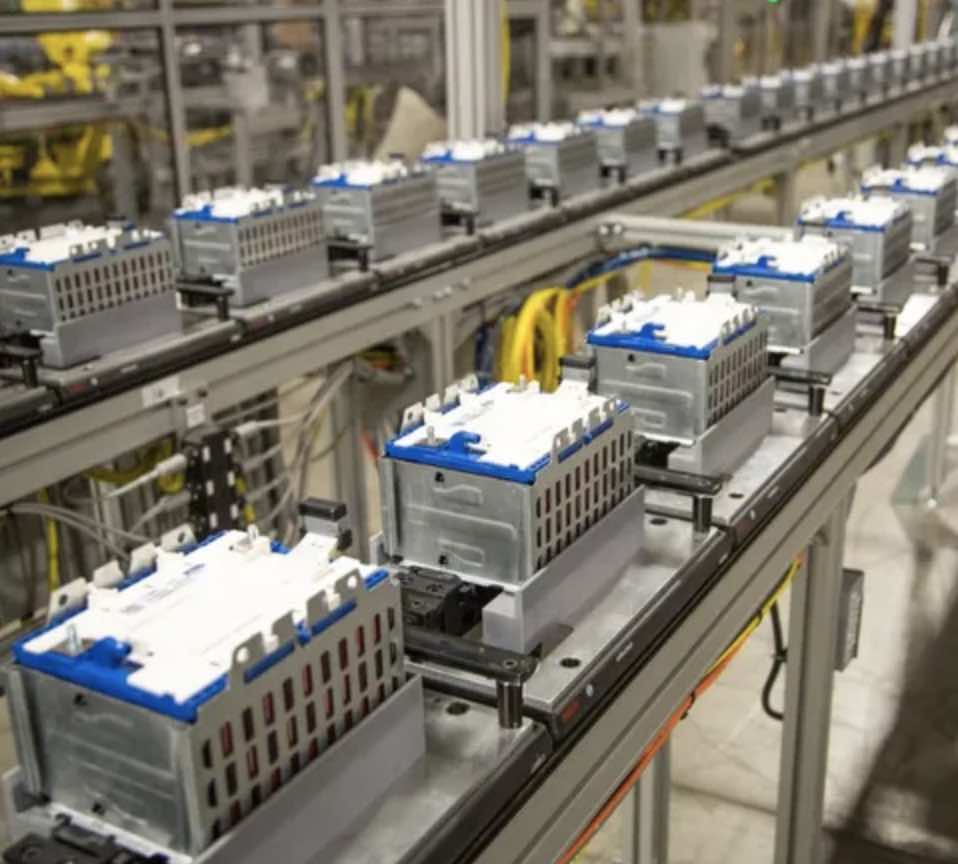
Enhancing Battery Manufacturing Facilities with Protective Coatings
The rapidly growing demand for batteries has led to the expansion of battery manufacturing facilities worldwide.
- High Performance Coatings
The rapidly growing demand for batteries, driven by electric vehicles, renewable energy storage, and portable electronics, has led to the expansion of battery manufacturing facilities worldwide. These facilities require robust protection against corrosion, chemical exposure, and electrical conductivity. In this blog post, we will explore the importance of coatings in battery manufacturing facilities and discuss the types of coatings that provide the necessary protection.
1. Acid-Resistant Coatings:
Battery manufacturing involves the use of acids and corrosive chemicals. Acid-resistant coatings provide a protective barrier against chemical attack, preventing corrosion and ensuring the longevity of equipment, storage tanks, and infrastructure. These coatings are typically formulated to withstand exposure to sulfuric acid and other battery electrolytes.
2. Electrostatic Dissipative (ESD) Coatings:
ESD coatings are designed to control static electricity, which is critical in battery manufacturing to prevent electrostatic discharge (ESD) that can damage sensitive components. These coatings dissipate static charges, reducing the risk of sparks or electrical damage. ESD coatings are commonly used on work surfaces, flooring, and equipment in battery manufacturing facilities.
3. High-Temperature Resistant Coatings:
Battery manufacturing often involves processes that generate high temperatures, such as curing, drying, or thermal treatment. High-temperature resistant coatings protect surfaces from heat-related damage, ensuring the longevity of equipment and structures subjected to elevated temperatures. These coatings can withstand thermal cycling, preventing cracking, blistering, or peeling.
4. Chemical-Resistant Coatings:
Chemical-resistant coatings are essential in battery manufacturing facilities due to the exposure to various chemicals during electrolyte preparation, coating application, and other processes. These coatings provide resistance to acids, solvents, and corrosive substances, ensuring the integrity of surfaces, storage tanks, and equipment.
5. Anti-Corrosion Coatings:
Battery manufacturing facilities often face corrosive environments due to the presence of electrolytes, moisture, and chemicals. Anti-corrosion coatings create a protective barrier that prevents the corrosion of metal surfaces, extending the lifespan of equipment, storage racks, and structural components.
