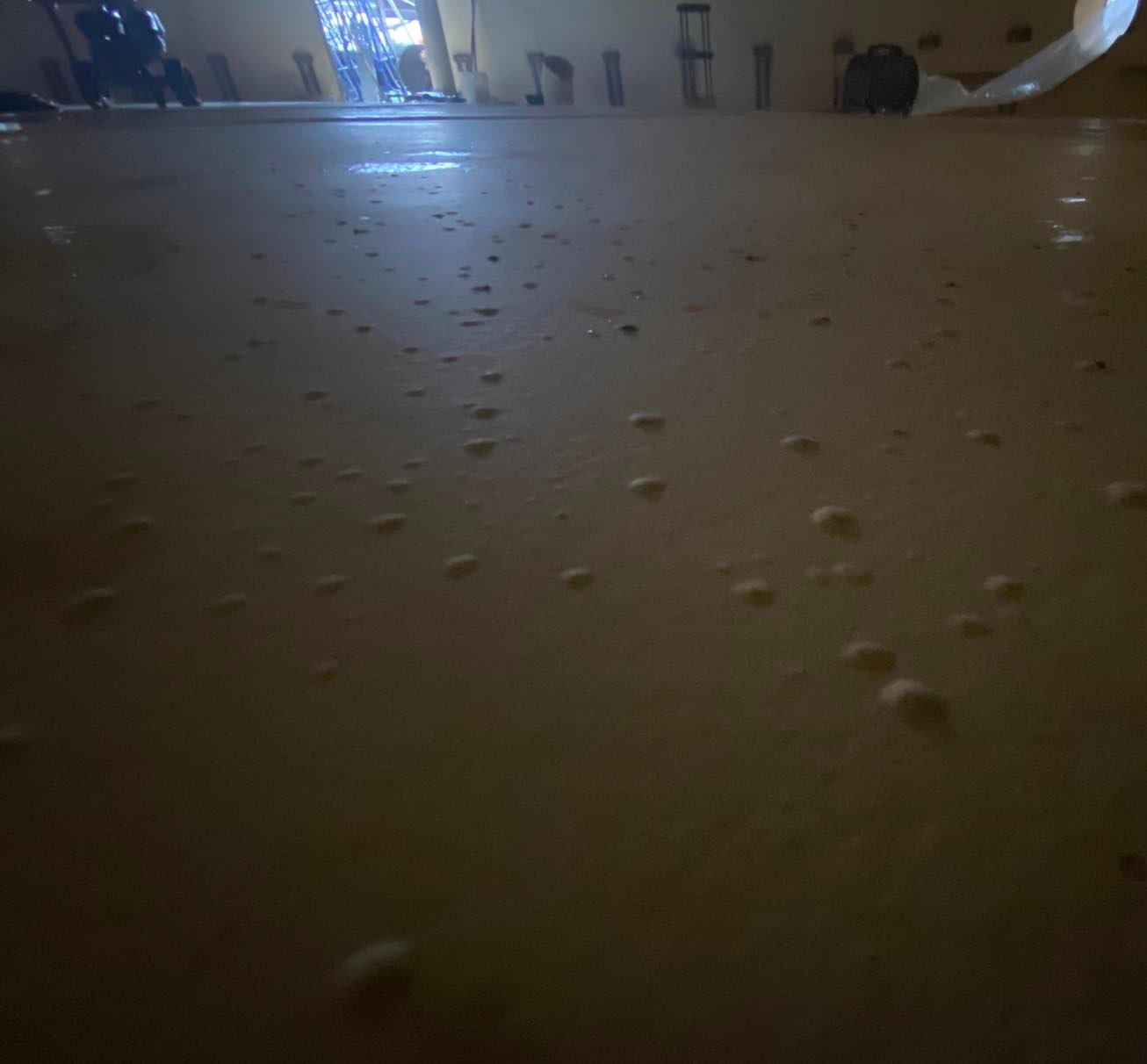
What is ASTM D 1653 (Permeability Testing) and Why is it Important?
Learn about ASTM D 1653 permeability testing, its importance in assessing coating performance, and how it helps in making informed decisions for protective coating applications.
