Lamb Weston Potato Plant | High Performance Coatings
When key production and employee areas at Lamb Weston needed repairs and upgrades to the floors in 2016, all the work had to be done in a handful of days.
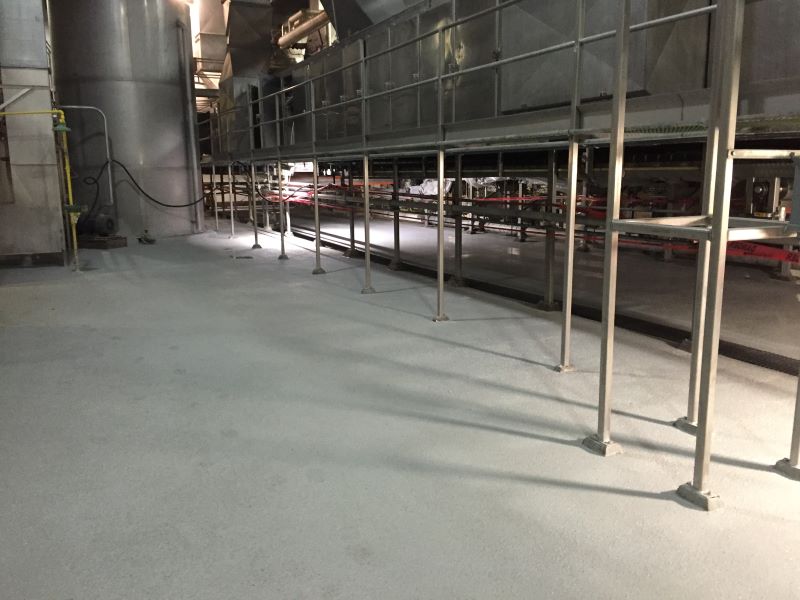
PROJECT INFORMATION
Project Location
Richland, Washington
Project Completion Date
April 2016
Owner
Lamb Weston, inc.
Richland, Washington
Applicator
Matheson Painting, Inc.
The Lamb Weston frozen potato processing plant has been in operation since 1972 and employs around 500 people. When key production and employee areas needed crucial repairs and upgrades to the floors in 2016, all the work had to be done in a handful of days. “The floor areas being coated also had major mechanical equipment repairs, so quick return to service was required,” recalled local Tnemec representative, Rick Gilbreath with TNW, Inc. “The floors had to be properly prepared, coated, and cured to service in three or four days from start to finish.” Besides the time factor, the coatings needed to resist a variety of different exposures, including constant steam cleaning, thermal shock, hot cooking oil, caustic chemical wash-downs and the abrasion from foot and forklift traffic. Further, Lamb Weston's sanitation manager was very concerned about microbial growth, which led Gilbreath to the Series 245 and Series 44-790 product recommendation to provide anti-microbial properties.
Gilbreath worked with Processing and Manufacturing Market Director, Joe Schmit, to design each coating system to meet the facility’s performance needs. The dryer portion of the facility had 8,000 square feet of area and had to be prepped, applied, and cured in four days. The coating system applied in this area was Series 245 Ultra-Tread S, which was bulked up with sand to create a repair material for patching. Next, Series 245 was applied as slurry and broadcast to refusal with sand. Finally, the system was topcoated with Series 237 Power-Tread.
The deteriorated trench drain was primed with Series 201 Epoxoprime and then brought back to level with Series 215 Epoxy Surfacer. Series 282 Tneme-Glaze was applied as the finish coat for chemical resistance.
Series 244 Ultra- Tread M, a trowel-down polyurethane concrete, was applied at 1⁄2 inch thickness in the high-temperature area under condensation return, which, when in service, is exposed to 14 pressure valves constantly spraying 220°F steam.
