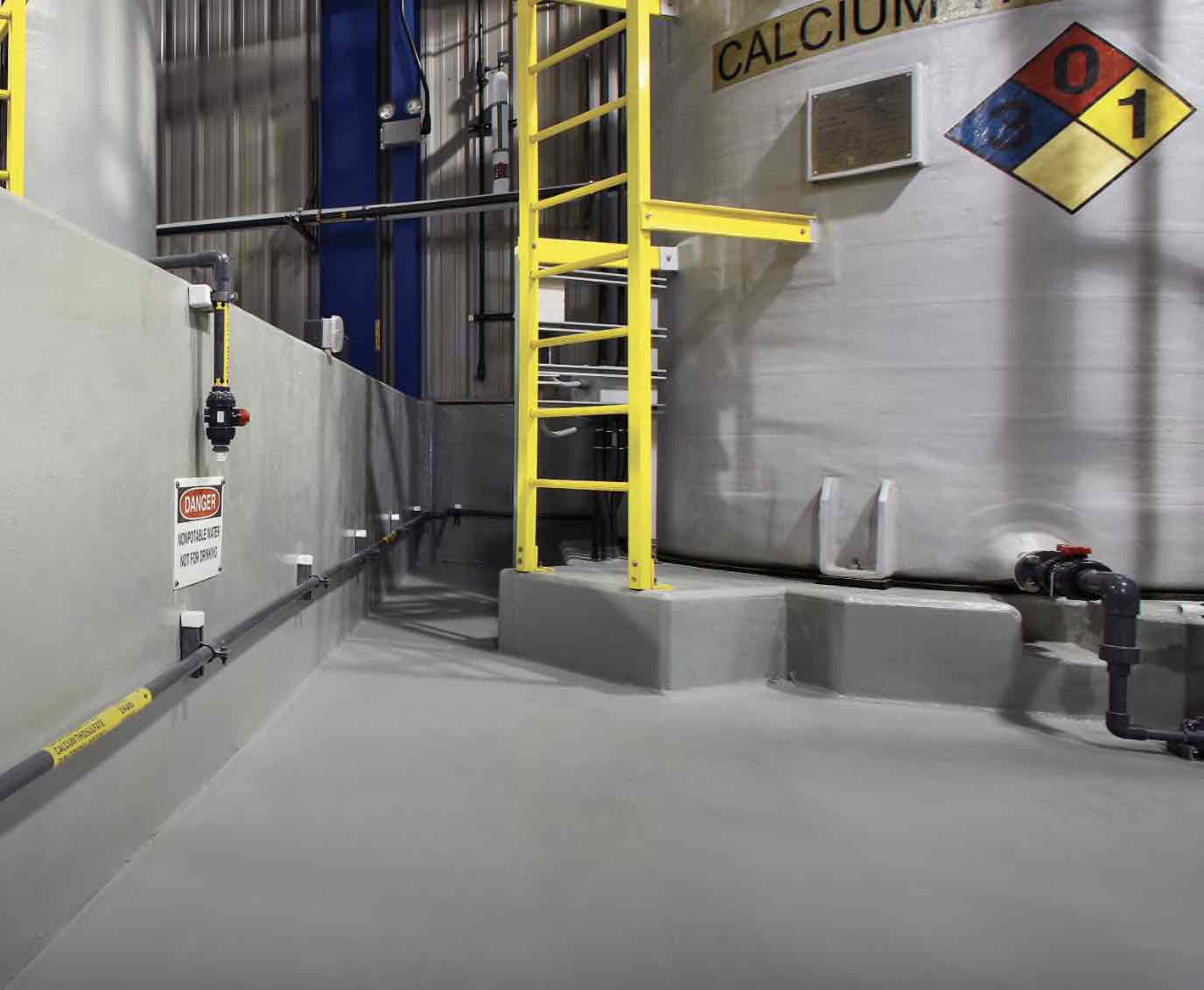
What Coatings Should be Used for Secondary Containment?
Secondary containment coating systems are designed to provide a protective barrier between the contents of a storage tank or vessel and the environment.
- High Performance Coatings
Secondary containment coating systems are designed to provide a protective barrier between the contents of a storage tank or vessel and the environment in the event of a leak or spill. The coating system is typically applied to the surface of the containment area and can be made of various materials, depending on the chemical resistance required.
When selecting a coating system for secondary containment, it is important to consider the type of chemical or substance being stored, as well as the potential for spills or leaks. Factors such as temperature, pressure, and exposure to sunlight can also impact the performance of the coating system. Some commonly used coating systems for secondary containment include:
- Epoxy coatings like Series 282 are known for their excellent chemical resistance and adhesion properties, making them an ideal choice for secondary containment applications. They can be applied in multiple layers to achieve a thick, durable coating that can withstand exposure to harsh chemicals and acids.
- Polyurethane cement coatings like Series 245 are sometimes used in secondary containment applications due to their high chemical resistance and durability, but also due to their ability to be applied over green concrete or in high MVT situations. They are also particularly useful in areas where there is a risk of impact, as they are able to withstand heavy physical wear and tear.
- Vinyl ester coatings like Series 1415 or Series 1416 are a combination of polyester and epoxy resins, providing excellent chemical resistance and thermal stability. They are commonly used in applications where high temperatures and exposure to harsh chemicals are a concern.
