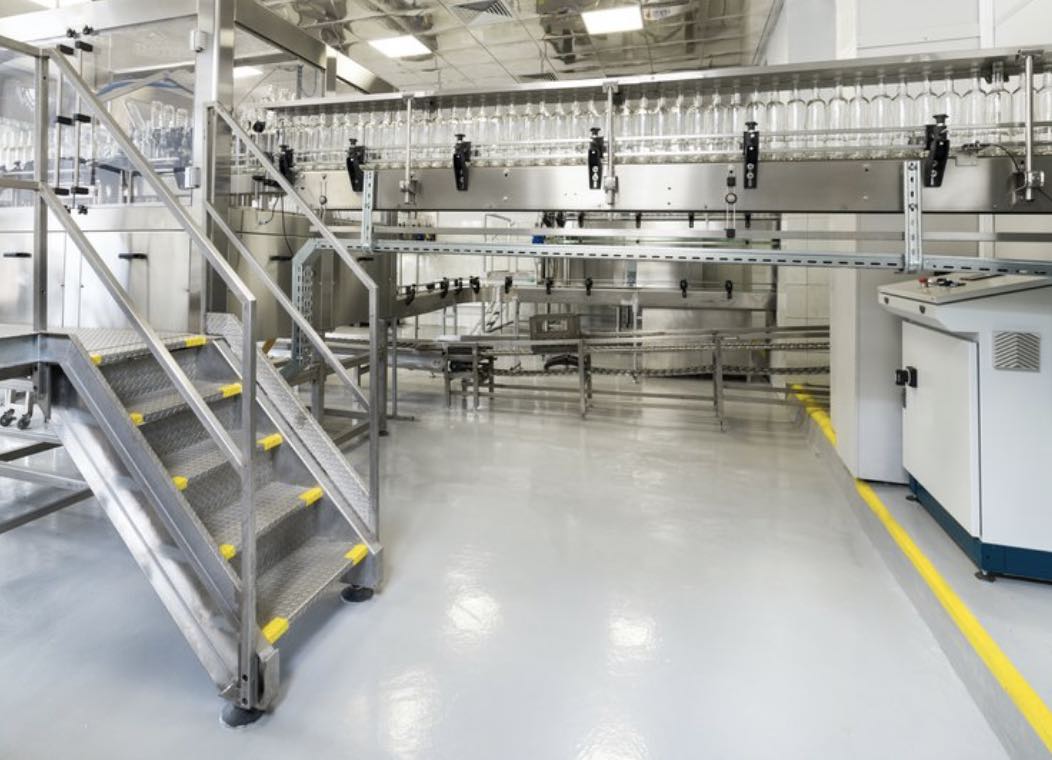
What is polyaspartic? Where is it used? Is it better than epoxy?
Developed originally in the 90’s, Polyaspartics have enhanced the performance flooring market by utilizing the speed of Polyurea chemistry.
- High Performance Coatings
Fast is fast is good right? Unless it’s too fast! Speed of application and speed of “in-service” times are both paramount in construction, but equipment limitations and working time can sometimes affect quality and constructibility.
Developed originally in the 90’s, Polyaspartics have enhanced the performance flooring market by utilizing the speed of Polyurea chemistry but modifying it slightly by partially blocking the amine curing agent so that the reaction time allows for traditional batching and roller applied applications. The result is a versatile resin that has good UV stability with low yellowing characteristics. Although Polyaspartics can be pigmented, they are usually used in clear form over vinyl flake and colored quartz as a “grout” or “finish coat”. Epoxies can be used in similar fashion, but are never truly UV stable and will yellow over time. Epoxies do however have a significant role in other layers of these flooring systems
Adequate pot life and working time allow for applicators to install the coating to decorative standards while the accelerated curing cycle provides quick return-to-service times. So, as you can imagine, these characteristics bode well in the performance flooring market. Tnemec Series 257 Excellathane SS (slower setting) offers applicators an extended pot life and over 20 minutes of working time to ensure that roller marks and lap lines are alleviated.