“The main entrance to the plant had to be completely finished and walkable before the plant went back online,” stated Gilbreath. “Using Series 256 Excellathane, the contractor was able to prep and apply all coats in a three-day window, allowing the fourth day for the topcoat to cure.” The system applied to the plant entrance consisted of Series 256 Excellathane double-broadcast with decorative quartz. Two more coats of Series 256 were applied before Series 248 Everthane was applied to give extra resistance to foot traffic. In production areas, Series 245 Ultra-Tread S was utilized again for its fast-curing properties and versatility. In the pre-cooler room, Series 245 was extended with sand to create a patching and sloping material. Then, Series 245 was applied, broadcast to refusal and later topcoated with Series 237.
Headquartered in Idaho, Lamb Weston is the #1 producer of frozen potato products in the USA and #2 globally. Lamb Weston has 22 manufacturing facilities around the globe and sells 60 million portions of fries daily worldwide.
Check out these other resources
Secondary Containment Coatings- What you need to know
Forklift Traffic on Warehouse Floors
Moisture Vapor Transmission Protection for Concrete Floors
Spalling Concrete and How to Fix It
Floor Coatings Are Not Easy to Specify
Selecting the Right Traffic Coating
Concrete Outgassing and How to Prevent It
Considerations Before Coating Concrete Floors
Selecting Coatings for Secondary Containment
Static Dissipative Floor Coatings
Advantages of Polyurethane Cement Coatings
Exploring Decorative Resinous Flooring Options
UV Resistant Epoxy Floor Coatings
