration, significantly reducing bleed water and associated shrinkage issues.
Environmental Benefits
CSA cements are more environmentally friendly than traditional Portland cements:
- Clinker is softer, requiring less energy for grinding
- Lower kiln temperatures needed: 1250°C (2250°F) versus 1500°C (2700°F) for Portland cement
- Reduced carbon footprint in manufacturing
Application Versatility
Products like Series 217 MortarCrete offer:
- Application thickness range from 1/4 inch to 4 inches in a single lift
- High chemical resistance compared to other cementitious repair mortars
- Ability to accept coatings and linings after just 12 hours at 75°F
- Excellent performance in various exposure conditions
Best Practices for Concrete Repair Success
- Always start with proper assessment - Understanding the extent and cause of damage is crucial
- Follow surface preparation standards - Use SSPC/NACE and ICRI guidelines as your roadmap
- Select materials based on project requirements - Consider all factors including timeline, exposure, and subsequent coatings
- Consider CSA cements for time-sensitive projects - Their rapid cure and high early strength can significantly reduce downtime
- Document your work - Keep records of materials used, application conditions, and any challenges encountered
Conclusion
Successful concrete spall repair requires a systematic approach combining proper assessment, surface preparation, and material selection. Modern CSA cement-based products offer significant advantages for many applications, particularly where rapid return to service is critical. By following industry standards and selecting appropriate materials, contractors can ensure durable, long-lasting repairs that provide an excellent substrate for protective coatings and linings.
References
- AMPP (2021) SSPC-SP13/NACE 6 Surface Preparation of Concrete
- ICRI (2021) 310.2R-2013 Selecting and Specifying Concrete Surface Preparation for Sealers, Coatings, Polymer Overlays and Concrete Repair
- Tnemec (2004) StrataShield Installation & Application Guide Resinous Flooring
- Tnemec (2021) Tnemec Series 217 MortarCrete Product Data Sheet
Check out these other resources
Secondary Containment Coatings- What you need to know
Forklift Traffic on Warehouse Floors
Moisture Vapor Transmission Protection for Concrete Floors
Floor Coatings Are Not Easy to Specify
Selecting the Right Traffic Coating
Concrete Outgassing and How to Prevent It
Considerations Before Coating Concrete Floors
Selecting Coatings for Secondary Containment
Static Dissipative Floor Coatings
Advantages of Polyurethane Cement Coatings
Exploring Decorative Resinous Flooring Options
UV Resistant Epoxy Floor Coatings
Don't miss these flooring project profiles
Secondary Containment Systems in the Southwest
Manufacturing Facility With Flair
Manufacturing Facility Drum Floors and Walls
Town of Gilbert NWTP Containment
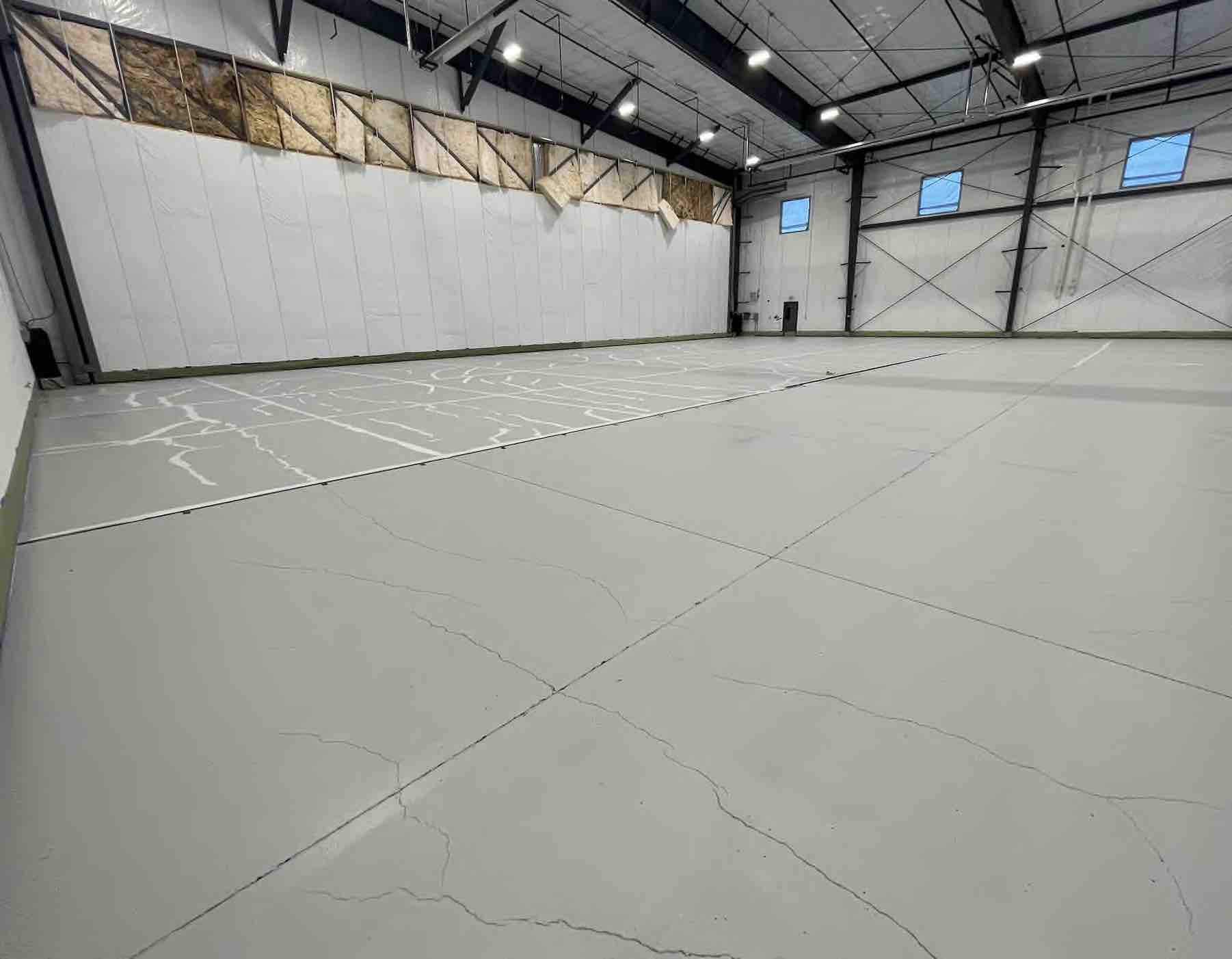
What Should be Considered Before Coating Concrete...