- High Performance Coatings
What is ASTM D 1653 (permeability testing) and why is it important?
ASTM D 1653 is a widely recognized standard test method specifically designed to assess the permeability of organic coatings to both water vapor and various gases. This test is crucial for evaluating how well a coating can act as a barrier against moisture and gaseous substances, which is vital for its protective function. The procedure involves immersing coated test panels in water or other selected liquids to simulate real-world conditions. During this immersion, the test measures the rate at which water vapor or gas transmits through the coating layer. This measurement is essential for determining the coating's effectiveness in preventing the passage of these elements, which can significantly impact the durability and protective capabilities of the coating. By understanding the permeability characteristics of a coating, manufacturers and engineers can make informed decisions about its suitability for different applications, ensuring that the coating will perform as expected in various environmental conditions.
Low permeable coatings can protect steel and concrete surfaces longer
The permeability of coatings is an important property to measure because it plays a crucial role in determining the overall performance, longevity, and effectiveness of the coating in protecting the underlying material. When coatings are permeable to water, gases, or other substances, they can allow these elements to penetrate through the coating layer and reach the underlying substrate. This penetration can lead to a variety of detrimental effects, such as corrosion, which is the gradual degradation of the substrate material due to chemical reactions with moisture or other corrosive agents. Additionally, discoloration can occur, altering the appearance and aesthetic value of the coated surface. Other forms of damage may include structural weakening, loss of adhesion, and the potential for the substrate to suffer from mechanical or chemical breakdown. Therefore, understanding and controlling the permeability of coatings is essential for ensuring that they provide the intended level of protection and maintain their integrity over time, especially in environments where exposure to moisture or chemicals is prevalent.
Comparing the permeability of coatings can lead to an informed decision
Testing the permeability of coatings in immersion is particularly important because it accurately replicates the challenging conditions that the coating may encounter in real-world applications. These conditions include scenarios where the coating is submerged in water or other liquids for extended periods, such as in underwater structures, industrial tanks, or even in environments with high humidity levels. By simulating such environments, the test provides valuable insights into how the coating will perform when exposed to moisture, humidity, and various liquid substances over time. This is crucial for applications where the coating is expected to provide a protective barrier against water ingress, such as in marine environments, where saltwater can be particularly corrosive, water storage tanks that must maintain the purity and safety of their contents, or pipelines that transport liquids over long distances. In these scenarios, the coating must not only resist water penetration but also withstand the pressure and chemical composition of the liquids it encounters, ensuring the longevity and reliability of the infrastructure it protects. Understanding the permeability of coatings in these contexts helps manufacturers and engineers design and select coatings that will maintain their protective qualities and structural integrity, even under the most demanding conditions.
What is osmotic blistering?
More permeable coatings, when immersed in water or other liquids, can be highly susceptible to a phenomenon known as osmotic blistering. Osmotic blistering is a significant concern because it involves the formation of blisters or bubbles on the coating surface due to the penetration of water or other substances. This occurs when there is a pressure differential between the coating and the underlying substrate, causing water to be drawn into the coating. The presence of these blisters not only compromises the aesthetic appearance of the coating but also its structural integrity. Over time, these blisters can expand and eventually rupture, leading to the delamination of the coating. This delamination exposes the substrate to further damage, such as corrosion or chemical degradation, thereby undermining the protective function of the coating. Understanding and mitigating osmotic blistering is essential for ensuring the long-term durability and effectiveness of coatings in environments where they are regularly exposed to liquids.
Coating specifiers can benefit by using comparisons
Permeability testing can help manufacturers and users of coatings to better understand the performance of the coating in these conditions, and to make informed decisions about the suitability of the coating for a particular application. Engineers who specify coatings for potable water tanks, for example, would benefit to pay special attention to the permeability of the coatings they specify. For more information, contact a High Performance Coating Consultant here.
Check out these other resources
Three Critical Questions for Coating Selection
All Elastomeric Coatings Are Not Equal
Don't miss these project profiles

What an Engineer should know before spec'ing High...
There are many factors that should be considered...