Don't miss these flooring project profiles
Secondary Containment Systems in the Southwest
Manufacturing Facility With Flair
Manufacturing Facility Drum Floors and Walls
Town of Gilbert NWTP Containment
MORE HIGH PERFORMANCE COATINGS PROJECTS
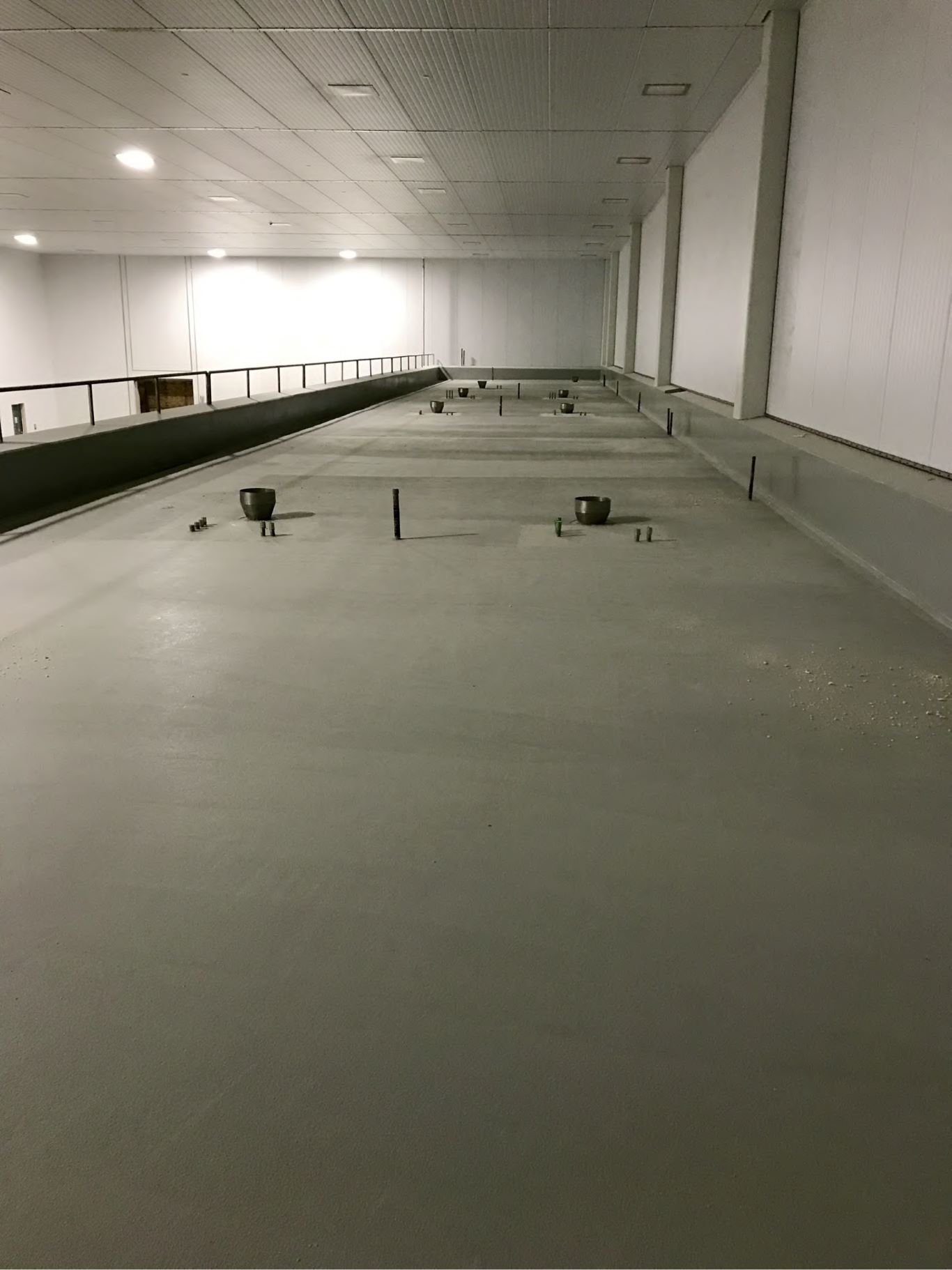
Twin City Foods, Pasco WA Fresh Pack...
Twin City Foods in Pasco Washington turned to TNW, Tnemec to help specify the correct floor...
Market Type:
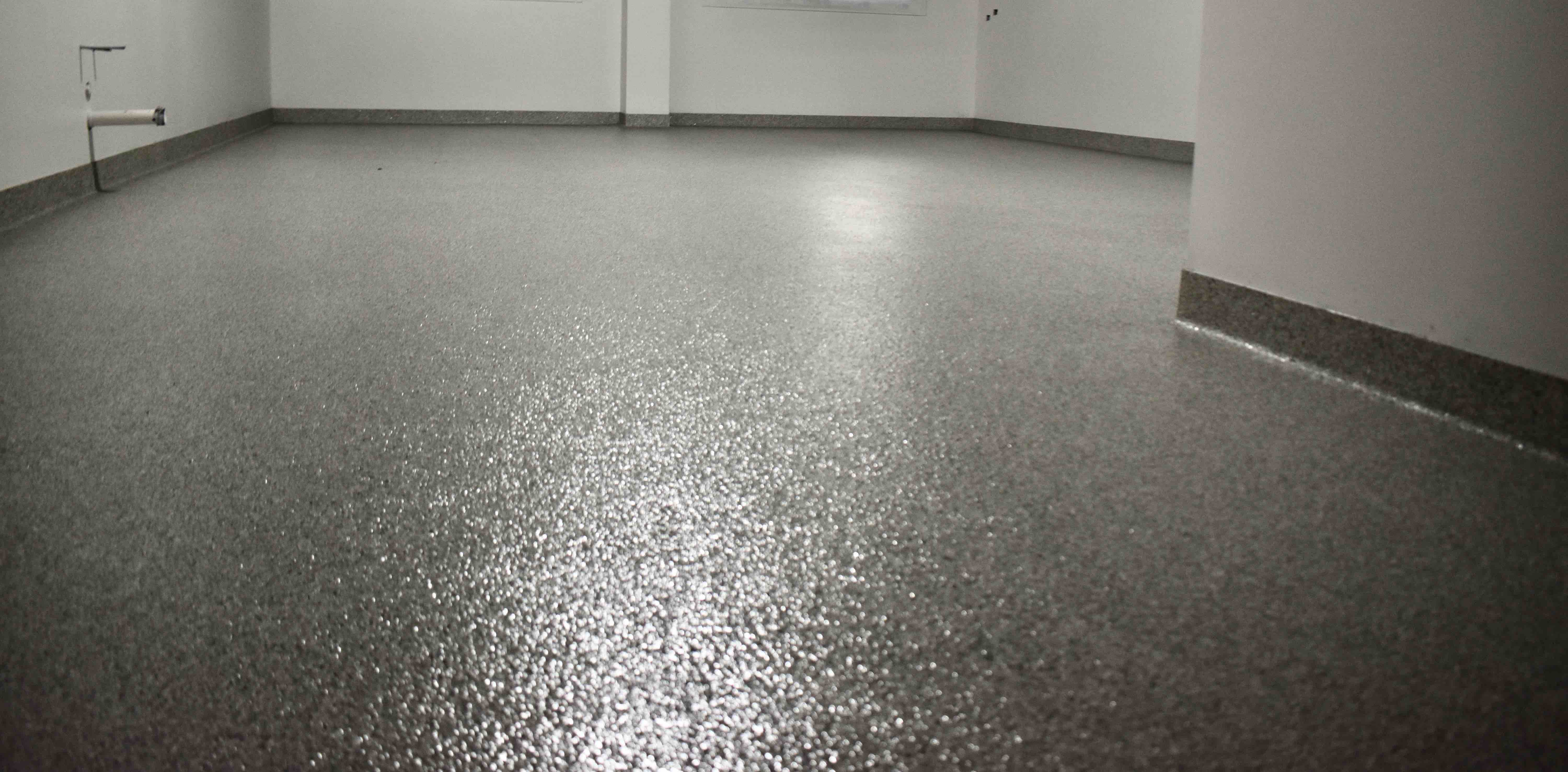
NDSU Peltier Complex
NDSU's new Peltier Complex will provide a new home for:
Market Type:
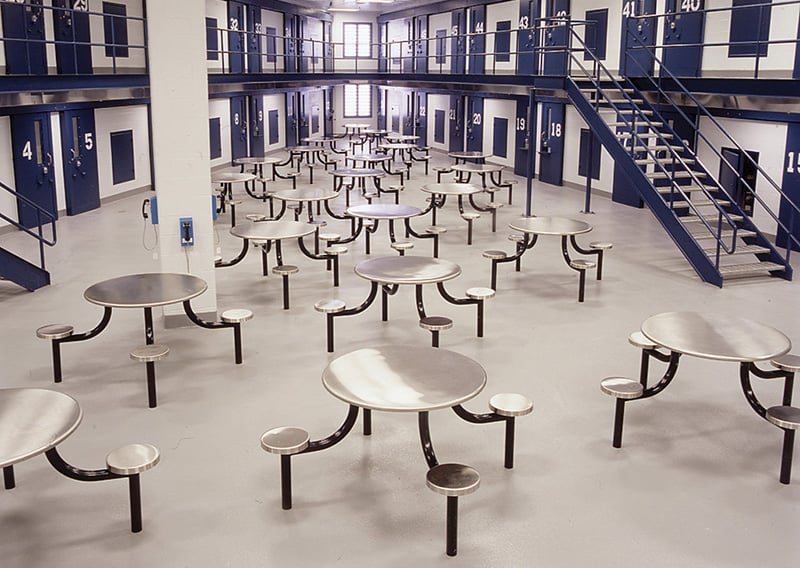
Butler County Jail
A correctional facility is almost never taken out of service and once filled with inmates, it is...
Market Type:
OR
LET OUR KNOWLEDGE AND EXPERTISE HELP ENSURE YOUR NEXT PROJECT IS SUCCESSFUL