Before coating concrete floors, there are several...
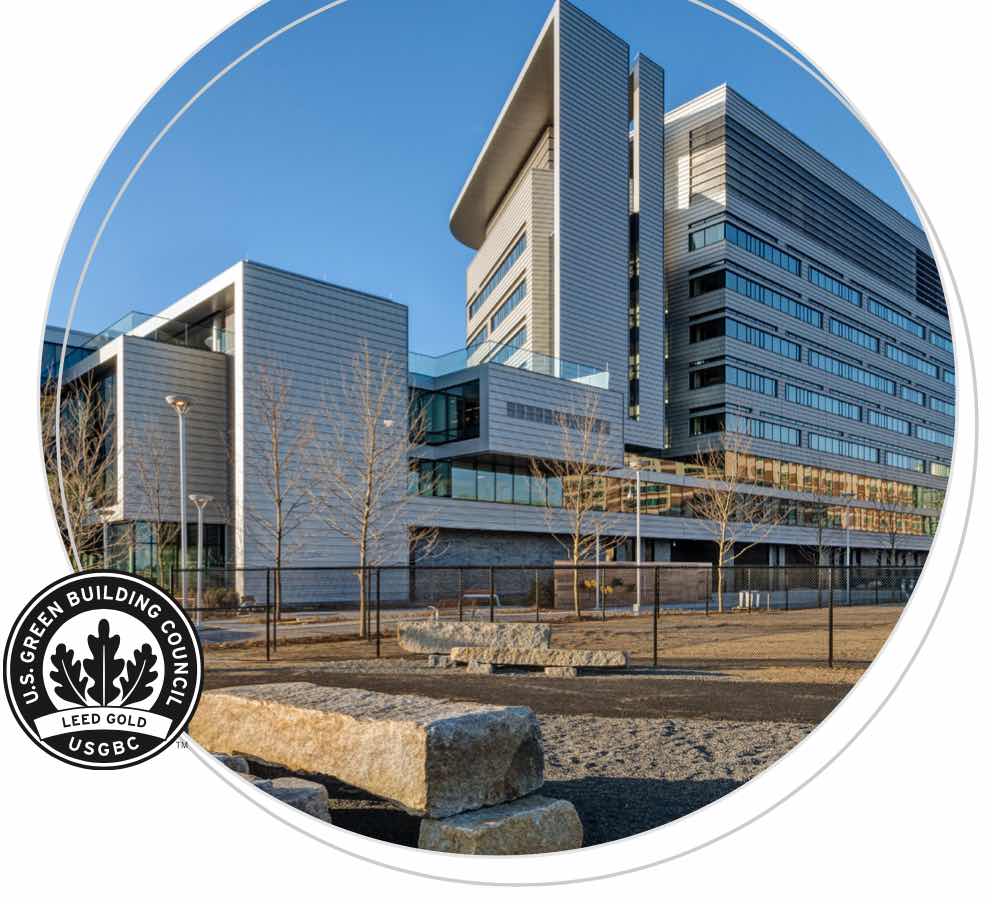
All Elastomeric wall coatings aren’t equal!
All Elastomeric wall coatings aren’t equal!
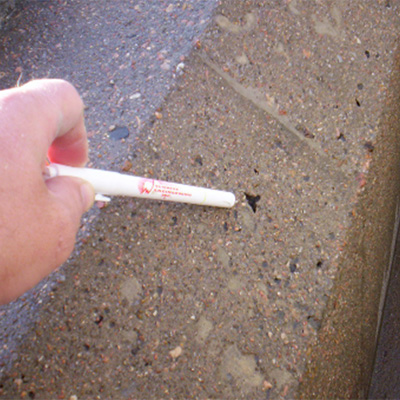
Concrete Repair & Resurfacing in Wastewater...
Wastewater treatment facilities face some of the...