- Fiberglass reinforced lining systems like Series 252SC or Series 239SC involve the application of a fiberglass-reinforced liner that is then coated with a protective resin. They offer excellent resistance to a wide range of chemicals and are often used in applications where there is a risk of physical damage. Fiberglass reinforcement is considered by many to be the only true secondary containment application due to its ability to protect moving substrates that may crack over time.
When selecting a coating system for secondary containment, it is important to work with a coatings specialist to ensure that the system is appropriate for the specific application and will provide long-term protection against leaks and spills. Proper surface preparation and application techniques are also critical to the success of the coating system. For more information on specifying secondary containment systems, reach out to a High Performance Coating Consultant here.
Check out these other resources
Secondary Containment Coatings- What you need to know
Forklift Traffic on Warehouse Floors
Moisture Vapor Transmission Protection for Concrete Floors
Spalling Concrete and How to Fix It
Floor Coatings Are Not Easy to Specify
Selecting the Right Traffic Coating
Concrete Outgassing and How to Prevent It
Considerations Before Coating Concrete Floors
Static Dissipative Floor Coatings
Advantages of Polyurethane Cement Coatings
Exploring Decorative Resinous Flooring Options
UV Resistant Epoxy Floor Coatings
Don't miss these flooring project profiles
Secondary Containment Systems in the Southwest
Manufacturing Facility With Flair
Manufacturing Facility Drum Floors and Walls
Town of Gilbert NWTP Containment

Advantages of Polyurethane Cement Floor Coatings
In the world of industrial and commercial...
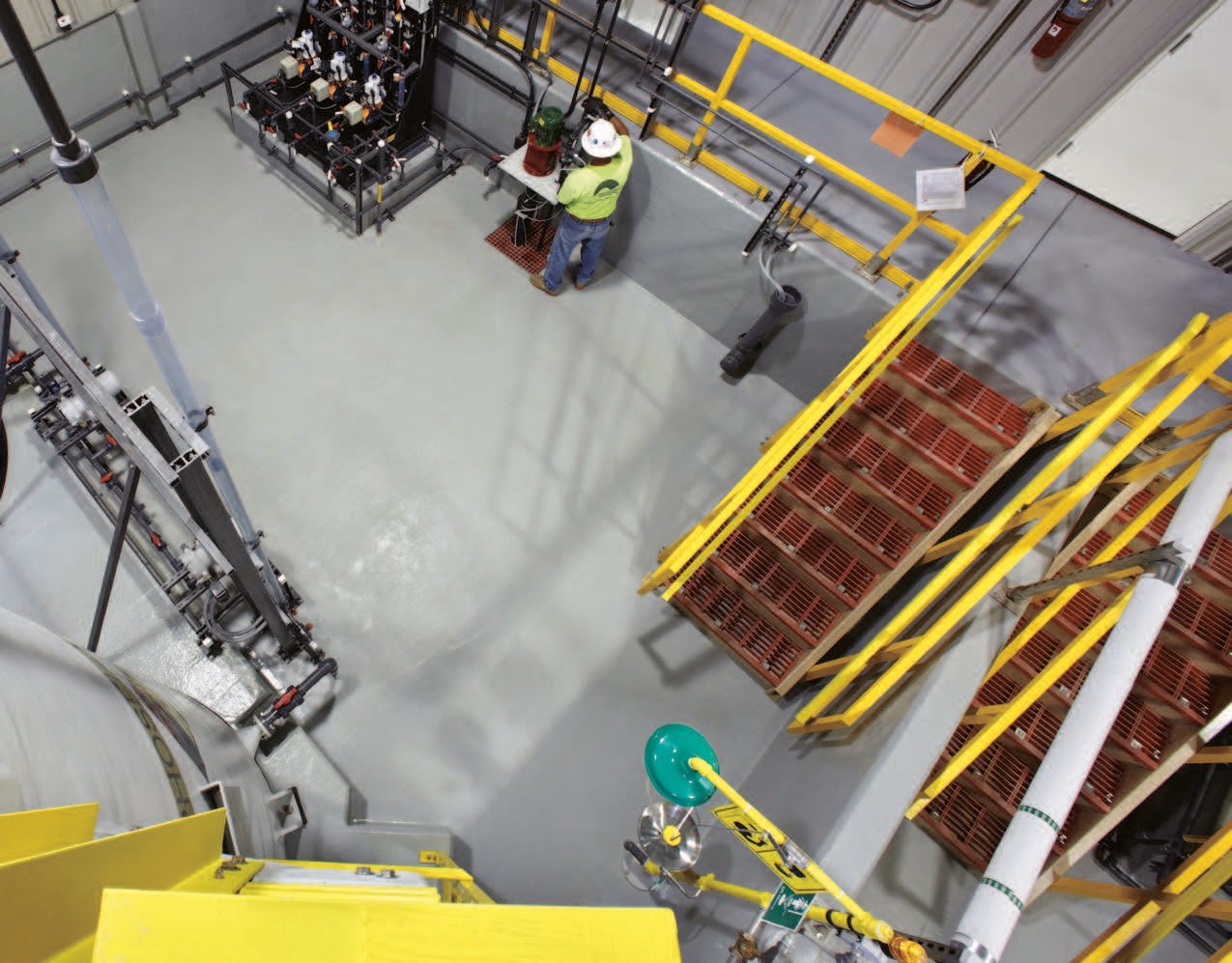
Exploring Secondary Containment linings
Dive deep into the world of secondary containment...

Exploring Decorative Resinous Flooring Options
Exploring Decorative Resinous Flooring: A World...