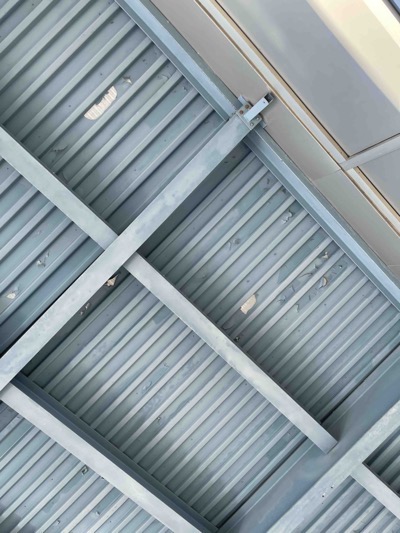
Can galvanized steel be coated?
When utilizing a duplex coating system, passivated galvanized steel can cause early coating failure if it is not prepared properly.
- High Performance Coatings
What is Passivation on Galvanized Steel and Can it Be Coated?
Passivation, sometimes referred to chromating, is a treatment often utilized by galvanized deck suppliers to prevent the formation of zinc salts, white rust and wet storage stains during stacking and transportation of galvanized deck panels. Passivation, and related oil treatments are likely to cause coating adhesion issues if they aren’t mitigated or removed properly prior to the application of the specified coating.
(Example of early failure of a duplex coating system on unprepared galvanized steel)
SSPC-SP 16 Brush-Off Blast Cleaning of Coated and Uncoated Galvanized Steel, Stainless Steels, and Non-Ferrous Metals, 4.3.3 details how to check a surface for oils and passivation using a copper sulfate testing kit.
- Ensure that surfaces are free of any visible oxidation or oxidation by-products.
- Prepare the solution by dissolving 2 grams of copper sulfate crystals in 100 ml of deionized water.
- Mark off three adjacent areas on the galvanized part, approximately 6.45 cm² (1 inch²).
- Leave one area untouched, solvent wash the second and third areas, and also thoroughly sand the third area using emery paper.
- Using an eyedropper or pipette, saturate a cotton swab with the copper sulfate solution and apply to all three areas, or apply the solution directly to the three areas.
If all three areas turn black immediately, there is no passivation on the surface. If the first area does not turn black within 10 seconds and the second and third areas turn black immediately, there is no passivation on the surface with the possible exception of light oil. If the first and second areas do not turn black within 10 seconds and the third area turns immediately, a passivator of some type is present¹.
If the galvanized deck surface is confirmed not to contain any passivation oils, the deck can be primed with a self-crosslinking hydrophobic acrylic similar to Tnemec Series 115 Uni-Bond DF. If the galvanized deck is confirmed to contain passivation treatments, the surface must be cleaned and profiled prior to the application of a high-performance coating.
For aggressive exposure environments or exposures that require a high-performance urethane or fluoropolymer finish coat, two component epoxies similar to Tnemec Series N69 Hi-Build Epoxoline II can be used to prime the prepared deck.
For more information please contact your local high-performance coating consultant.
