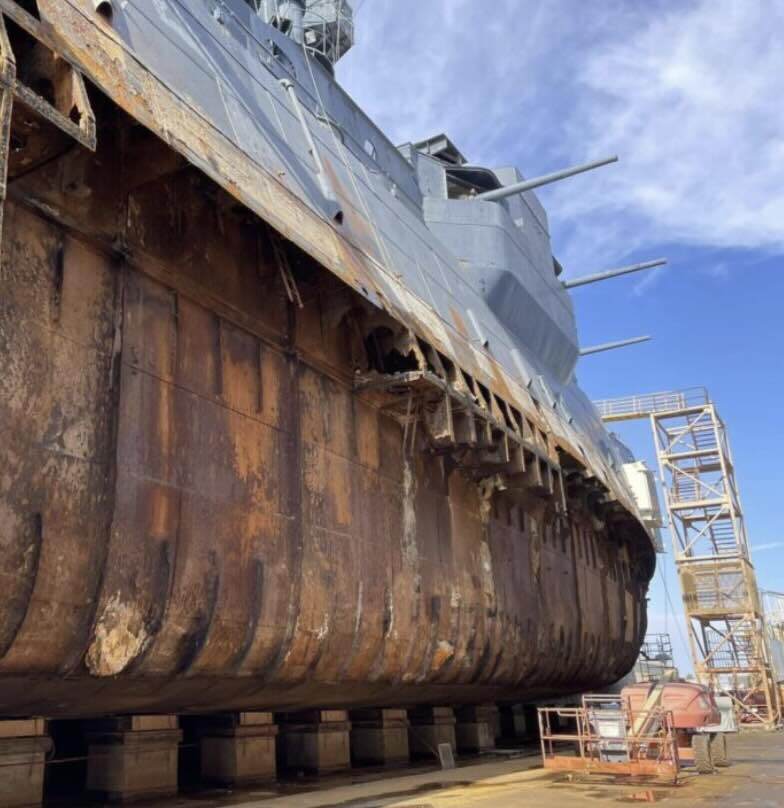
Maximizing Maritime Efficiency by controlling condensation with coatings
Explore how anti-condensation coatings are revolutionizing condensation control on ships, enhancing both the durability and efficiency of maritime operations.
- High Performance Coatings
Explore how anti-condensation coatings are revolutionizing condensation control on ships, enhancing both the durability and efficiency of maritime operations.
Understanding Condensation Challenges in Maritime Environments
Maritime vessels face unique environmental challenges that can severely impact their operation and maintenance. One such challenge is condensation, which occurs when warm, moist air comes in contact with cooler surfaces, leading to water accumulation. This can cause corrosion, mold growth, and deterioration of critical components. Understanding the factors that contribute to condensation aboard ships is crucial for implementing effective control measures.
Effective management of condensation is vital to maintain the structural integrity of a vessel and ensure the safety and comfort of its crew. Anti-condensation coatings play a significant role in addressing these challenges by providing a barrier to temperature changes and reducing the potential for moisture buildup.
The Role of Anti-Condensation Coatings in Enhancing Ship Durability
Anti-condensation coatings are specifically engineered to combat the detrimental effects of condensation on maritime vessels. These coatings can be applied to a variety of surfaces, including hulls, decks, and interior spaces, to prevent heat transfer and mitigate the formation of condensation. By doing so, they not only protect against corrosion and degradation but also contribute to a more stable internal environment.
Moreover, the energy efficiency of ships can be significantly improved with the use of these coatings. This leads to reduced operational costs and a smaller carbon footprint, making anti-condensation coatings an investment in both the longevity of the vessel and environmental sustainability.
Tnemec Series 972, Aerolon Provides Technological Advancement in Anti-Condensation Coatings for Ships
Tnemec Series 972 Aerolon is at the forefront of anti-condensation coating technology, offering superior protection against condensation and thermal bridging. Utilizing a proprietary blend of insulative materials, Aerolon effectively maintains surface temperatures, preventing the conditions that lead to condensation. This innovation represents a significant leap forward in maritime maintenance technology.
The versatility of Aerolon makes it suitable for a wide range of maritime applications, including storage tanks, piping, and other critical infrastructure. Its ease of application and durability under harsh marine conditions make it an ideal solution for both new construction and maintenance projects.
Case Studies: Successful Implementation of Anti-Condensation Coatings in Maritime Operations
Real-world applications of anti-condensation coatings on maritime vessels have demonstrated their effectiveness in managing condensation and enhancing ship performance. Case studies reveal that ships treated with insulation coatings experience fewer maintenance issues related to moisture damage, leading to more reliable operations.
For instance, a fleet of cargo ships coated with anti-condensation coatings reported a significant decrease in corrosion-related repairs, resulting in cost savings and reduced downtime. These case studies serve as powerful testimonials to the benefits of using coatings in the marine industry.
Tnemec Aerolon, Series 972 Drastically Improves Dry Dock Turn-Around Times
One of the most impactful advantages of using Tnemec Aerolon insulation coatings is the reduction in dry dock turn-around times. The quick application and fast curing properties of Aerolon allow for shorter maintenance windows, enabling ships to return to service more rapidly. Many applications require only a single coat to perform similarly to older technologies that may need 4-5 coats.
This efficiency gain not only reduces labor and maintenance costs but also minimizes the time ships spend out of commission, thereby maximizing revenue generation. The implementation of Aerolon Series 972 represents a strategic investment for shipowners and operators aiming to streamline their maintenance processes and enhance overall fleet performance.