6. Hygienic Coatings:
In facilities manufacturing batteries for medical devices or other applications requiring strict hygiene standards, hygienic coatings play a crucial role. These coatings provide a smooth, non-porous, and easy-to-clean surface that resists the growth of bacteria, fungi, or mold. Hygienic coatings help maintain cleanliness and sterility in the manufacturing environment.
7. UV-Resistant Coatings:
Battery manufacturing facilities may have areas exposed to ultraviolet (UV) radiation, such as outdoor storage or testing areas. UV-resistant coatings protect surfaces from UV degradation, preventing fading, discoloration, and surface deterioration caused by prolonged sun exposure.
Conclusion:
Coatings play a vital role in protecting battery manufacturing facilities, ensuring the durability, efficiency, and safety of operations. Acid-resistant coatings safeguard against chemical attack, while ESD coatings prevent electrostatic discharge. High-temperature resistant coatings offer protection in heat-intensive processes, and chemical-resistant coatings provide resistance to corrosive substances. Anti-corrosion coatings help combat moisture and chemical exposure, and hygienic coatings maintain cleanliness. UV-resistant coatings protect against UV degradation.
By selecting the appropriate coatings for battery manufacturing facilities, manufacturers can enhance the lifespan of equipment, maintain optimal operational conditions, and ensure compliance with safety and environmental regulations. Consulting with coating experts and suppliers is crucial to identify the most suitable coatings for specific applications, considering factors such as chemical exposure, temperature, and surface preparation requirements. With the right coatings in place, battery manufacturing facilities can thrive in the dynamic and evolving energy storage industry. Give us a call at High Performance Coatings and we'll help you specify the right solutions for this complicated industrial application.
Check out more resources on this topic at...
Exploring Fiberglass Mat Wall System Applications
Unveiling the Distinctions: USDA vs. FDA Coatings
Protective Linings for Wet Corn Milling Tanks: A Comprehensive Review
Effective Methods to Prevent Condensation in Food Plants
Where to use a Fiberglass Reinforced Wall System
Exploring High Performance Coatings in Aerospace Engineering
High Performance Coatings for Food Processing and Packaging Industries
Here are some projects highlighting fiberglass reinforced wall systems...
Creating Hygienic Environments: Sanitary Design for Food & Beverage Processing
Silver Spring Gardens | High Performance Coatings
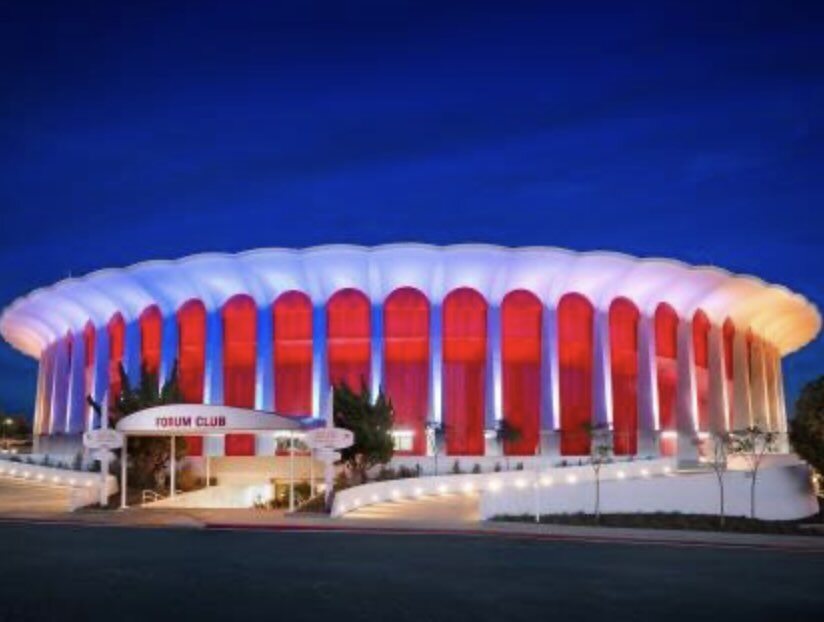
Comparing Various Topcoats: Pros and Cons and...
Explore the cutting-edge battle between...
