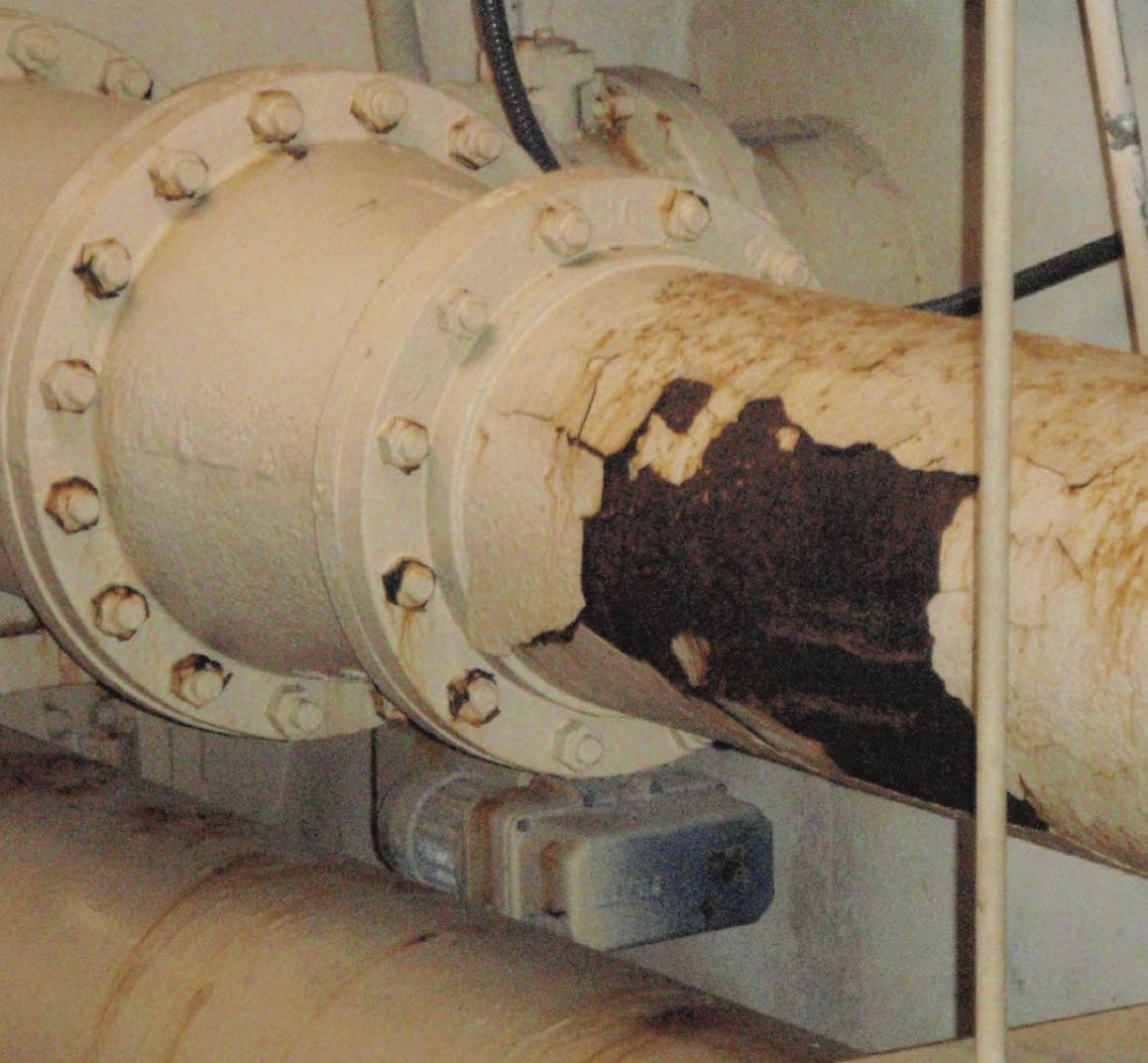
Surface Tolerant Coating Applications
See the benefits and applications of surface-tolerant epoxy mastic coatings for enhancing durability and corrosion protection on various metal surfaces.