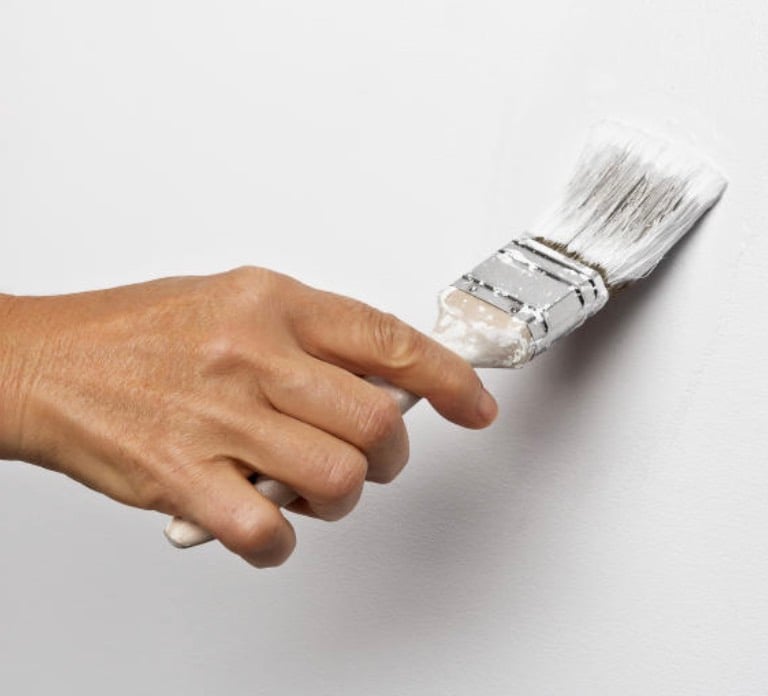
What Are The Proper Methods for Touching Up High...
Touching up high-performance coatings requires...
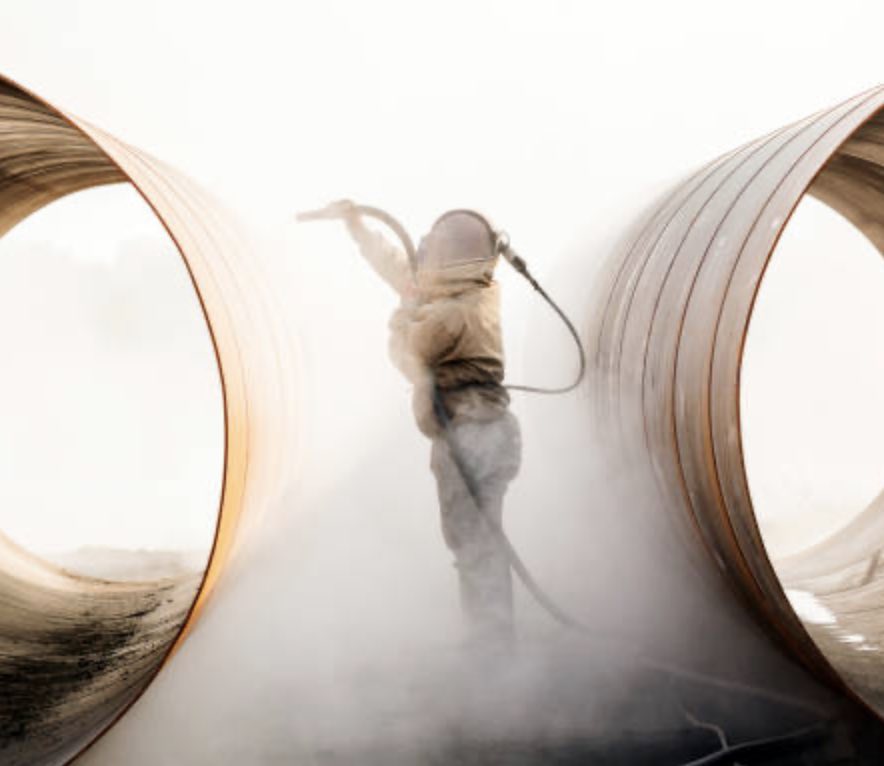
Is Surface Preparation the Most Important Part of...
Surface preparation is critical when using...