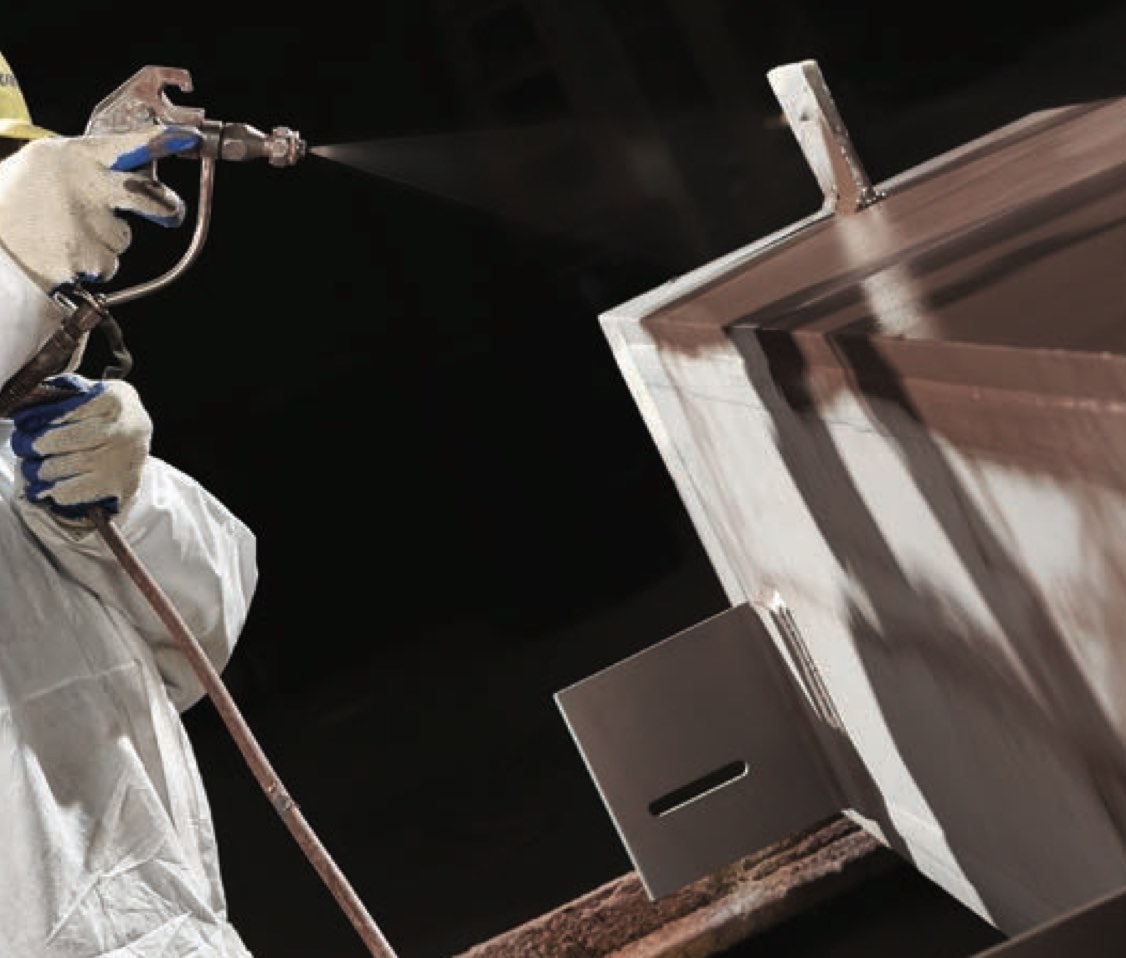
Shop Priming for High Performance Coating Systems
All too often, we receive inquiries about application of high-performance finishes over generic alkyd shop primers commonly used by fabricators. Most of the time, this is a very bad idea.
