
What Is SWAT Testing, & Why Is It Important?
Lining systems used in wastewater treatment and transmission systems have evolved over the years to meet the demands created by ever increasingly aggressive exposures.
- High Performance Coatings
Accelerated performance testing of coating and lining materials is integral to product development. Formulators use the results of industry consensus standard laboratory test methods to evaluate a product’s ability to perform in its intended service condition, compare new product formulations to older technologies, compare products of differing generic chemistries for use in similar service conditions, and compare similar products of one manufacturer to those of another manufacturer for the purpose of establishing a standard of quality in a specification. ASTM G 210 “Standard Practice for Operating the Severe Wastewater Analysis Testing Apparatus”, commonly referred to simply as “SWAT” testing, provides formulators with a reliable, reproducible method to determine a product or system’s ability to withstand the demanding service conditions found in modern wastewater treatment and transmission systems. SWAT testing results can also be used by specifiers to define baseline performance requirements for wastewater lining systems.
Lining systems used in wastewater treatment and transmission systems have evolved over the years to meet the demands created by ever increasingly aggressive exposures. Looking back as far as the 1950’s, typical wastewater lining applications primarily employed coal tar epoxy technologies. The Clean Water Act implemented in 1980 began a transformation in wastewater treatment processes by requiring pretreatment of pH regulation and extraction of heavy metals, leading to increased hydrogen sulfide generation in the waste stream. Wastewater systems also began to become more regionalized, necessitating larger facilities and longer transmission distances, all contributing to much more aggressive environments. Finally, odor control and containment measures, largely driven by quality of life concerns in the areas near wastewater treatment facilities, contributed to higher concentrations of hydrogen sulfide in newly created headspaces. All of these measures resulted in wastewater environments that became exponentially more aggressive over a very short period of time.
As the industry came to grips with the need for more robust product applications to withstand the rigors of modern wastewater exposures, it also became clear to coating formulators that older testing protocols used to evaluate products were poorly suited to adequately represent the intended service conditions. Years of study around the lining failure modes observed in wastewater environments led the industry to the conclusion that a laboratory test method that would simulate an aggressive wastewater exposure and yield consistent, reproducible results.
ASTM G 210 was developed specifically to address this need. The key elements of the new test protocol and apparatus are controllable hydrogen sulfide concentrations, cyclic vapor phase and immersion in sulfuric acid and aqueous hydrogen sulfide solution, and elevated temperatures. Test results are reported as the delta of electrochemical impedance spectroscopy (EIS) results from before and after the twenty eight day test duration. EIS values are expressed as a Log Z value at 0.01 Hz, which can be used to determine the product’s permeability. The comparative value before and after the test period further clarify the product’s ability to maintain its permeation resistance under prolonged exposure.
It is generally accepted that a 6.0 Log Z at 0.01 Hz (ohms/cm2) is the level at which protection begins against hydrogen sulfide permeation. However, in actual wastewater exposures, the Log Z at 0.01 Hz value of the lining system can degrade quite quickly. As such, it is important to select a lining system which will exhibit a much higher initial Log Z at 0.01 Hz, and which also will yield the smallest delta between initial and final EIS measurements. Higher initial values with lower delta will yield the longest service life expectancy of the selected lining system.
Tnemec Company’s Perma-Shield line of wastewater lining products was designed and developed specifically to resist permeation in environments with elevated hydrogen sulfide levels. This suite of products includes cementitious repair mortar (Series 217 Mortarcrete), cementitious epoxy resurfacer (Series 218 Mortarclad), 100% solids epoxy mortar lining (Series 434 Perma-Shield H2S), 100% solids fiber reinforced epoxy lining (Series G436 Perma-Shield FR), 100% solids epoxy glaze coat (Series G435 Perma-Glaze), and 100% solids ceramic epoxy pipe lining (Series 431 Perma-Shield PL). Perma-Shield products have been used extensively in severe wastewater environments for nearly twenty years, providing unmatched protection in the toughest exposures. Your local Tnemec Company representative agency can assist you with specification development to ensure your project is designed for maximum performance.
CONTACT HPC TODAY to learn more.
