Bellingham Washington Airport Hangar Floor
Upgrading a hangar floor to a high-performance resinous coating system can enhance durability, aesthetics, and overall functionality.
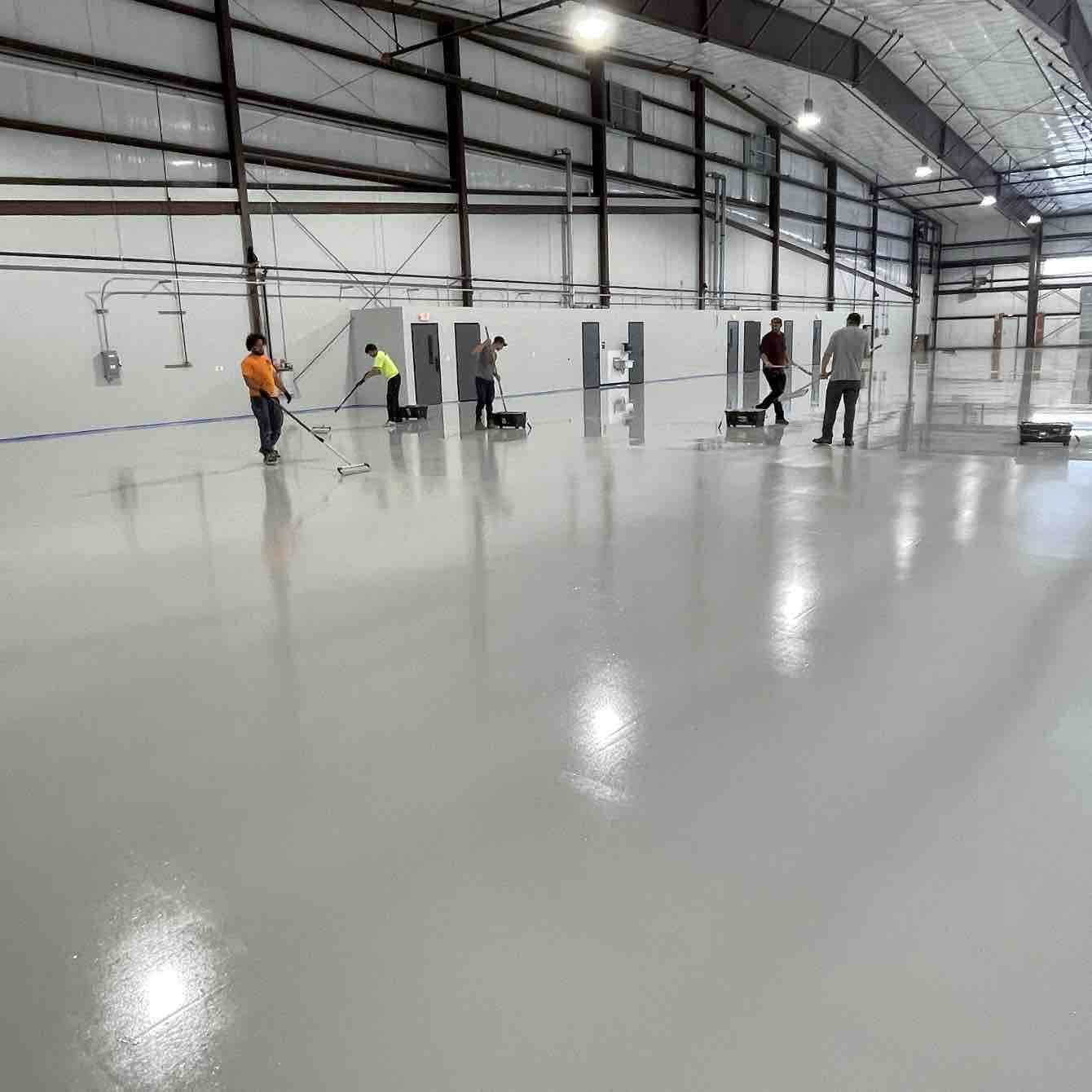
PROJECT INFORMATION
Project Location
Bellingham WA
Project Completion Date
July 2023
Contractor
Foundation Restoration
This project was undertaken for a private aviation hangar in Bellingham, Washington. The client sought to upgrade their hangar flooring to a high-performance resinous coating system to enhance durability, aesthetics, and overall functionality. The selected coating system comprised Tnemec Series 205 Primer, Series 222 Epoxy Intermediate Coat, and Series 248 wear resistant Topcoat.
