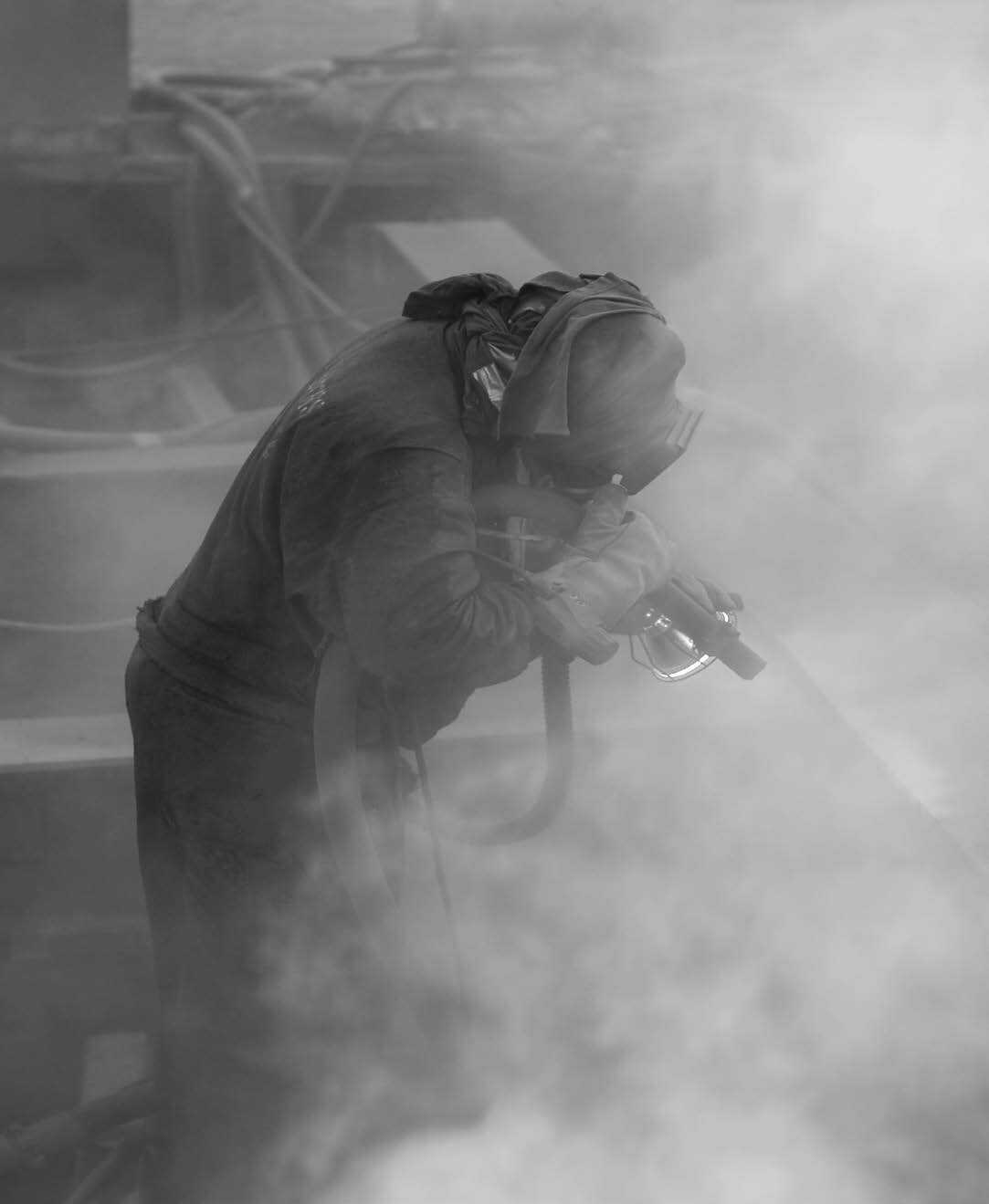
Choosing Surface Preparation Standards
Unlock the secrets to flawless coatings with top-notch surface preparation standards.
- Buddy Stanford
The efficacy of any coating system begins with specifying appropriate surface preparation standards.
The Importance of Surface Preparation in Coating Durability
Surface preparation is arguably the most critical step in the application of high-performance coatings. It directly impacts the adhesion, longevity, and overall effectiveness of the coating. Without proper surface preparation, even the most advanced coatings can fail prematurely, leading to costly repairs and maintenance.
Proper surface preparation ensures that contaminants, rust, and other surface imperfections are removed, allowing the coating to bond effectively with the substrate. This process not only enhances the durability of the coating but also improves its resistance to environmental factors such as moisture, UV radiation, and chemical exposure.