Check out these additional resources on wastewater and water treatment coatings
Ductile Iron Surface Preparation
Engineers- Specifying High Performance Coatings
Coatings for Wastewater Facilities
Don't miss these wastewater and water treatment coating project profiles
Howard Berry Water Treatment Plant
Scottsdale Groundwater Treatment Facility
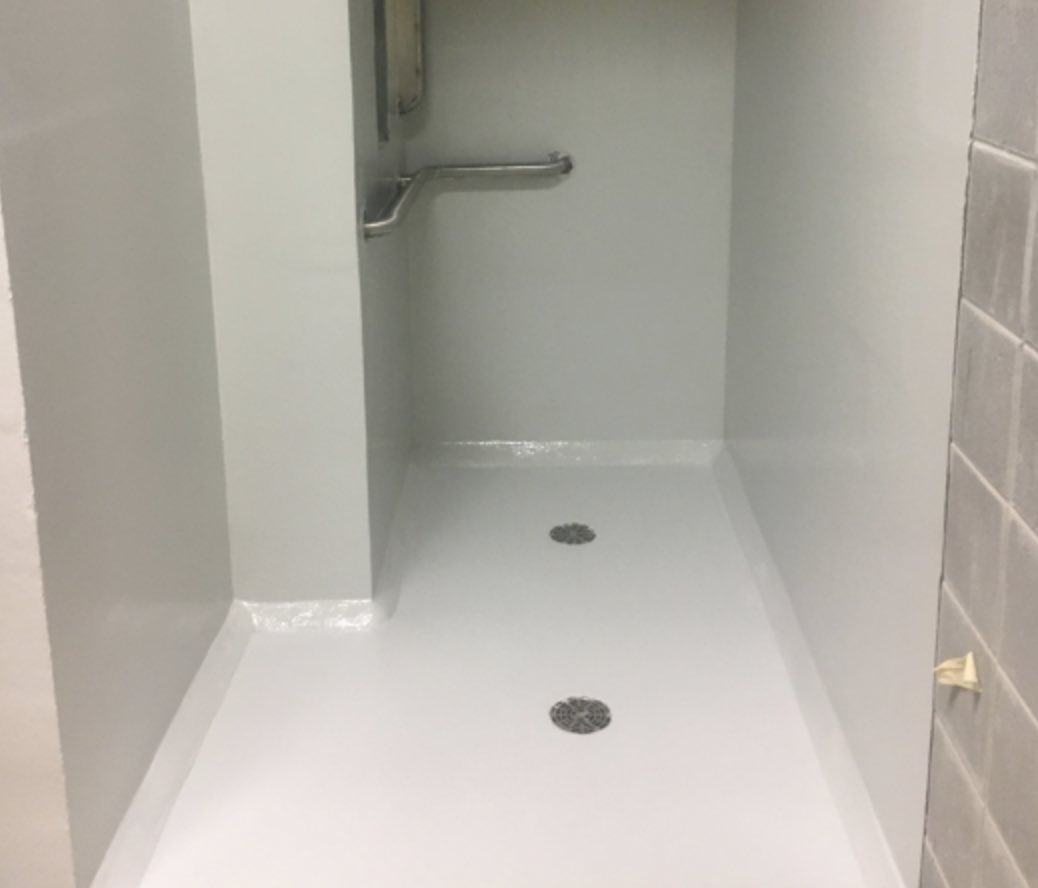
Where to use a Fiberglass Reinforced Wall System
Epoxy mat layup wall systems, like Tnemec...
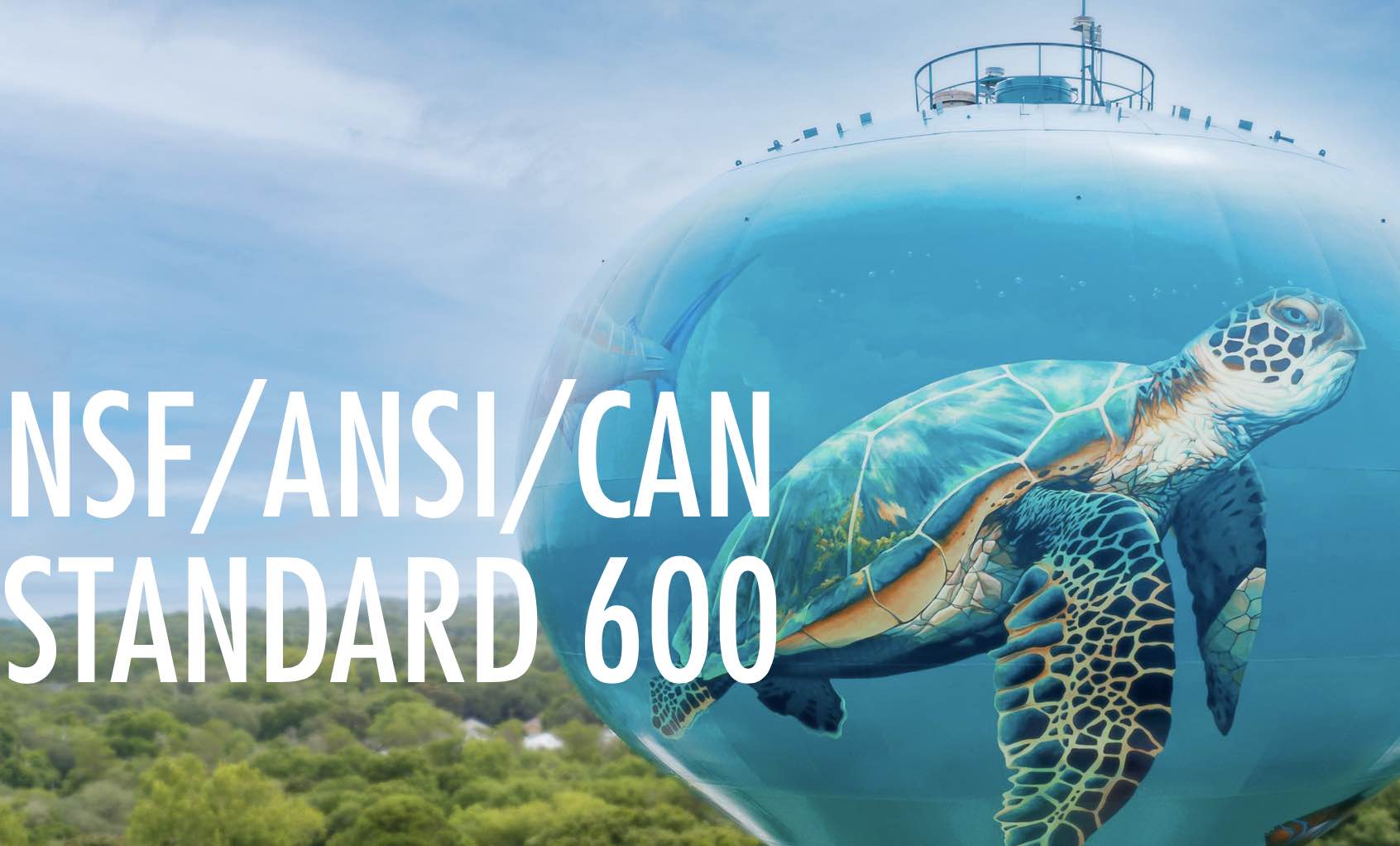
What is NSF / ANSI / CAN 600?