Project Execution:
Site Assessment and Preparation:
A comprehensive site assessment was conducted to evaluate the existing condition of the hangar floor. Surface preparation included thorough cleaning and mechanical abrasion to ensure optimal adhesion for the subsequent epoxy layers. "We spent a great deal of time working with the General Contractor and owner to ensure we were installing the right system to meet their usage requirements", stated Matt Shaver with Foundation Restoration. "We also installed several mock-ups onsite so the owners could participate with the aesthetic value of the finished floor".
Primer Application (Tnemec Series 205):
Tnemec Series 205 Primer, a high-quality epoxy primer, was applied to the prepared surface. This primer played a crucial role in promoting adhesion and enhancing the bond between the substrate and the subsequent epoxy layers. It also provided a seal to help prevent outgassing.
Epoxy Intermediate Coat (Tnemec Series 222):
Following primer application, Tnemec Series 222 Epoxy Intermediate Coat was applied. This layer provided exceptional protection against chemicals, abrasion, and wear, while also imparting structural integrity to the flooring system.
Topcoat Application (Tnemec Series 248):
The final stage involved applying Tnemec Series 248 Topcoat, a premium urethane topcoat formulated with a very specific sieve size of aluminum oxide. The topcoat added an aesthetic touch while offering heightened resistance against UV exposure, chemicals, and abrasion resistance.
Curing and Quality Assurance:
Each step in the above referenced application was allowed to cure according to manufacturer requirements. Rigorous quality checks were conducted to ensure the coating system met the required standards for adhesion, hardness, gloss, and overall performance.
Project Outcome and Benefits:
Enhanced Durability: The selected resinous coating system significantly improved the durability of the hangar floor, ensuring it can withstand heavy aircraft traffic and equipment movement.
Chemical Resistance: The epoxy layers provided excellent resistance against chemicals like skydrol and hydraulic fluid, ensuring the hangar floor remains protected from potential spills and leaks.
