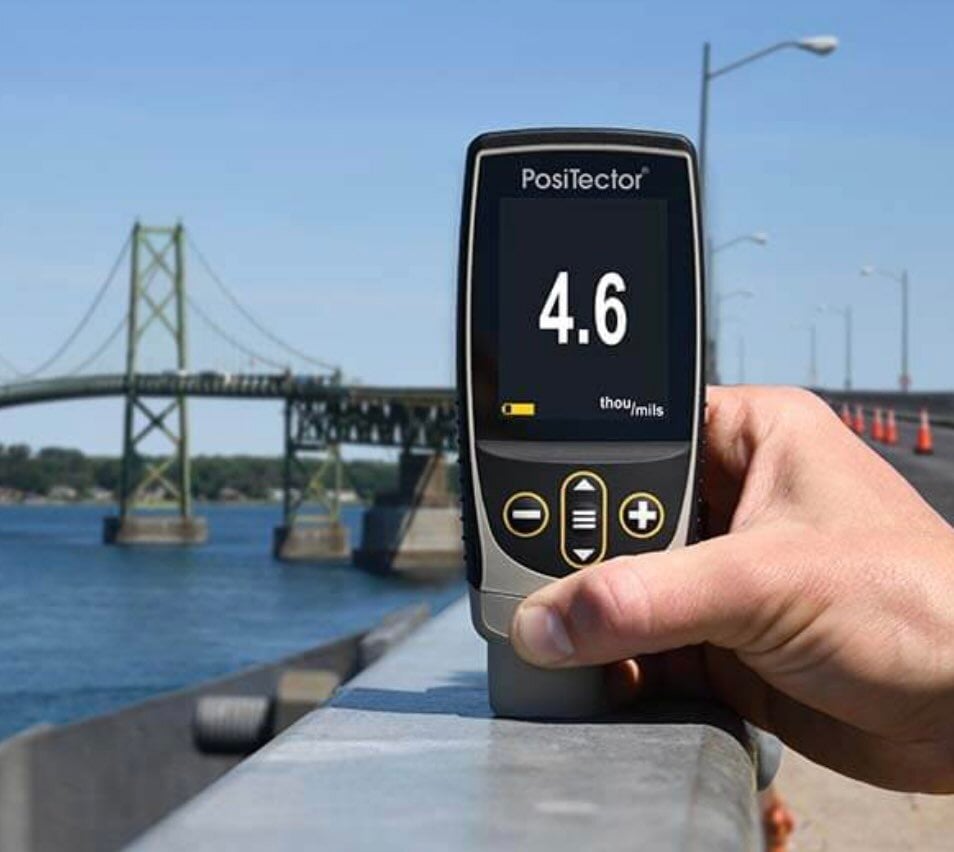
Measuring Paint Thickness: Wet Film vs. Dry Film Explained
Discover the intricacies of paint application and the crucial differences between wet and dry film thickness measurements in the painting industry.
- High Performance Coatings
Discover the intricacies of paint application and the crucial differences between wet and dry film thickness measurements in the painting industry.
Understanding Paint Thickness Measurement
Paint thickness measurement is a critical process in the coating industry to ensure the longevity and effectiveness of the paint applied to various surfaces. It involves determining the amount of paint on a substrate, which can significantly influence the coating's performance in terms of protection, appearance, and durability. Accurate measurement is crucial in meeting industry standards, avoiding material waste, and ensuring compliance with project specifications.
The significance of paint thickness measurement lies in its ability to prevent coating failures such as blistering, flaking, or corrosion. By understanding the exact thickness of the paint, technicians can make informed decisions about the application process and the expected lifespan of the coating.
Exploring Wet Film Thickness (WFT): Techniques and Tools
Wet Film Thickness (WFT) refers to the depth of a coating measured immediately after application, before drying or curing. Measuring WFT is important to predict the final Dry Film Thickness (DFT) and to ensure that the paint is applied according to the manufacturer's recommendations. Techniques for measuring WFT include the use of notched gauges, which are dragged across the wet coat to leave a track that can be measured for thickness.
Other tools include comb gauges, which feature a series of notches at various depths, and wet film wheels, which roll across the surface. High-tech options like ultrasonic gauges use sound waves to determine thickness. Each technique has its own advantages and is selected based on factors such as accuracy requirements, paint type, and environmental conditions.
Delving into Dry Film Thickness (DFT): Methods and Importance
Dry Film Thickness (DFT) measures the thickness of a coating after it has fully dried or cured. This is a crucial step for quality control in the coating process, as it reflects the actual protective layer that remains on the surface. Common methods for measuring DFT include magnetic pull-off gauges, electronic magnetic gauges, and eddy current gauges, each suitable for different types of substrates and coatings.