Furthermore, Polyaspartics can be formulated as non-rigid coatings and are resistant to hot-tire staining and delamination, so they are often found in vehicular garages as the finish coat to decorative floors. Many formulations like the Tnemec Series 256 and 257 are nearly 100% solids, so VOC’s are near zero and the odor is barely detectable….further benefits in flooring applications which are typically indoors where occupants don’t want to be displaced during installation.
As with most coatings, the complete system is composed of other technologies which all serve various functions. Selecting the right primers, properly preparing the substrate, evaluating MVT (moisture vapor transmission), choosing the proper non-skid profile, and satisfying the owners’ aesthetic vision are just some of the variables that need to be considered prior to specifying the full system.
Contact us to discuss your specific project and benefit from our expertise and proven systems.
Check out these other resources
Secondary Containment Coatings- What you need to know
Forklift Traffic on Warehouse Floors
Moisture Vapor Transmission Protection for Concrete Floors
Spalling Concrete and How to Fix It
Floor Coatings Are Not Easy to Specify
Selecting the Right Traffic Coating
Concrete Outgassing and How to Prevent It
Considerations Before Coating Concrete Floors
Selecting Coatings for Secondary Containment
Static Dissipative Floor Coatings
Advantages of Polyurethane Cement Coatings
Exploring Decorative Resinous Flooring Options
UV Resistant Epoxy Floor Coatings
Don't miss these flooring project profiles
Secondary Containment Systems in the Southwest
Manufacturing Facility With Flair
Manufacturing Facility Drum Floors and Walls
Town of Gilbert NWTP Containment
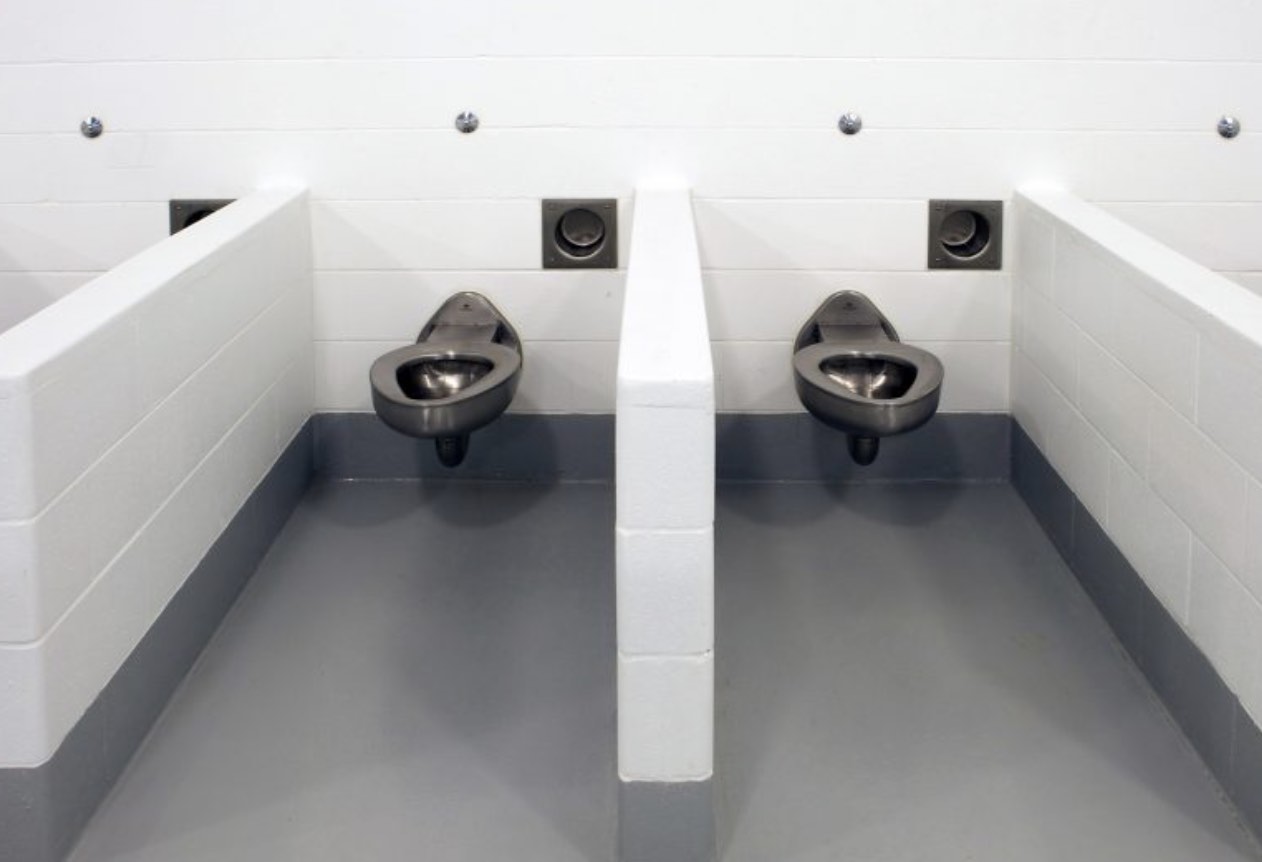
Correctional Facilities Require Coatings That...