Aesthetic Appeal: The glossy finish of the topcoat enhanced the hangar's appearance, creating a sleek and professional environment for both clients and visitors.
Ease of Maintenance:The seamless and smooth finish of the epoxy coating simplified cleaning and maintenance efforts, contributing to a more efficient operational environment.
"The owner was very happy with the end product, and has already given us another floor. They were impressed with the consistent sheen and finish, compared to other hangars they had done in the past", stated Foundation Restoration General Manager, Morgan Longwell.
Conclusion:
The application of Tnemec Series 205 Primer, Series 222 Epoxy Intermediate Coat, and Series 248 Topcoat successfully revitalized the hangar floor, exceeding the client's expectations in terms of durability, aesthetics, and longevity. The upgraded coating system is expected to serve the hangar efficiently for years to come, ensuring a safe and appealing environment for aviation operations.
LET OUR KNOWLEDGE AND EXPERTISE HELP ENSURE YOUR NEXT PROJECT IS SUCCESSFUL
Check out these other resources
Secondary Containment Coatings- What you need to know
Forklift Traffic on Warehouse Floors
Moisture Vapor Transmission Protection for Concrete Floors
Spalling Concrete and How to Fix It
Floor Coatings Are Not Easy to Specify
Selecting the Right Traffic Coating
Concrete Outgassing and How to Prevent It
Considerations Before Coating Concrete Floors
Selecting Coatings for Secondary Containment
Static Dissipative Floor Coatings
Advantages of Polyurethane Cement Coatings
Exploring Decorative Resinous Flooring Options
UV Resistant Epoxy Floor Coatings
Don't miss these flooring project profiles
Secondary Containment Systems in the Southwest
Manufacturing Facility With Flair
Manufacturing Facility Drum Floors and Walls
Town of Gilbert NWTP Containment
MORE HIGH PERFORMANCE COATINGS PROJECTS
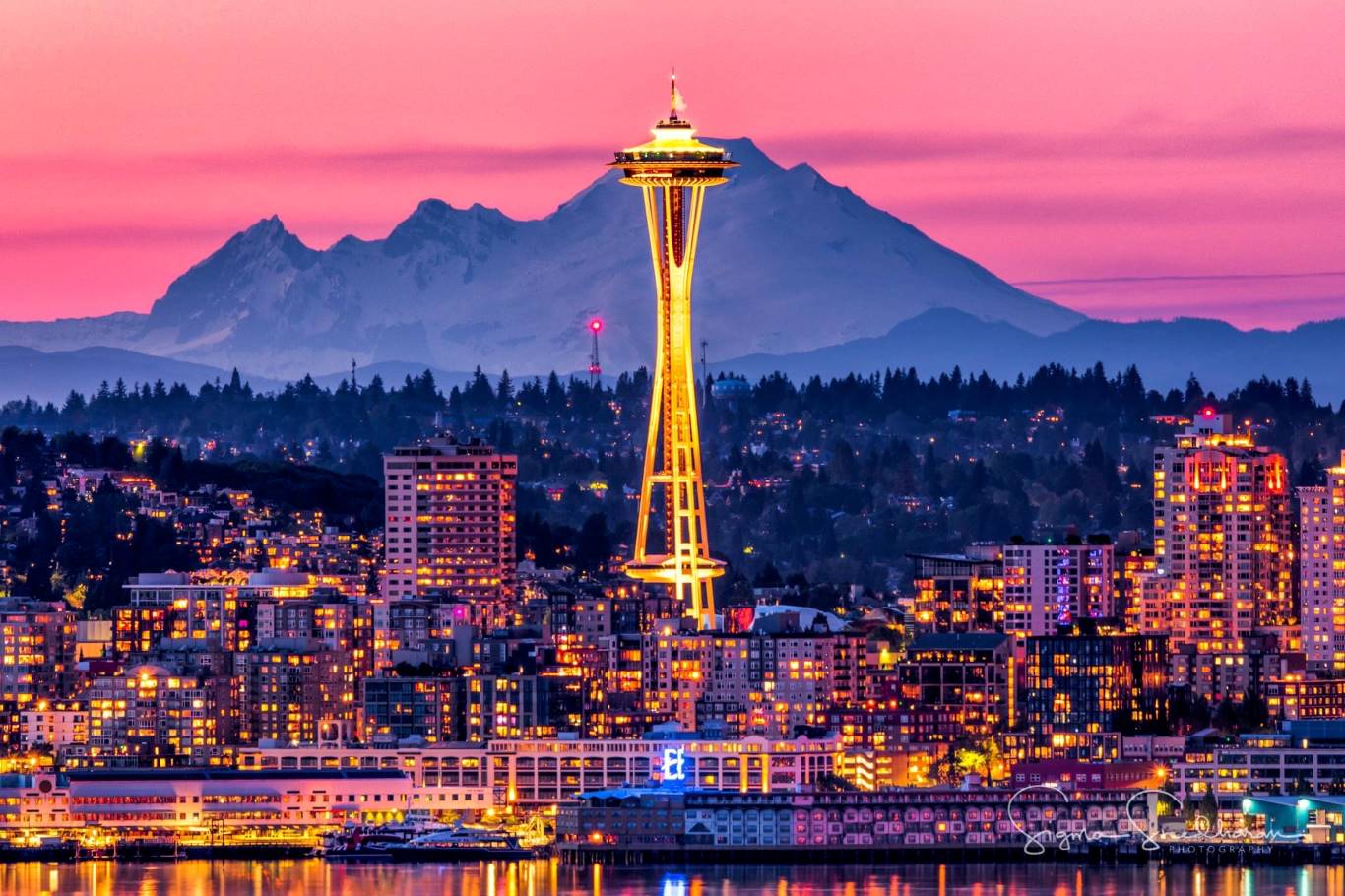
Space Needle Kitchen Refurbishment
In 1959, Seattle hotel executive Edward E. Carlson, who was a chief organizer of the 1962 World’s...
Market Type:
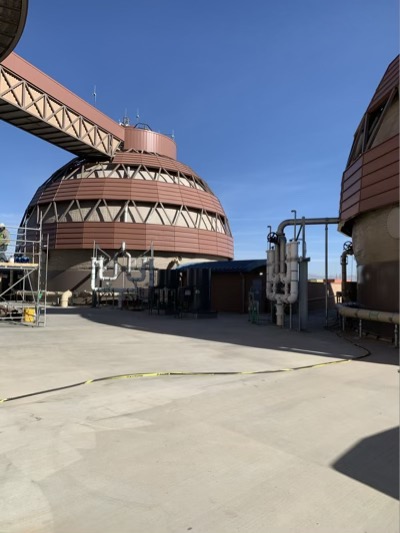
Greenfield water reclamation facility...
