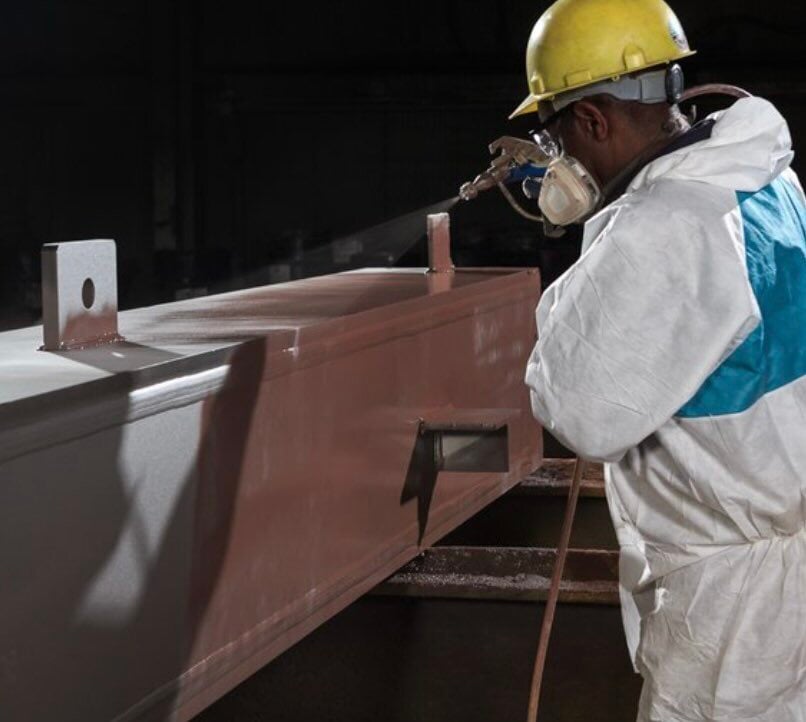
Unlocking the Power of Zinc Primers in High Performance Coating Systems
Explore the transformative role of zinc primers in enhancing the durability and functionality of high performance coatings. Zinc provides cathodic.
- Rick Gilbreath
Explore the transformative role of zinc primers in enhancing the durability and functionality of high performance coatings.
The Essential Role of Zinc Primers in Corrosion Protection
Zinc primers are crucial in safeguarding metal structures from corrosion, which can be both costly and hazardous over time. These primers serve as sacrificial coatings that prevent rust by corroding themselves instead of allowing the underlying metal to deteriorate. The protective layer formed by zinc primers is a result of the oxidation of zinc, which creates a barrier that hinders moisture and oxygen from reaching the steel surface. This process, known as galvanic protection, is essential in extending the lifespan of metal components in various industries, from construction to marine applications.
The use of zinc primers is particularly important in harsh environments where structures are exposed to elements that can accelerate corrosion. The application of a zinc primer is the first line of defense in a coating system designed to provide long-term protection for steel. It is a fundamental step that ensures the integrity and durability of the coated structure, making it an indispensable component in the maintenance and preservation of valuable assets.
Comparative Analysis of Zinc Primers and Other Coating Systems
When it comes to protecting steel structures, the choice of primer can make a significant difference in the performance of the coating system. Zinc primers are often compared to other types of primers, such as epoxy and polyurethane-based formulations. While these alternatives can provide a degree of protection, they lack the self-sacrificing properties of zinc, which is particularly effective in preventing corrosion at cut edges and areas where the coating may be compromised.
The unique chemistry of zinc primers allows them to provide cathodic protection, where the zinc actively sacrifices itself to protect the steel. This is in contrast to barrier coatings, which rely solely on their ability to create a physical shield against corrosive elements. Over time, barrier coatings can fail due to cracking or damage, exposing the steel to the risk of corrosion. Zinc primers, on the other hand, continue to protect the steel even if the topcoat is breached, making them a superior choice for long-term corrosion resistance.
Making Sure Zinc Primers are Listed in Both 055000 and 096000 Sections of the Specification
In the context of construction specifications, the inclusion of zinc primers in both the 055000 (Metal Fabrications) and 096000 (High-Performance Coatings) sections underscores their importance across different stages of a project. By specifying zinc primers in the early stages of metal fabrication, the specifier ensures that the initial layer of protection is applied under controlled conditions, which can greatly enhance the overall performance of the coating system.
The continuity of specifying zinc primers in both sections ensures that the integrity of the corrosion protection strategy is maintained throughout the project. It sets a clear standard for the type of primer to be used, preventing the substitution of inferior products that could compromise the long-term durability of the structure. This attention to detail in the specification process helps to deliver a high-quality finish that is equipped to withstand environmental challenges.