Surface Preparation Standards: An Overview
There are many recognized industry consensus standards for surface preparation, each designed to meet specific requirements and industry needs. These standards provide guidelines for achieving the desired level of cleanliness and surface profile necessary for optimal coating performance.
Some of the most commonly referenced standards include those published by the Association for Materials Protection & Performance (AMPP), the International Concrete Repair Institute (ICRI), the National Association of Pipe Fabricators (NAPF), and International Organization for Standardization (ISO), among others. Each of these organizations offers detailed specifications for various surface preparation methods, including abrasive blasting, mechanical abrasion, waterjetting, chemical cleaning, and hand tool & power tool cleaning.
Types of Surface Preparation
Surface preparation requirements can include many different methods, types of equipment, degrees of cleanliness, depending on the intent of the application. Below is an outline of types of preparation often specified for various substrates:
Substrate | Preparation Types | Common Reference Standards |
Metals (Ferrous & Non-Ferrous) | Abrasive Blast, Hand & Power Tool Cleaning, Solvent Cleaning | SSPC/NACE, ISO |
Concrete | Abrasive Blast, Mechanical Abrasion, Chemical Etching | SSPC/NACE, ICRI |
Ductile Iron Pipe | Abrasive Blast, Hand & Power Tool Cleaning, Solvent Cleaning | NAPF |
Selecting and Utilizing the Appropriate Standards
Surface preparation standards are generally crafted to address the specific requirements of preparing different substrates. SSPC/NACE standards are frequently cited for both ferrous and non-ferrous metals, while a combination of SSPC/NACE and ICRI Technical Guidelines is typically used for concrete. To determine the appropriate surface preparation for your specification, the best starting point is to consult the product data and application guide literature provided by the coating system manufacturer. Usually, the manufacturer will specify the suitable preparation standards for all relevant substrates.
It is crucial to follow the coating system manufacturer's published guidelines to ensure they will support the application as specified. Manufacturers are unlikely to issue or honor warranties for coating systems that are specified or applied using non-conforming preparation methods.
Once the appropriate surface preparation method for your application has been identified, it is adviseable to utilize the approprate standard as a reference within your specification, along with any clarifying notes suggested by the manufacturer, rather than to attempt to capture the provisions of the referenced standard within your specification. For example, surface preparation of concrete is often specified by reference to SSPC-SP 13/NACE No. 6 (Cleanliness) and ICRI Technical Guideline No. 310.2R (Surface Profile) as follows:
Shot blast, abrasive blast, or mechanically abrade referencing SSPC-SP 13 Surface Preparation of Concrete to produce a uniform surface profile referencing ICRI CSP 5 or greater.
In this case, the specifier uses the clarifying note "Shot blast, abrasive blast, or mechanically abrade" to refine the acceptable methods to achieve cleanliness indicated by the SP 13 standard, while referencing ICRI to define surface profile. This inclusion is complete without further modification for surface preparation of concrete prior to application of many high-build resinous floor coating systems.
Conclusion
When formulating your coating system specification, it is important to keep in mind that standards are tailored to different substrates. Consult manufacturer guidelines to ensure proper preparation and warranty compliance. Reference appropriate standards in specifications, using clarifying notes as needed.
Check out these additional resources:
The Importance of Surface Preparation
Surface Preparation of Ductile Iron Pipe & Fittings
Can Galvanized Steel Be Coated?
Is Surface Preparation the Most Important Part of a Coating System?
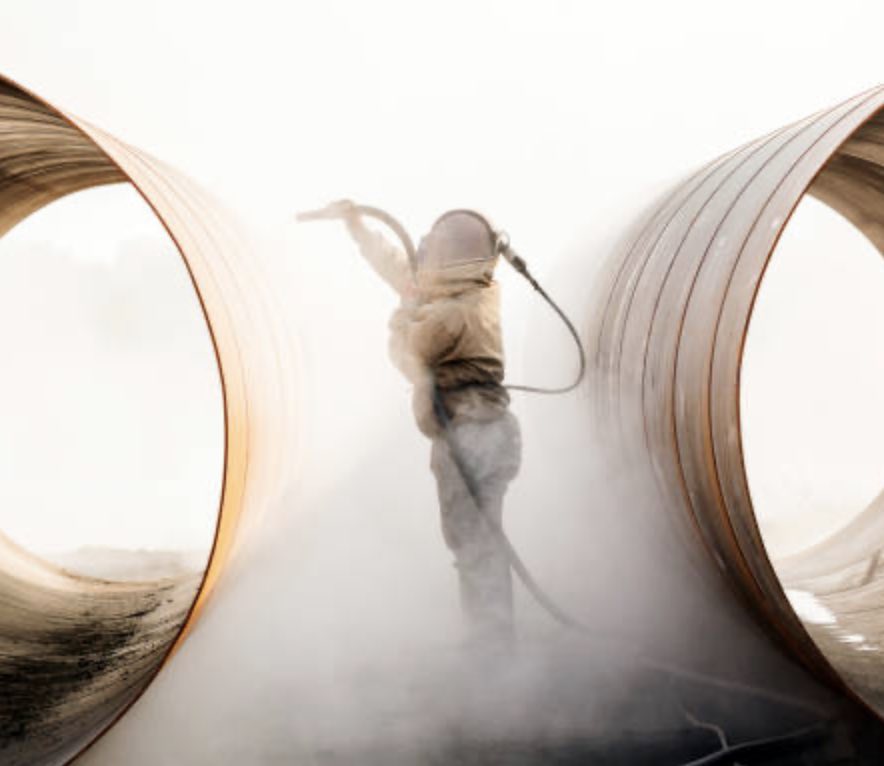
Is Surface Preparation the Most Important Part of...