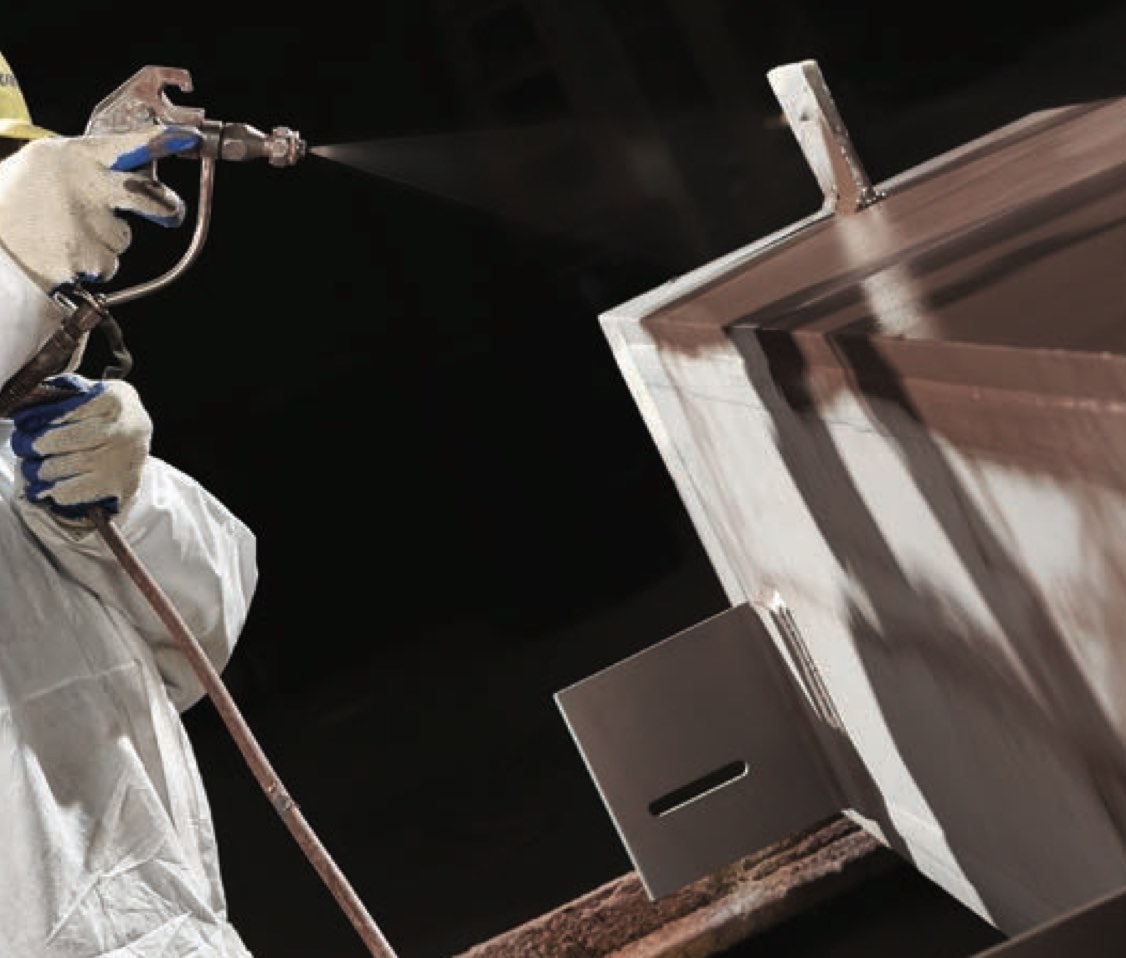
Shop Priming for High Performance Coating Systems
How often do High Performance Coatings in...
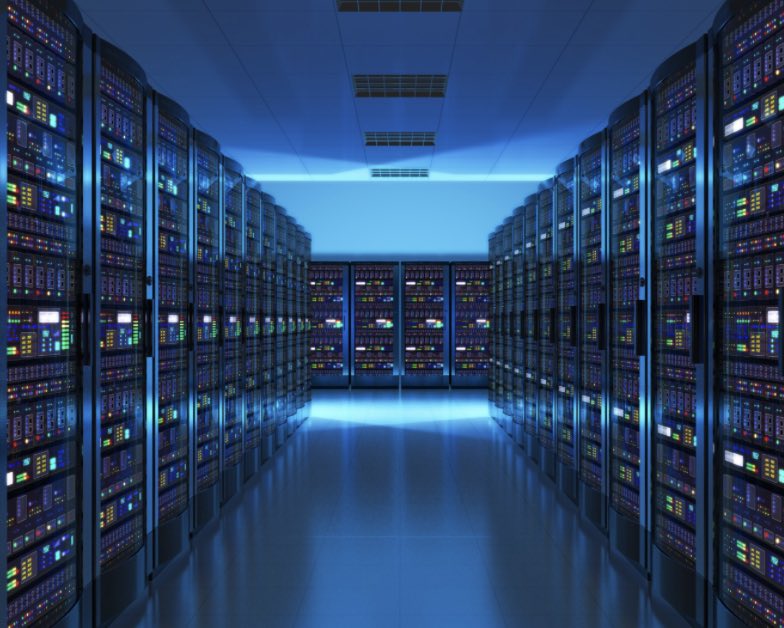
Data Center Resinous Flooring Systems
Ensuring the longevity and safety of data center...