The importance of DFT measurement cannot be overstated, as it directly relates to the coating's performance characteristics. By ensuring that the DFT meets specified ranges, technicians can guarantee that the coating will provide adequate protection against environmental factors, wear, and corrosion, ultimately extending the service life of the coated asset.
Comparative Analysis: Wet Film vs. Dry Film Measurement
While both WFT and DFT measurements are vital for the coating process, they serve different purposes and are used at distinct stages of the application. WFT is measured immediately after the paint is applied, providing an estimate for the final DFT and allowing for corrections in real-time if the application is too thick or thin. On the other hand, DFT is measured after the coating has dried, verifying that the final thickness complies with the project's specifications.
A comparative analysis between WFT and DFT measurement is essential for understanding the relationship between the two. Factors such as the type of paint, environmental conditions, and drying times can affect the correlation between WFT and DFT. By analyzing both measurements, professionals can ensure a successful coating application with optimal protection and efficiency.
The Role of SSPC-PA2 in Paint Thickness Verification
SSPC-PA2 is a standard established by the Society for Protective Coatings that provides guidelines for measuring the dry film thickness of protective coatings. The standard ensures that DFT measurements are conducted systematically and that a sufficient number of readings are taken to represent the coated area accurately.
The importance of SSPC-PA2 lies in its widespread recognition and adoption in the coatings industry, providing a benchmark for quality assurance. It outlines procedures for gauge calibration, verification, and adjustment, as well as the proper documentation of measurement results. Adherence to SSPC-PA2 helps maintain consistency and reliability in paint thickness verification, which is crucial for the longevity and performance of protective coatings.
Check out these other related blogs:
Why High Performance Coatings Fail
What Are Proper Methods For Repairing High Performance Coatings
The Importance of Surface Preparation
What Maintenance is Required with High Performance Coatings?
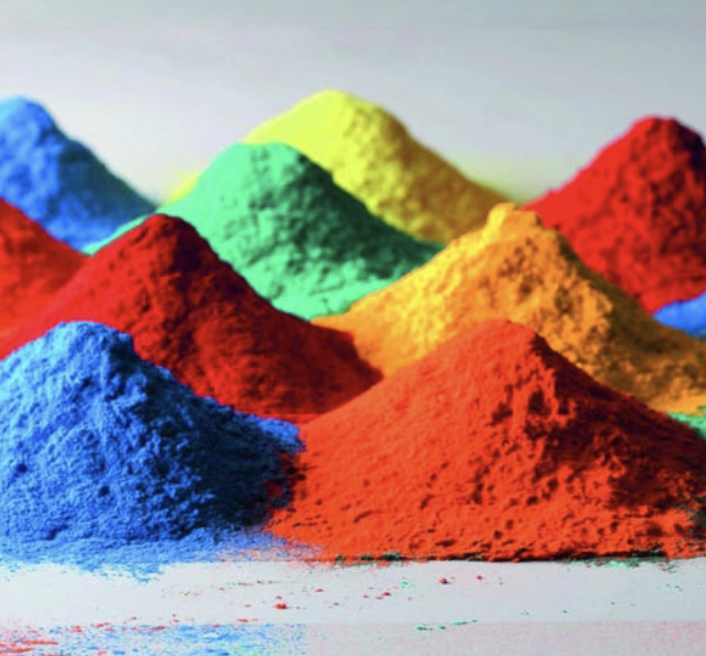
Unleashing Color Brilliance: Blending Pigment for...
Discover how blending pigments can transform the...