- High Performance Coatings
Surface Tolerant Coatings Benefits for Corrosion Protection with Minimal Surface Preparation:
Surface Preparation is typically the most important step when applying high performance coating systems, as it ensures the longevity and effectiveness of the coatings by providing a clean and stable surface for adhesion. However, achieving the ideal surface preparation can be challenging, as abrasive blasting, which is often the preferred method, is sometimes either not feasible or entirely impossible due to various factors such as limited site access, strict environmental regulations, or the presence of sensitive equipment that cannot be exposed to abrasive materials. In such challenging scenarios, surface tolerant products, like Tnemec’s ProTuff Series 132, Series 133, Series 135, or Series 138, can be specified as viable alternatives. These advanced formulation products are specifically designed for application over surfaces with tightly adhered corrosion and marginally prepared or previously coated steel, making them highly adaptable to less-than-ideal conditions. These materials are versatile and can also be used as a primer or intermediate coat under weatherable finishes, providing an additional layer of protection and durability.
Tnemec Company Inc.’s ProTuff epoxies are engineered to be applied at low temperatures, even below dew point conditions, and on damp surfaces, which significantly broadens their applicability in various environmental conditions. Their exceptional ability to adhere to substrates with less than thorough surface preparation protocols, such as SSPC-SP2 Hand Tool or SSPC-SP3 Power Tool, makes these coating types extremely useful in mitigating the high cost and environmental impact associated with containment and blasting operations, offering a practical and efficient solution for maintaining the integrity of coated surfaces.
Benefits of Surface Tolerant Epoxy Mastic Coatings:
- Reduced downtime and labor cost: By minimizing the need for extensive surface preparation, these coatings allow for quicker application processes, which in turn reduces the time facilities need to be offline. This efficiency translates into lower labor costs and less disruption to operations, making it a cost-effective solution for maintenance projects.
- Apply over old coatings & tightly bonded rust: These coatings are engineered to adhere effectively to surfaces that have existing coatings or tightly bonded rust, eliminating the need for complete removal of previous layers. This capability not only saves time but also preserves the integrity of the underlying structure, providing a practical solution for extending the life of aging infrastructure.
- Low-temperature cure: Designed to cure at lower temperatures, these coatings can be applied in environments where traditional coatings might fail. This feature is particularly beneficial in colder climates or during winter months, ensuring that maintenance schedules are not delayed due to temperature constraints.
- Damp-tolerant application capabilities: The ability to apply these coatings on damp surfaces expands their usability in various environmental conditions, such as high humidity or after rainfall. This flexibility ensures that projects can proceed without waiting for ideal weather conditions, thus maintaining project timelines.
- Corrosion and chemical resistance: These coatings offer robust protection against corrosion and chemical exposure, safeguarding metal surfaces from harsh environmental factors and chemical spills. This resistance is crucial for industries such as chemical processing, marine, and wastewater treatment, where exposure to corrosive elements is common.
- Easy and versatile application – brush, roll or spray: The coatings can be applied using a variety of methods, including brushing, rolling, or spraying, which allows for adaptability to different project needs and surface geometries. This versatility ensures that even complex structures can be coated efficiently and effectively.
- High-build capabilities: With the ability to achieve thick layers in a single application, these coatings provide enhanced protection and durability. The high-build nature ensures that surfaces are well-protected against physical wear and environmental damage, extending the lifespan of the coated materials.
Difficulties and Hazards of Surface Tolerant Coatings
Certainly, the practice of overcoating aged systems introduces a unique set of challenges and potential risks that must be carefully managed. When considering the application of surface tolerant coatings, it is absolutely essential for specifiers to have a comprehensive understanding of several critical factors. These include the environmental tolerances of the coatings, which dictate the conditions under which they can be effectively applied and cured, as well as a thorough assessment of the existing coating system's condition. This involves evaluating the adhesion values, which measure how well the current coating is bonded to the substrate, and determining whether it can support an additional layer without compromising its integrity. Neglecting to fully grasp these aspects can result in severe issues, such as the complete delamination of both the existing and newly applied coatings. This delamination can lead to costly repairs, increased downtime, and potential damage to the underlying structure. Therefore, it is highly advisable to consult with a local High Performance Coating Consultant. These experts can provide invaluable guidance on assessing whether an existing coating is suitable for an overcoat application, ensuring that the new coating will adhere properly and perform as expected. They can also offer insights into the best practices for preparing the surface and selecting the appropriate products to achieve optimal results.