NSF/ANSI/CAN Standard 61 with the NSF 600...
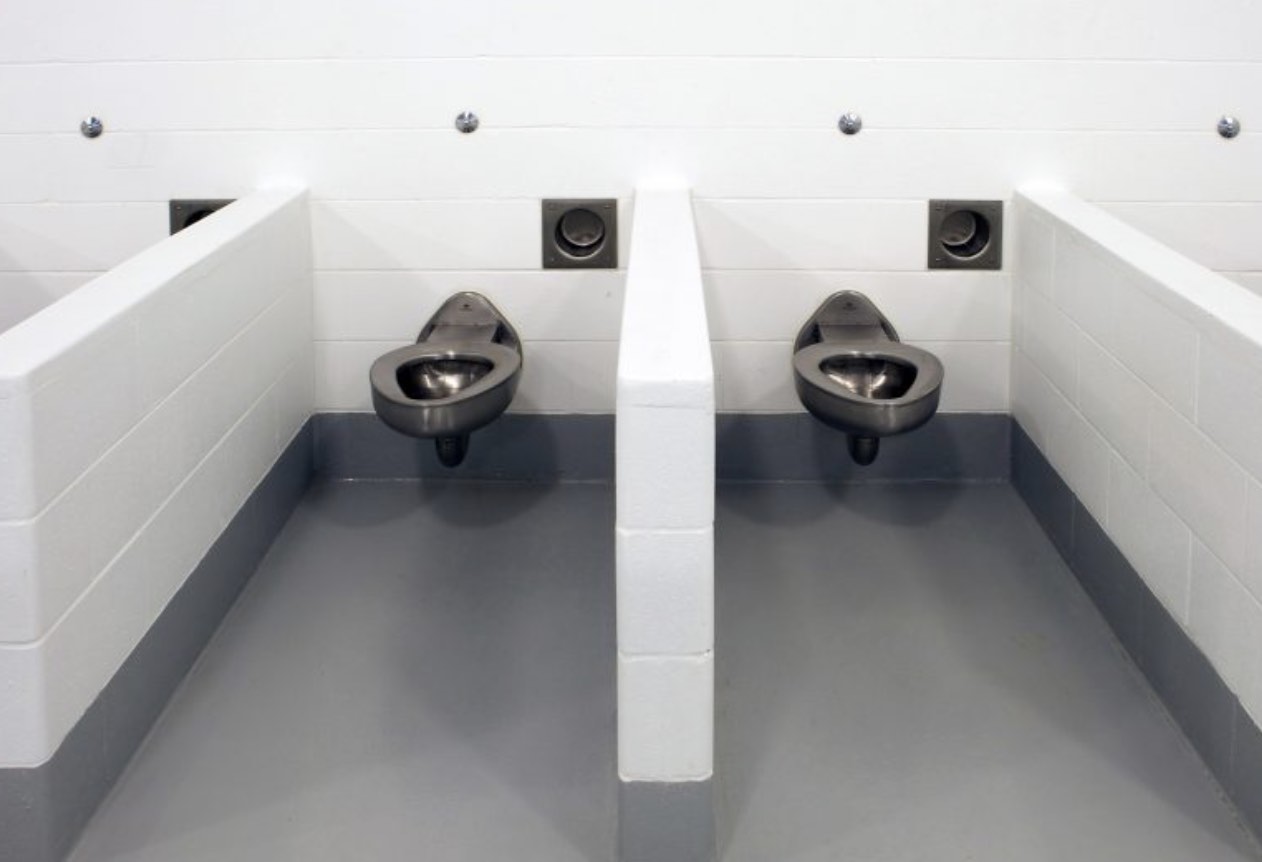
Correctional Facilities Require Coatings That...
Correctional Facilities require coatings that...