Surface preparation is critical when using...
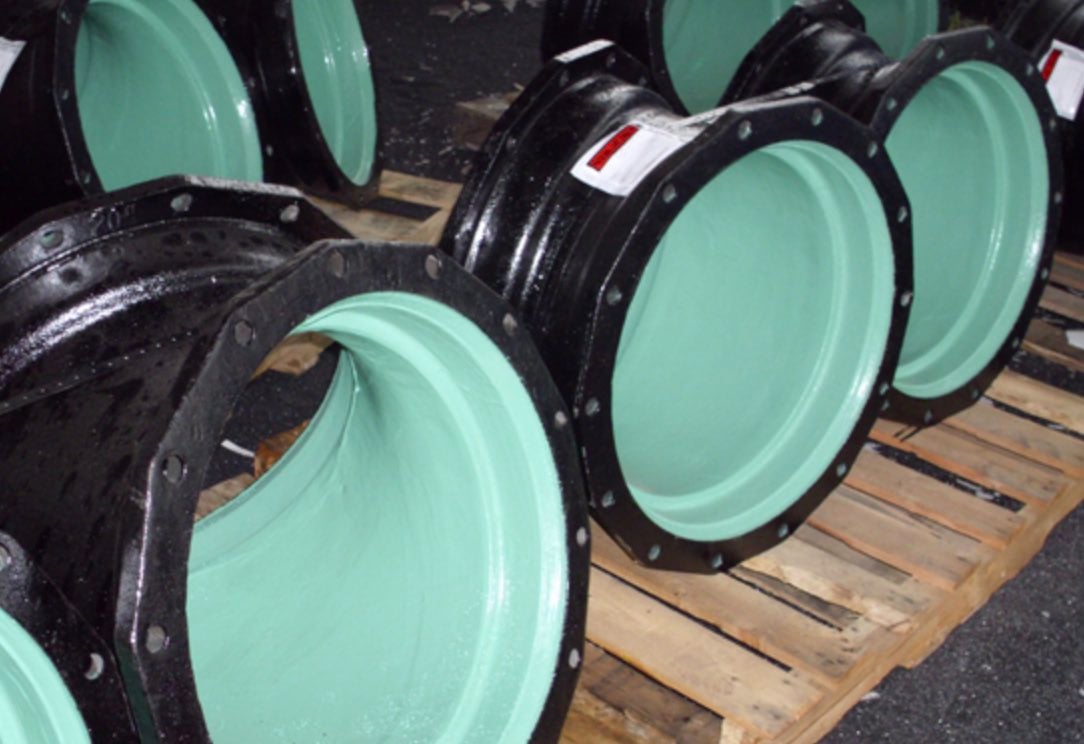
Surface Preparation of Ductile Iron Pipe &...
The foundation of any effective high-performance...
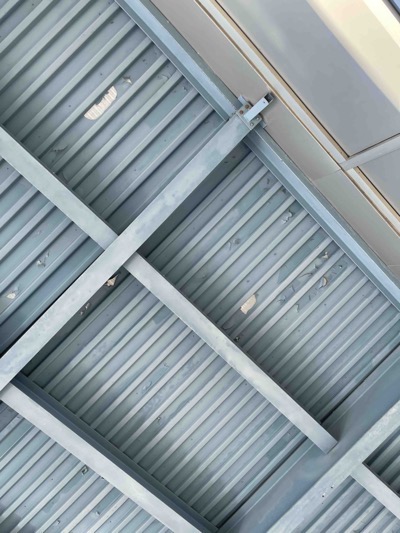
Can galvanized steel be coated?
What is Passivation on Galvanized Steel and Can...