- High Performance Coatings
How often do High Performance Coatings in Division 09 become excluded or modified because the steel wasn’t prepared correctly, or because a high-performance primer wasn't installed? Is this a fabricator oversight, or perhaps a specification error? Is the long-term protection of your structural steel in jeopardy? How do you avoid this? Is the owner getting what he wants and needs?
All too often, we receive inquiries about application of high-performance finishes over generic alkyd shop primers commonly used by fabricators. Most of the time, this is a very bad idea. Most generic shop primers are simply applied directly to the mill scale and are designed to prevent flash rusting during storage, transportation, and erection of the steel. These primers and the minimal surface preparation required to apply them are not designed to support high-performance coating systems specified in Division 9. Alkyd shop primers don’t typically contain effective corrosion inhibitors, and are most certainly not suited to providing cathodic protection. Adhesion of these products is often minimal due to the lack of anchor profile and low standards of substrate cleanliness.
Understanding the basics of high-performance coating systems begins with knowing that they typically are comprised of multiple products of differing generic chemistries, each with its own unique function in the completed application. One tried and true high-performance combination for coating steel would be:
- Zinc Rich Primer: High zinc pigment volume imparts passive cathodic protection to steel substrates.
- Epoxy Intermediate Coat: Low-permeability epoxies offer barrier protection to prevent atmospheric contaminants from prematurely attacking the zinc-rich primer and underlying steel.
- High-Performance Finish Coat: A multitude of finish coat technologies can be selected to protect the cathodic and barrier protection afforded by the primer and intermediate coats. The finish coat provides UV stability, extending the completed systems ability to retain color and gloss for an extended period of time. Finish coats can also be selected for enhanced resistance to chemical attack, abrasion, impact, and many other service condition considerations.
Where it comes to surface preparation, it is also essential that we understand that each individual component of the high-performance coating system will exert a curing stress on the substrate and previously applied coats, so it is critical that we provide a well prepared, solid foundation, and a clean surface with an anchor profile to achieve maximum adhesion. Poor surface preparation, lack of profile, and subpar primers will often lead to premature failures of what might otherwise be a serviceable high-performance coating system.
So how do we avoid these issues? The best defense is a good offense to prevent this from being an oversight in the first place. Make sure that the specification gives proper direction where it matters. First, make sure your construction drawings have distinct notes on the surface preparation and primer to be used where high performance coatings will be installed. Second, make sure your Division 5 specification sections reference the same surface preparation and primer standards as the drawings, and make sure they are consistent with the primer and system being specified in the high-performance coating section under Division 9. Then of course, ensure that your Division 9 high-performance coating systems reference all the products within the system, and note who is responsible for the preparation and priming (typically the steel fabricator), and field touch up of shop-applied primers following erection (typically the field applicator). If all of these construction documents are appropriately referenced to each other, everyone has a clear outline of the responsibilities of each party and shouldn’t be missed during bidding nor construction.
For detailed technical information about these specification sections, and the benefits of proven primers like the Tnemec Tneme-Zinc 90-97 that support all high performance coatings, please contact us to request assistance on your specific project.
Check out these related resources
Why High Performance Coatings Fail
Performance Based Coating Specifications
The Importance of Surface Preparation
Don't miss these related project profiles

What Is The Role of High Performance Coatings in...
Restoration projects play a vital role in...