What Happens When Alkyd Primers are Applied in Place of Zinc Primers in the Fabrication Shop
The use of alkyd primers instead of zinc primers in fabrication shops can have significant detrimental effects on the corrosion resistance of steel structures. Alkyd primers, while cost-effective and easy to apply, do not offer the same level of protection as zinc-based coatings. They act as a barrier layer but lack the galvanic properties that enable zinc primers to protect the steel even when the coating is damaged.
When alkyd primers are used as a substitute, they can lead to premature failure of the coating system, resulting in increased maintenance costs and potential structural integrity issues. The initial savings achieved by using alkyd primers can be quickly overshadowed by the long-term expenses associated with repairing or replacing corroded components. It is crucial for specifiers and project managers to recognize the false economy of this approach and insist on the specified use of zinc primers for their superior corrosion protection capabilities.
Value Engineering Quality Out of the Project is Doing the Owner No Favors
Value engineering is often employed to reduce project costs, but when it involves the removal of critical elements such as zinc primers from a coating system, it does a disservice to the project owner. The short-term savings achieved by opting for cheaper materials or processes can compromise the long-term performance and safety of the structure. This approach can lead to increased liability, higher maintenance costs, and reduced asset value.
By maintaining the integrity of the specified high-performance coating system, including the use of zinc primers, project owners can ensure the longevity and durability of their investment. It is imperative that all stakeholders understand the importance of adhering to the original specifications that call for quality products and proper application techniques. Educating owners about the true cost implications of value engineering can help prevent the dilution of performance standards and preserve the value of the structure over time.
Check out these related topics below:
Zinc Primers in Potable Water Applications
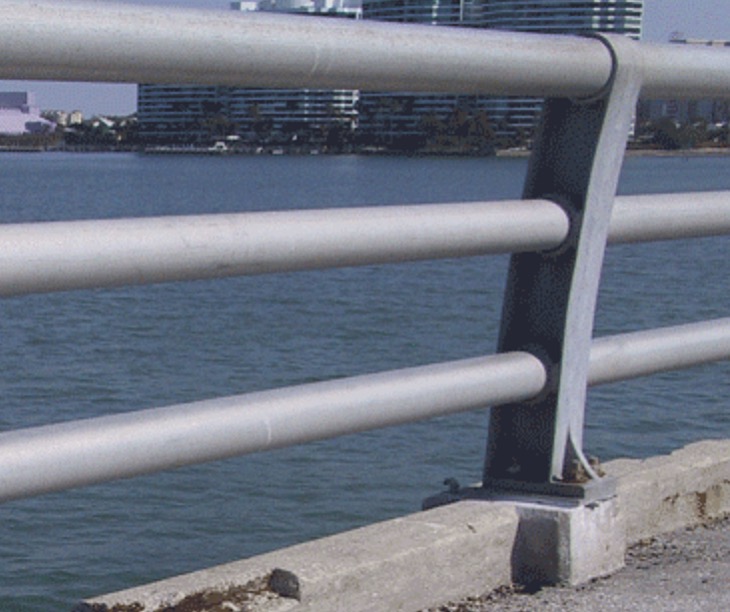
Hot Dipped Galvanized Steel VS Zinc Rich Primer
IF STEEL IS GOING TO BE COATED, A ZINC-RICH...
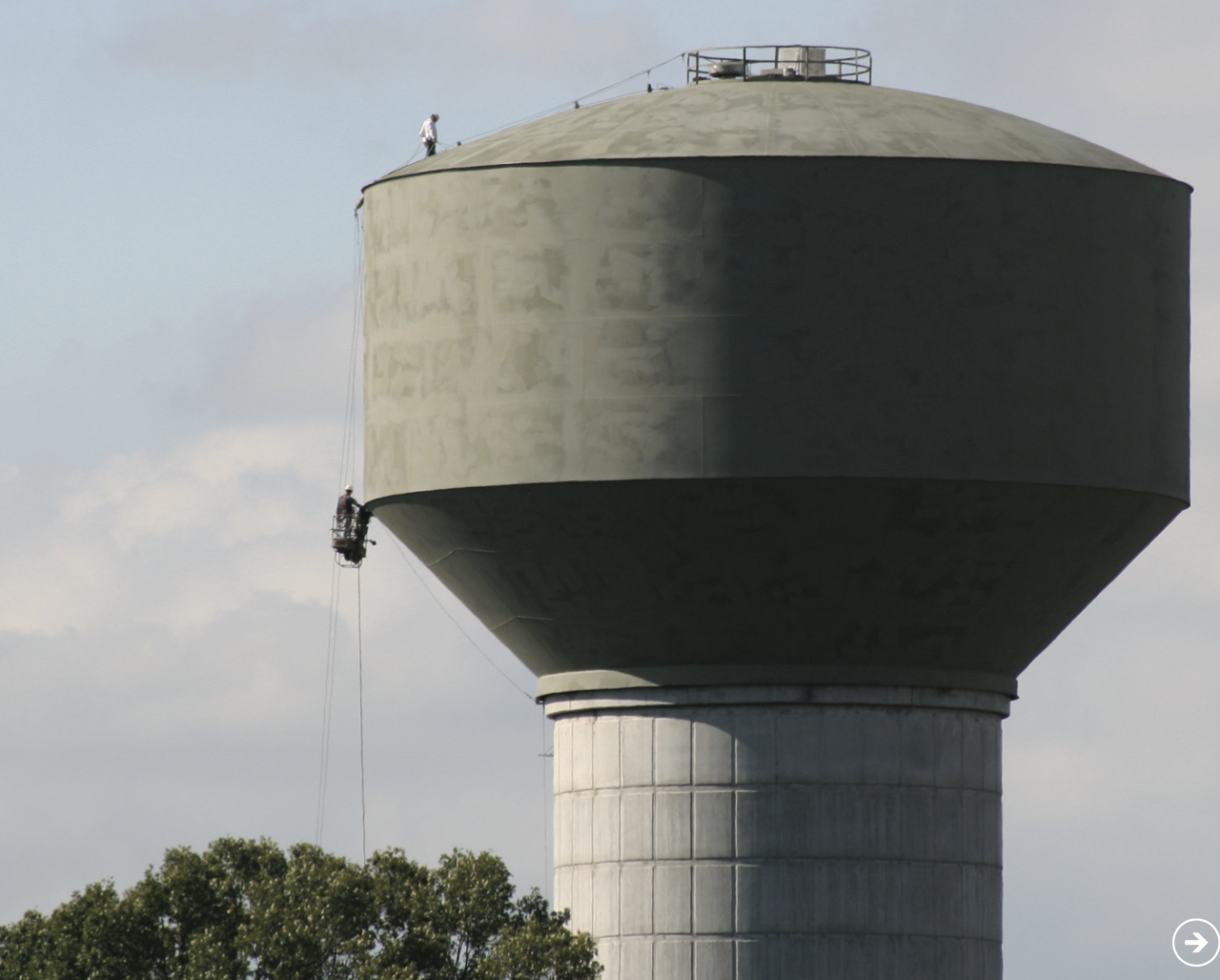
Zinc rich primers in potable water tanks
Zinc Rich Primers In Potable Water Immersion
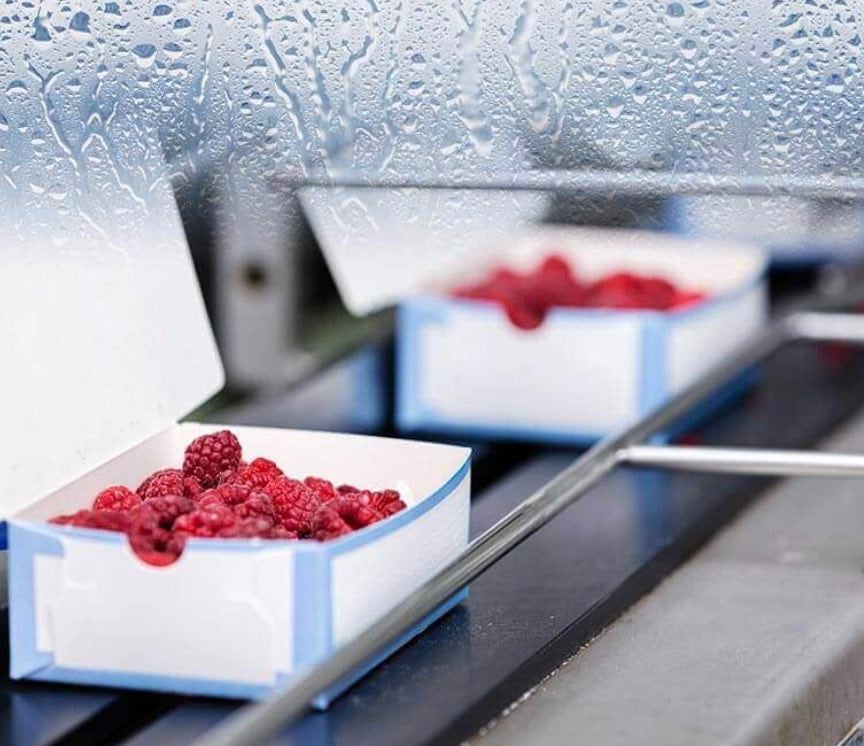
Effective Methods to Prevent Condensation in Food...
Essential techniques to combat moisture getting...