In short, surface-tolerant epoxy mastic coatings can offer Owners, Engineers, Architects, and applicators enhanced durability and corrosion protection for a wide range of previously coated metal surfaces, making them incredibly versatile for maintenance in any environment. These coatings are engineered to withstand harsh conditions and provide a robust barrier against environmental factors that can lead to deterioration. From pipe galleries, where moisture and temperature fluctuations are common, to power plants, which require high-performance solutions to withstand extreme operational demands, surface-tolerant epoxy coatings from Tnemec Company Inc. have a long-standing history of providing customers with reliable, time-tested protection.
Whether applied as stand-alone systems or in conjunction with high-performance topcoats, these coatings ensure that structures remain resilient and functional over time. In the end, these advanced epoxy products will not only serve to extend maintenance cycles, reducing the frequency and cost of repairs, but also keep your facilities online, minimizing downtime and operational disruptions. By safeguarding your valuable assets, these coatings contribute to the longevity and efficiency of your infrastructure, ensuring that it continues to perform optimally in the face of challenging conditions.
CONTACT US for assistance in selecting the proper surface tolerant primer and for help in evaluating the existing coatings and conditions on your project.
Check out our related resources on this topic:
The Importance of Surface Preparation with High Performance Coatings
Surface Preparation of Ductile Iron Pipe & Fittings
Ultimate Guide to Surface Tolerant Epoxies
Determine What Coatings to Use Where
Don't miss these project profiles
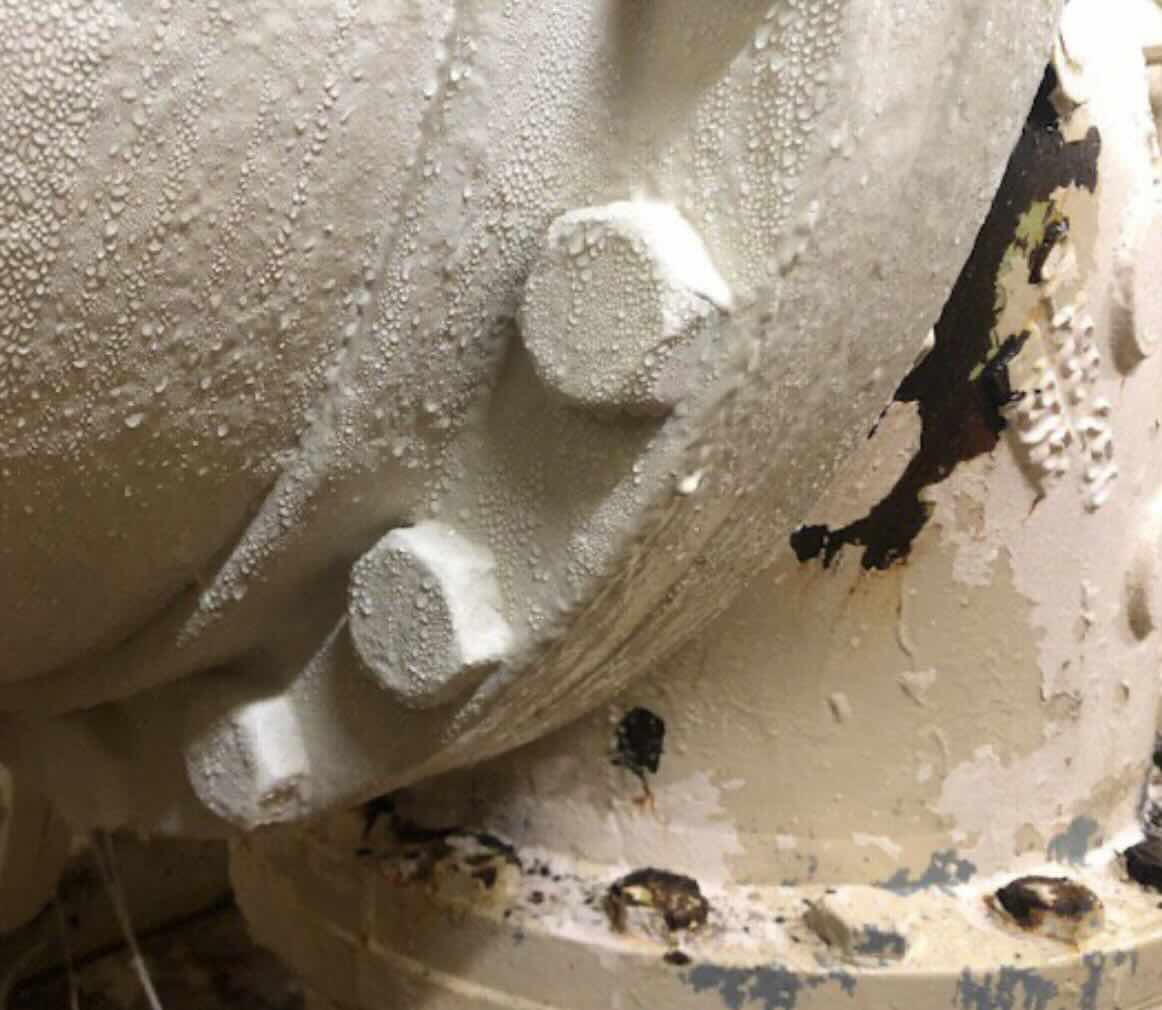
Ultimate Guide to Surface-Tolerant Epoxy Coatings
Discover the resilient world of surface-tolerant...
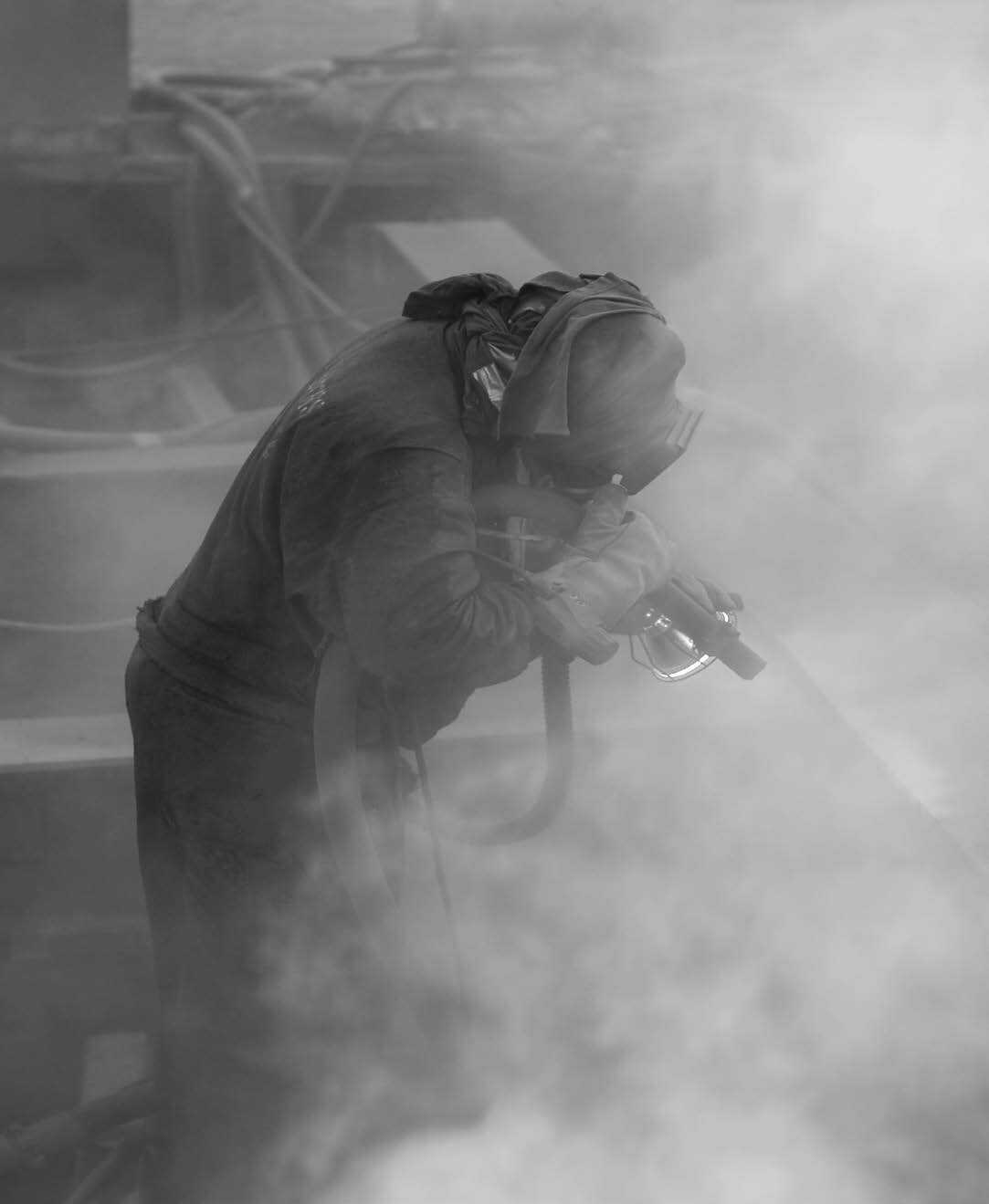
Choosing Surface Preparation Standards
The efficacy of any coating system begins with...
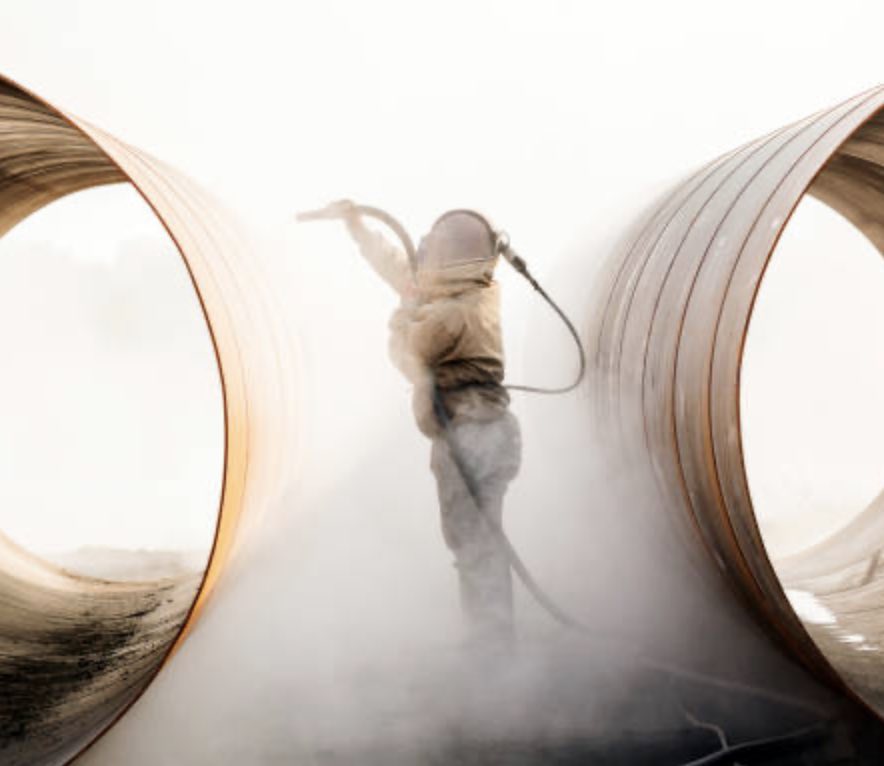
Is Surface Preparation the Most Important Part of...
Surface preparation is critical when using...