¹SSPC: The Society for Protective Coatings SURFACE PREPARATION SPECIFICATION SSPC-SP 16 Brush-Off Blast Cleaning of Coated and Uncoated Galvanized Steel, Stainless Steels, and Non-Ferrous Metals
Check out these related resources
Hot Dipped Galvanizing VS Zinc Rich Primers
Why High Performance Coatings Fail
The Importance of Surface Preparation
Don't miss these project profiles
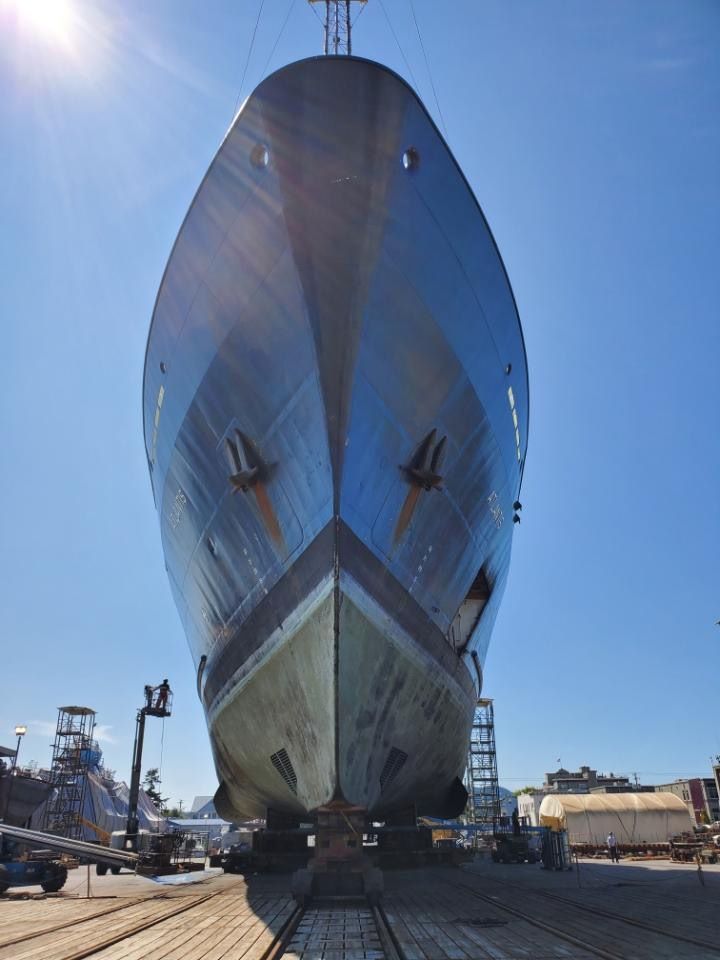
The Declining Performance of Marine Coatings
In the competitive world of marine coatings, a...
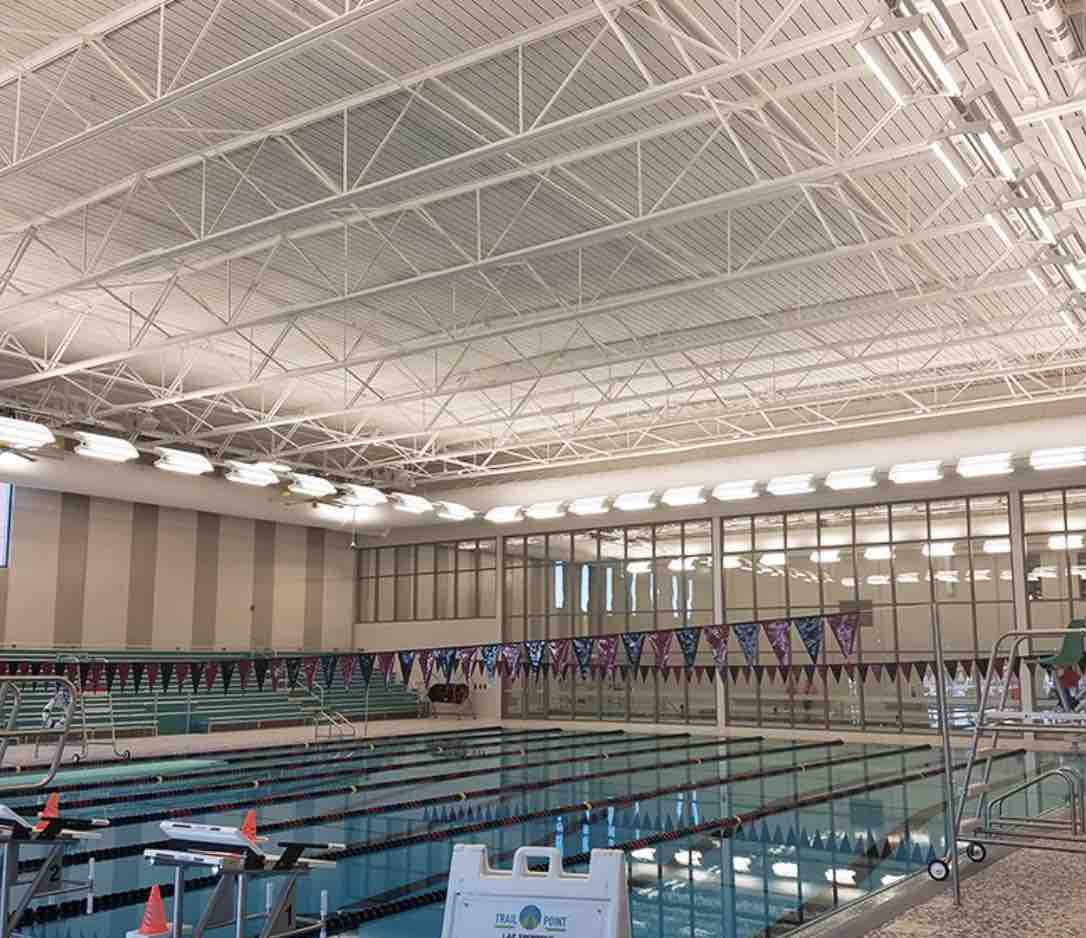
How Do You Know When a High Performance Coating...
