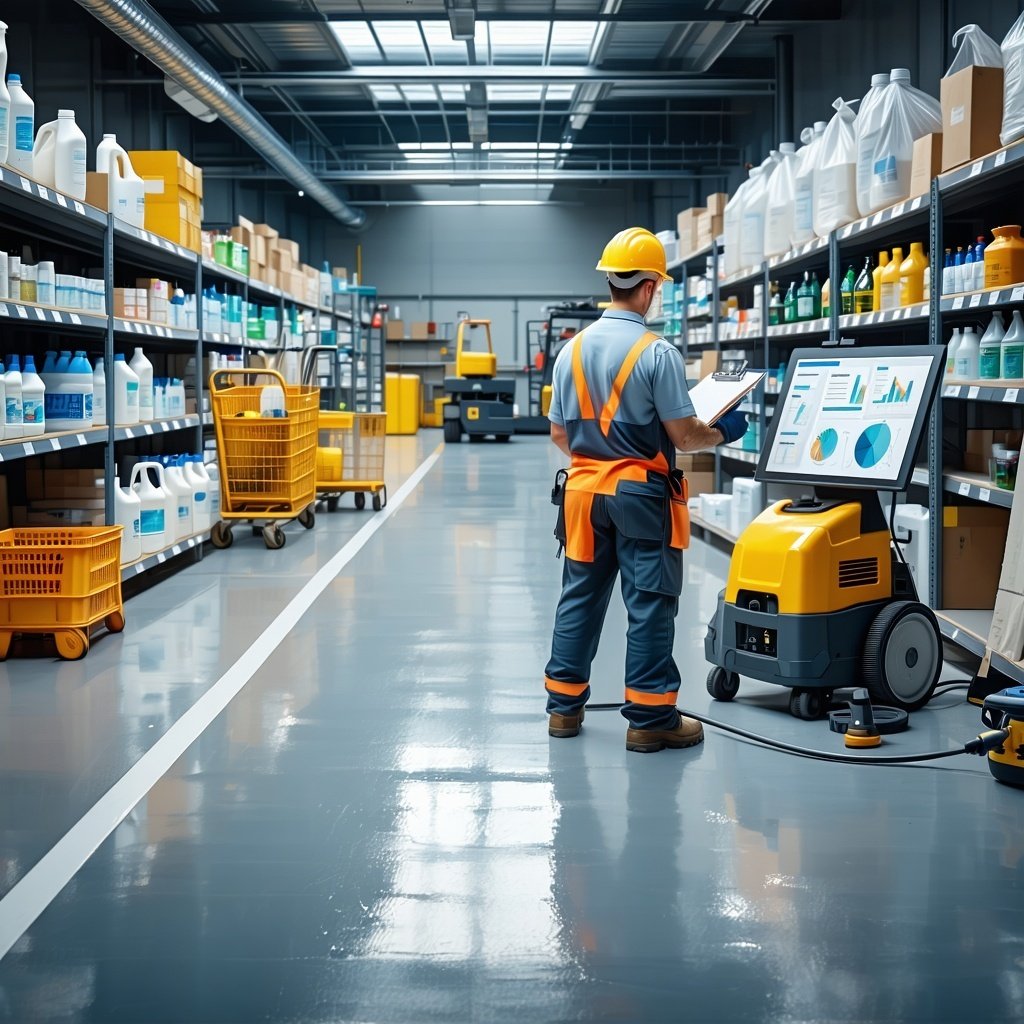
What Maintenance is Required with High Performance Coatings?
Maintenance requirements for high-performance coatings can vary depending on the specific type of coating and the environment in which it is applied.
- High Performance Coatings
Maintenance over time can greatly reduce the ownership cost of any coated asset.
What Maintenance is Required with High Performance Coatings?
High-performance coatings represent a significant investment in protecting and enhancing your surfaces, often costing 3-5 times more than standard coating systems. However, this premium investment can deliver 15-20+ years of superior protection when properly maintained, compared to just 5-10 years for conventional coatings. Like any valuable asset, these specialized coatings require proper care to deliver their full potential and maximize return on investment.
The maintenance approach varies dramatically based on coating type, environmental conditions, and application requirements. Industrial epoxy floor coatings in manufacturing facilities face different challenges than architectural polyurethane systems on building exteriors. Understanding these distinctions and following proven maintenance practices ensures your coating investment continues delivering value throughout its intended service life.
The Foundation: Regular Cleaning and Inspection
Consistent cleaning forms the cornerstone of coating maintenance, directly impacting both performance and longevity. Dirt, debris, and contaminants don't just affect appearance—they can compromise the coating's protective properties over time. Accumulated contaminants (algae, mildew, mold, etc.) can trap moisture against the coated surface, leading to osmotic blistering or peeling of the finish coat in some systems. Chemical contaminants may react with certain coating chemistries, causing premature degradation or discoloration.