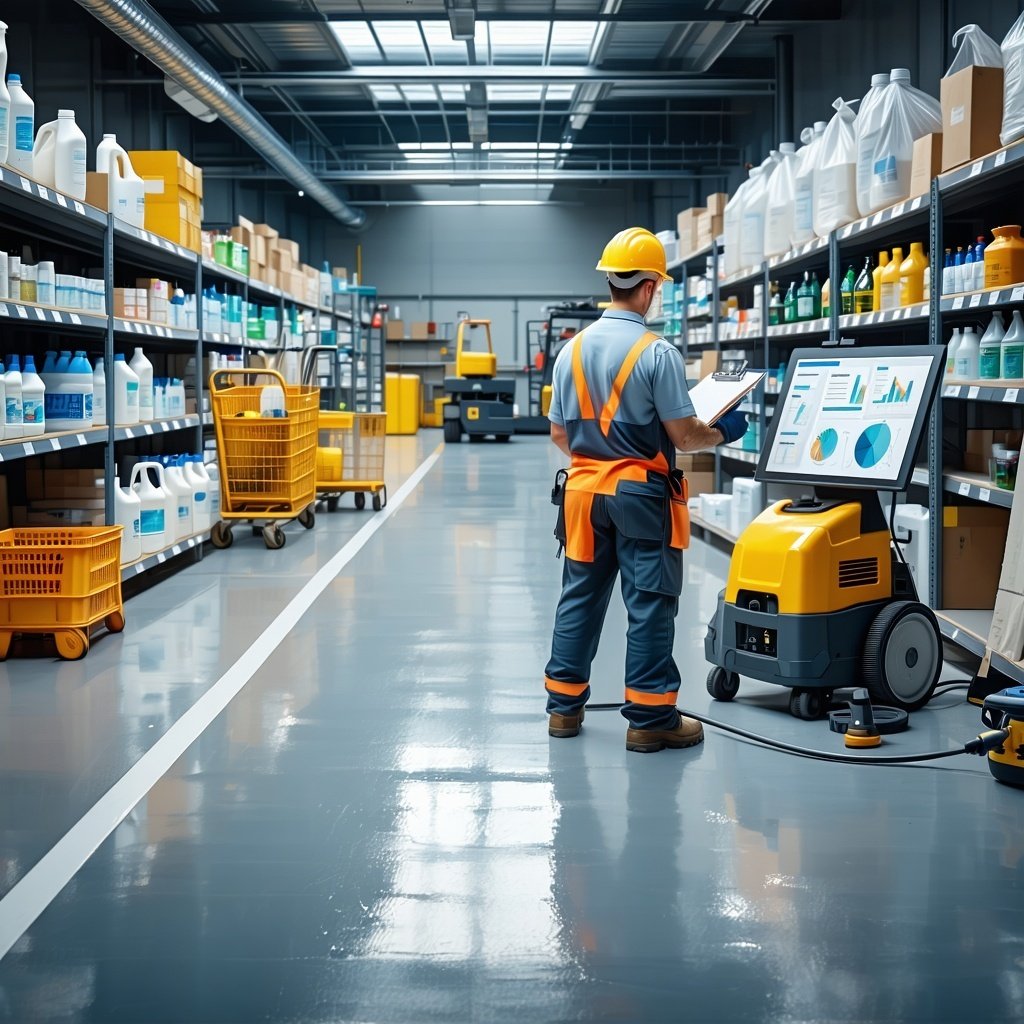
What Maintenance is Required with High...
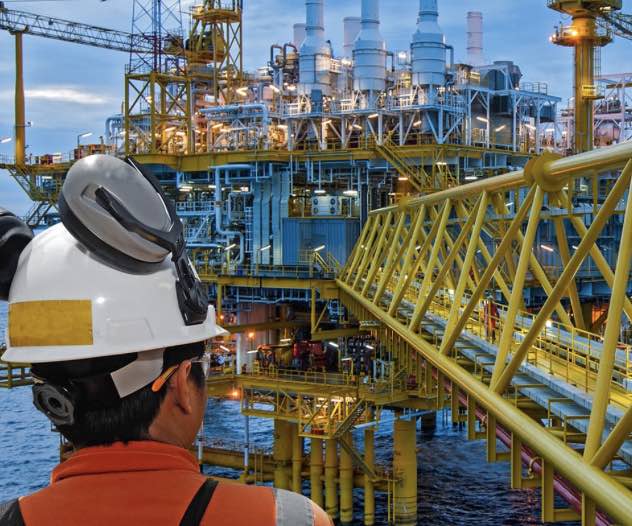
Exploring High Performance Coatings for Offshore...
Offshore and marine structures face relentless...