The process of determining when a high...
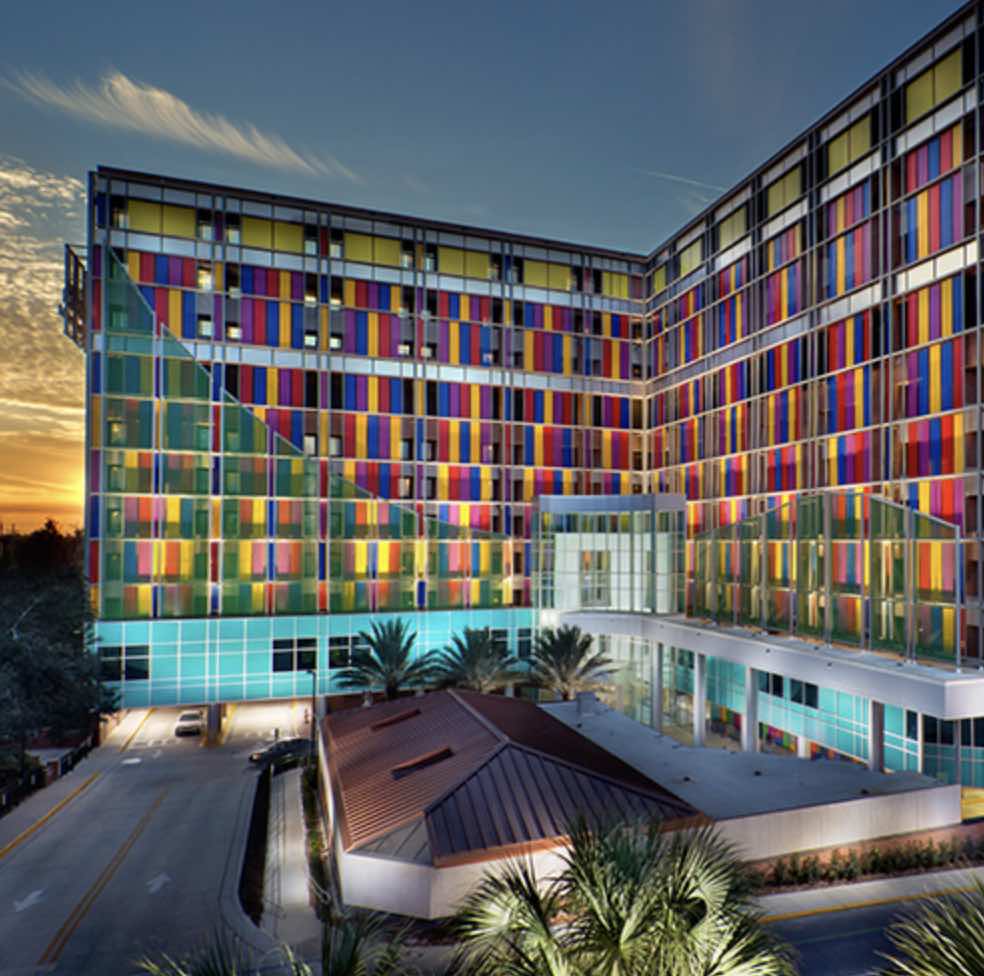
Understanding AAMA 2605 Standards for High...
AAMA 2605 is a stringent performance standard.