Correctional Facilities require coatings that...
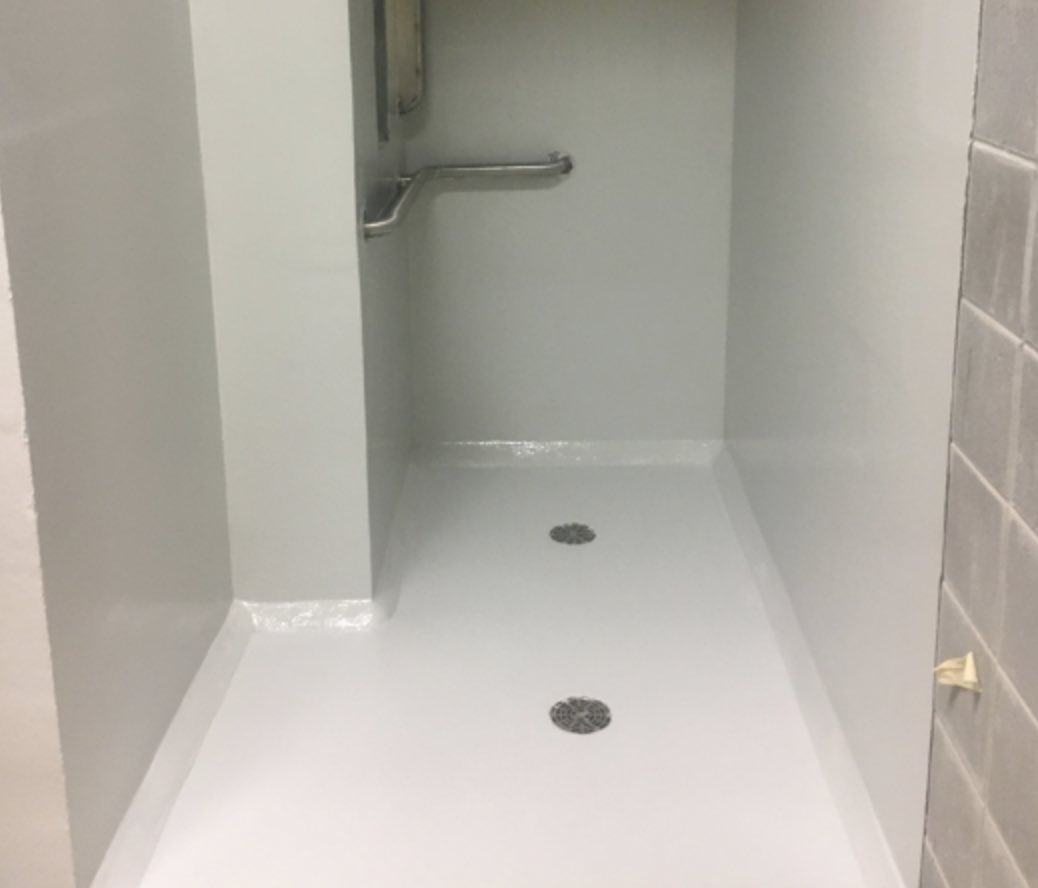
Where to use a Fiberglass Reinforced Wall System
Epoxy mat layup wall systems, like Tnemec...

What Coatings are Best for Marine Environments
Marine coatings are specially designed coatings...