The expansion and rehabilitation of the Greenfield Water Reclamation Facility in Mesa, Arizona,...
Market Type:
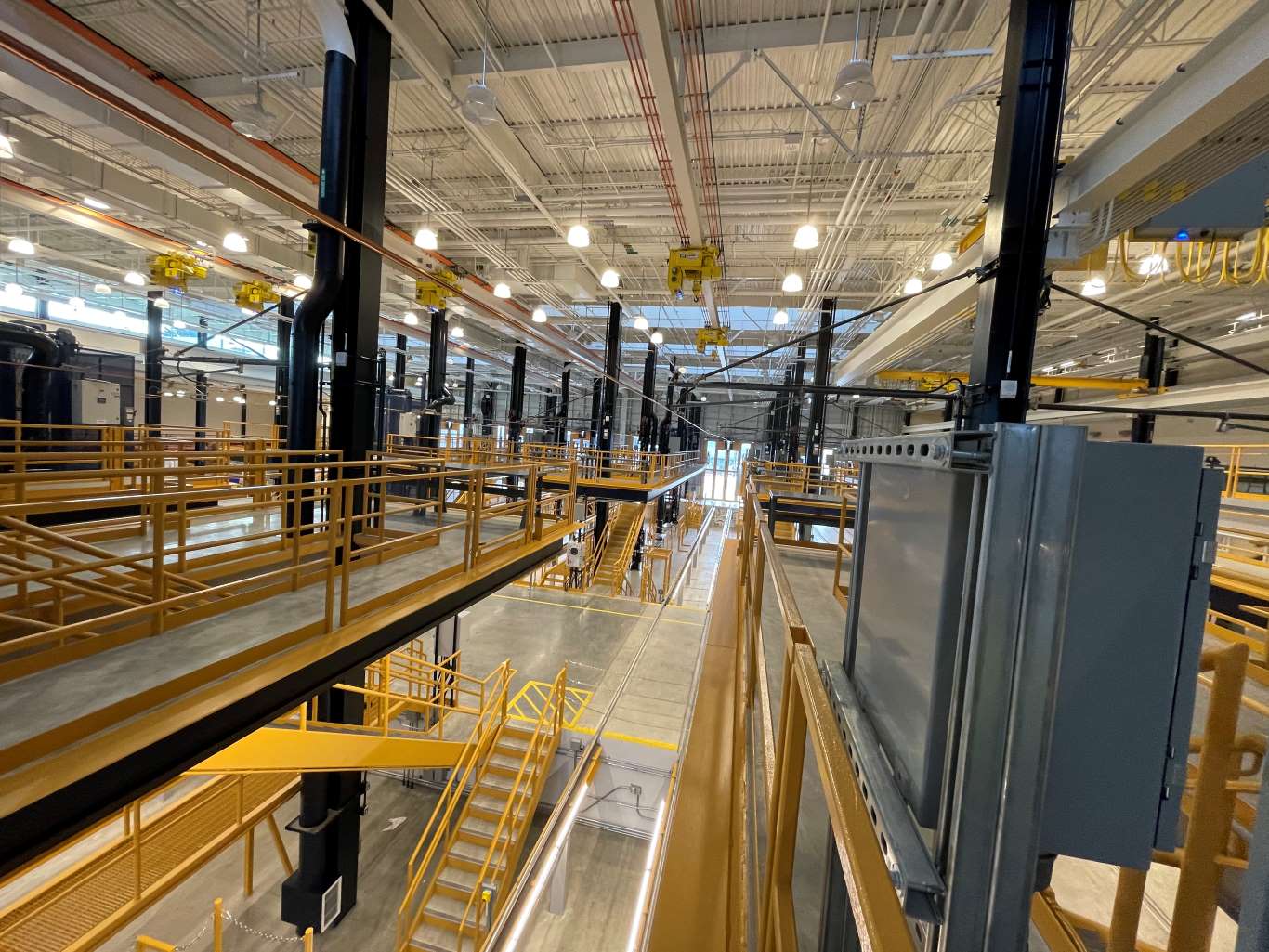
Sound Transit Operations and Maintenance...
As part of Sound Transits massive expansion effort, the Bellevue OMFE (Operations and Maintenance...
Market Type:
OR
LET OUR KNOWLEDGE AND EXPERTISE HELP ENSURE YOUR NEXT PROJECT IS SUCCESSFUL