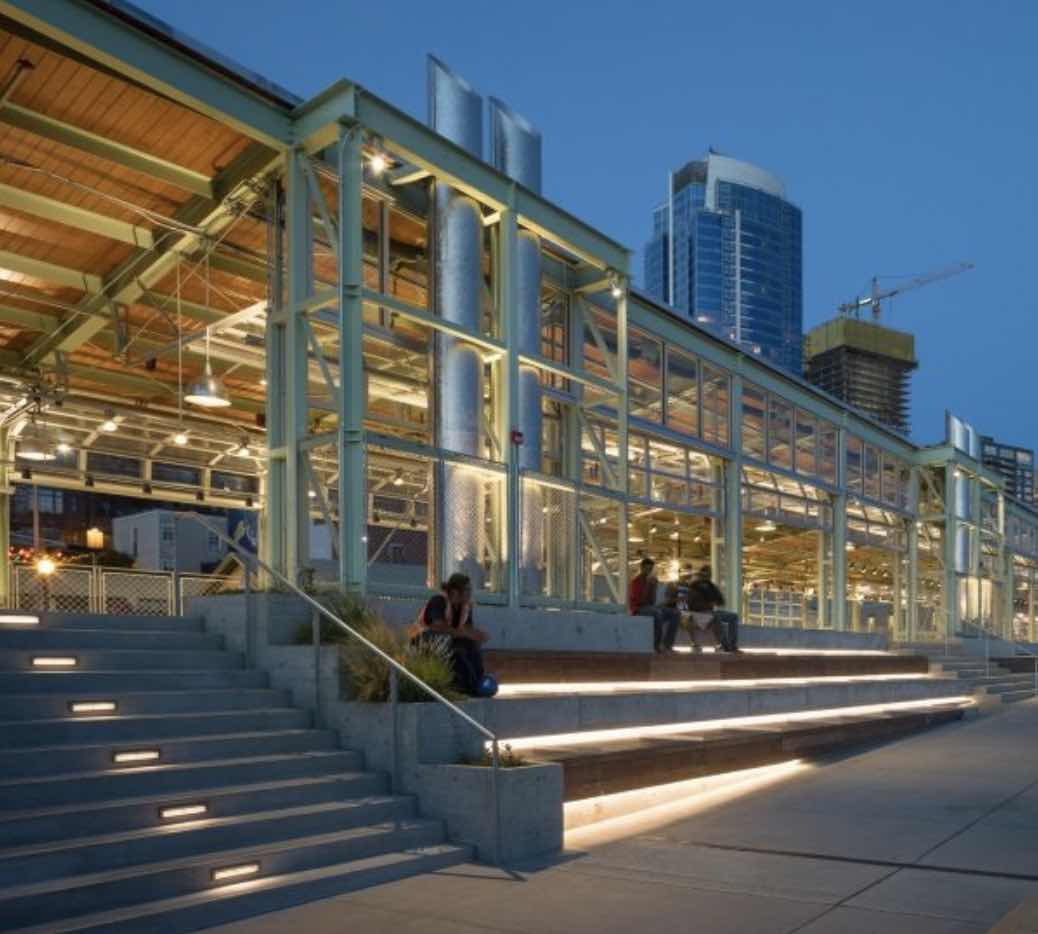
How Do High Performance Coatings Differ From...
High-performance coatings differ from regular...
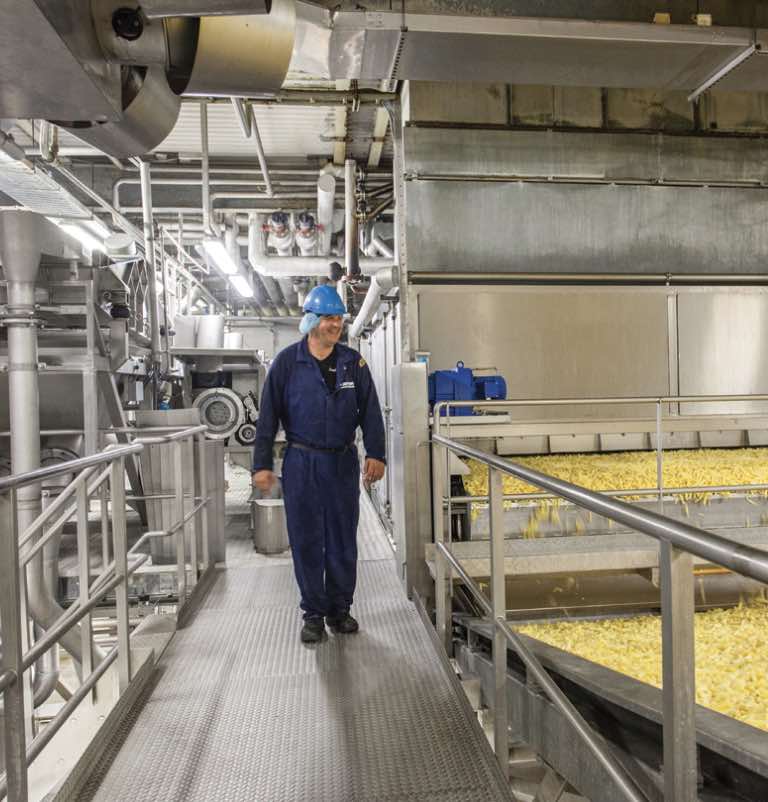
Unveiling the Distinctions: USDA vs. FDA Coatings
Explore the critical differences between USDA and...