Check out our other resources on this topic:
Does formulation and product performance matter?
Writing performance based coating specifications
How Do High Performance Coatings Differ From Regular Coatings, or Paint?
What Considerations Should an Architect Make Before Spec'ing Coatings
Preventing Condensation in Food Plants
Don't miss these Aerolon project profiles
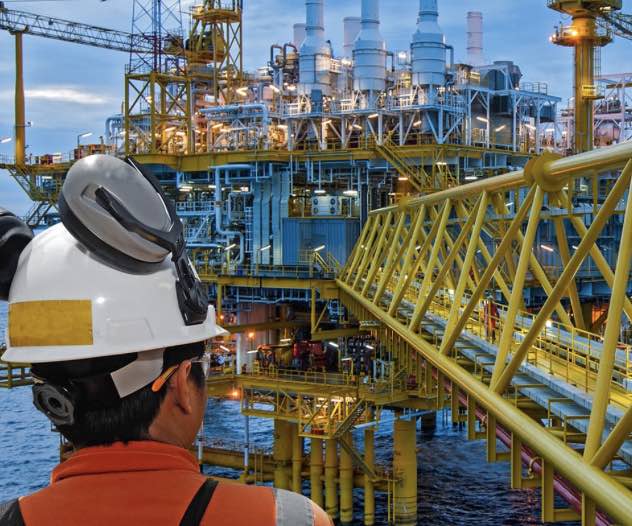
Exploring High Performance Coatings for Offshore...
Offshore and marine structures face relentless...

Exploring High Performance Coatings in Aerospace...
Aerospace engineering demands exceptional...
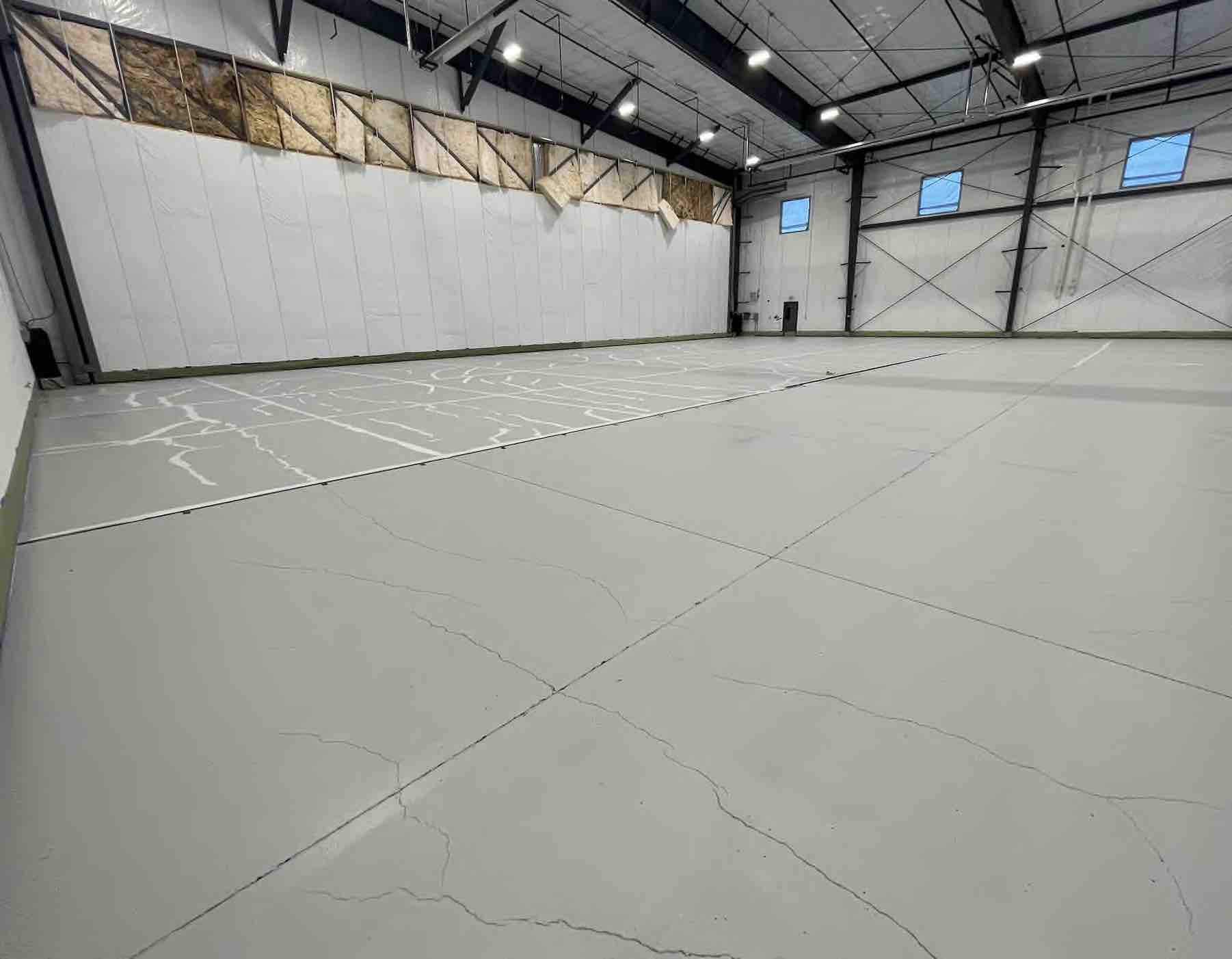
What Should be Considered Before Coating Concrete...
Before coating concrete floors, there are several...