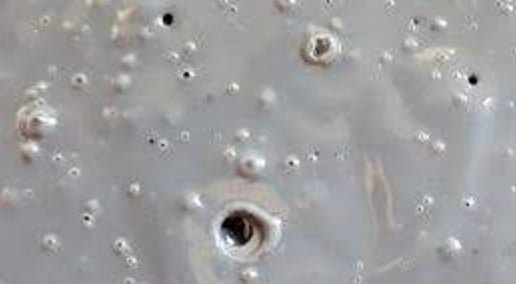
What is Outgassing and How Is It Prevented
When temperatures increase, the air inside these voids or pores expand resulting in a phenomenon called “outgassing.”
- High Performance Coatings
Concrete is one of the most commonly used building materials in the world. And, what appears to be a dense solid mass is actually a structure that is very porous with varying sized voids. As such, when temperatures increase, the air inside these voids or pores expand resulting in a phenomenon called “outgassing.” Outgassing itself is not a problem until protective coatings are being applied. If coatings are applied to an outgassing substrate, pinholes can result, which if not repaired, may substantially reduce the service life of the coating system.
For that reason, as a coatings applicator, it is important to plan your project to avoid an outgassing substrate as follows:
- Wait to coat surfaces until temperatures are stable or descending. When the volume of air inside the concrete substrate is stable or contracting.
- Utilize epoxy modified cementitious resurfacers (Tnemec Series 218) to parge the surface and fill voids and bugholes which can contribute to outgassing and pinholes.
- Shade concrete surfaces from direct sunlight.
- Spray and backroll a compatible primer under the right conditions to seal the surface and create a thin film air block.
- If in confined spaces, supply indirect fired heat for a time before coatings will be applied to increase the substrate temperature and turn heat off an hour or two before coating operations resulting in a decreasing surface temperature.
For more information on outgassing, or to discuss coating systems and resurfacers that can help eliminate or remediate outgassing, reach out to High Performance Coatings for more information.
Check out these other resources
Secondary Containment Coatings- What you need to know
Forklift Traffic on Warehouse Floors
Moisture Vapor Transmission Protection for Concrete Floors
Spalling Concrete and How to Fix It
Floor Coatings Are Not Easy to Specify
Selecting the Right Traffic Coating
Considerations Before Coating Concrete Floors
Selecting Coatings for Secondary Containment
Static Dissipative Floor Coatings
Advantages of Polyurethane Cement Coatings
Exploring Decorative Resinous Flooring Options
UV Resistant Epoxy Floor Coatings
Don't miss these flooring project profiles
Secondary Containment Systems in the Southwest
Manufacturing Facility With Flair
Manufacturing Facility Drum Floors and Walls
Town of Gilbert NWTP Containment
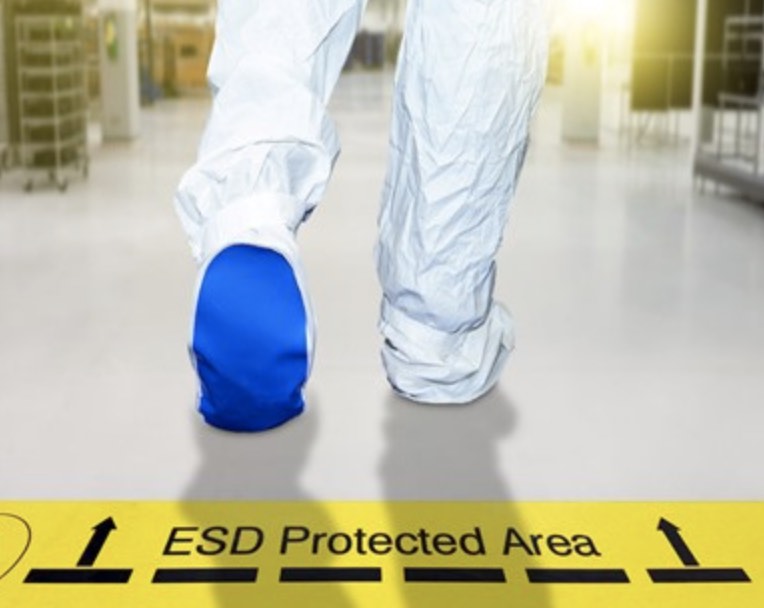
What are Static Dissipative Floor Coatings and...
Static dissipative floor coatings are specialized...
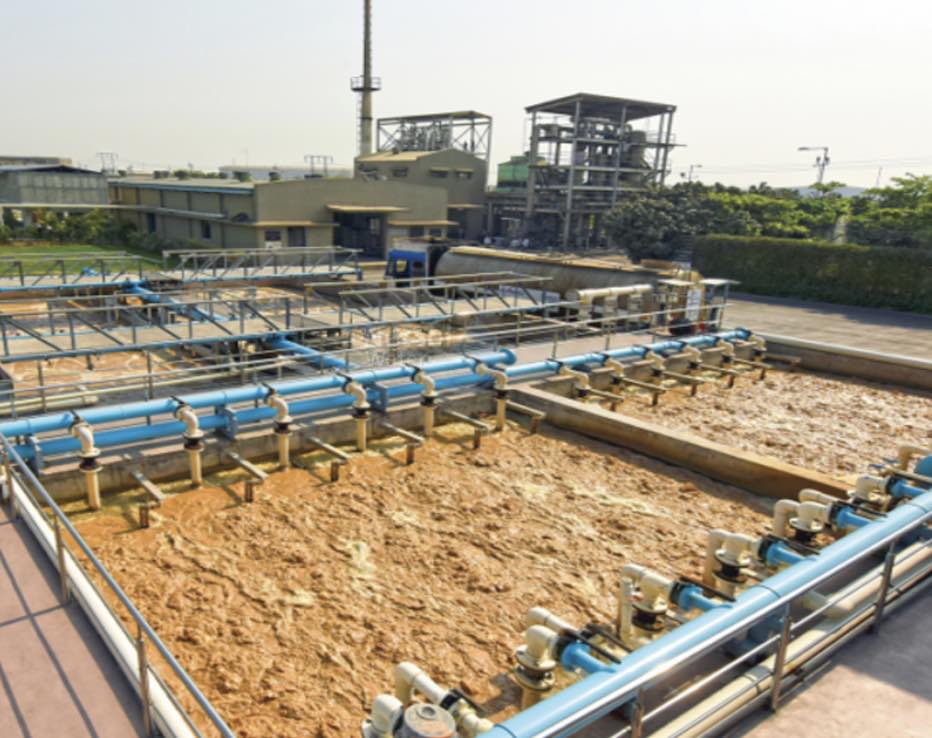
Maximizing the Performance of Membrane BioReactors
Here we'll explore the innovative MBR technology...
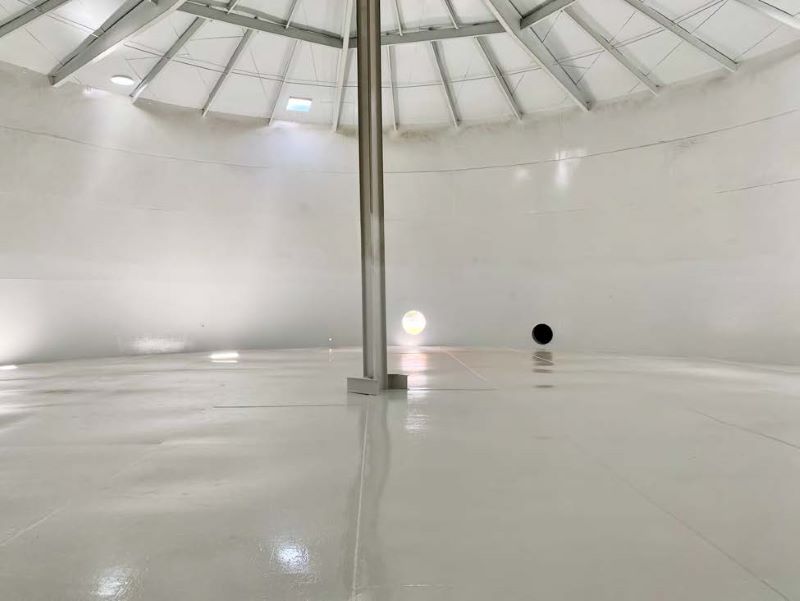
Interior Immersion Grade Coatings: Protecting...
Ensuring the longevity and safety of potable...