Cleaning Frequency and Methods
Daily Operations: High-traffic areas like manufacturing floors or commercial kitchens may require daily cleaning to prevent buildup of oils, chemicals, or food particles. Simple sweeping or dry mopping removes loose debris that could become ground into the coating surface.
Weekly Deep Cleaning: Many high-performance coatings benefit from weekly deep cleaning using appropriate detergents. pH-neutral cleaners work best for most systems, though some specialized formulations may require specific cleaning agents recommended by the manufacturer. Avoid harsh alkaline cleaners (pH > 10) or strong acids (pH < 3) unless specifically approved, as these can etch or chemically attack certain coating types.
Annual Intensive Cleaning: Stubborn stains or heavy contamination may require monthly intensive cleaning with specialized products. This might include degreasing agents for industrial floors or mildewcides for exterior coatings in humid climates.
Inspection Protocols
Regular inspections catch problems before they become costly repairs, potentially saving 70-80% of remediation costs. Professional coating inspectors recommend systematic visual assessments following a structured checklist approach.
Visual Inspection Checklist:
- Surface Integrity: Look for cracks, chips, or impact damage that could allow moisture penetration
- Adhesion Issues: Check for peeling, bubbling, or delamination at edges and high-stress areas
- Color Changes: Document any fading, chalking, or discoloration that might indicate UV degradation or chemical attack
- Wear Patterns: Identify areas of excessive wear that may require earlier recoating
- Contamination: Note any staining, efflorescence, or biological growth
Documentation Best Practices: Photograph problem areas consistently from the same angles and distances to track progression over time. GPS coordinates or detailed location descriptions help maintenance teams locate specific issues quickly.
Proactive Repair Strategies
When localized damage occurs, swift action preserves the coating's overall integrity and prevents minor issues from becoming major failures. The "1-10-100 Rule" applies perfectly to coating maintenance: fixing a problem immediately costs $1, waiting until it spreads costs $10, and delaying until system failure costs $100.
Damage Assessment and Prioritization
Critical Repairs (Address within 24-48 hours):
- Through-coating damage exposing substrate
- Active moisture intrusion or osmotic blistering
- Chemical spill damage or severe staining
- Delamination larger than 1 square inch
Priority Repairs (Address within 2-4 weeks):
- Surface scratches or scuff marks
- Minor edge lifting or small chips
- Localized wear patterns
- Color variations affecting appearance
Routine Maintenance (Schedule during next maintenance window):
- Minor surface contamination
- Slight gloss reduction
- Small areas of chalking
Repair Methodology
Surface Preparation: The foundation of any successful repair begins with proper surface preparation. Remove all loose or damaged coating material using appropriate mechanical methods—grinding, sanding, or blasting depending on the coating type and damage extent. Clean the repair area thoroughly to remove all dust, oils, or contaminants that could interfere with adhesion.
Material Selection: Use coating materials specifically designed for repairs and compatible with the existing system. Mixing different coating chemistries can result in adhesion failures or incompatible expansion/contraction rates leading to cracking.
Application Technique: Follow manufacturer specifications for mixing ratios, application thickness, and environmental conditions. Professional repair techniques often involve feathering edges to create seamless transitions and using compatible primers when required.
Curing and Quality Control: Allow proper curing time before returning surfaces to service. Most high-performance coatings require 24-72 hours for initial cure and 7-14 days for full chemical cure, depending on temperature and humidity conditions.
Understanding Recoating Cycles
Even the highest-performance coatings have finite lifespans, typically ranging from 5-20 years depending on formulation and environmental exposure. Understanding and planning for recoating cycles ensures continuous protection and avoids the significantly higher costs associated with coating system failure and substrate damage.
Factors Affecting Coating Lifespan
Environmental Exposure: UV radiation, temperature cycling, humidity, and chemical exposure all accelerate coating degradation. Coatings in Florida's intense UV environment may require recoating every 10-15 years, while the same system in a moderate climate might last 20+ years.
Traffic and Mechanical Wear: High-traffic areas experience accelerated wear. Industrial floors handling heavy machinery or frequent forklift traffic may need recoating every 3-5 years, while low-traffic areas could last 10-15+ years.
Chemical Exposure: Facilities handling acids, bases, solvents, or other aggressive chemicals need more frequent recoating. Chemical processing plants might recoat every 2-3 years, while office environments could extend to 10-15 years.
Substrate Movement: Buildings that experience significant thermal expansion, settling, or structural movement stress coating systems, potentially reducing lifespan by 20-30%.
Recoating vs. Complete Removal
Recoating Over Existing Systems: When the existing coating shows wear but maintains good adhesion, recoating can extend life cost-effectively. This approach typically costs 40-60% less than complete removal and reapplication.
Complete Removal and Replacement: Severely degraded coatings, those with poor adhesion, or incompatible systems require complete removal. While more expensive initially, this approach often provides better long-term value.
Surface preparation becomes critical during recoating projects, often representing 60-70% of the total project cost. This process may involve thorough cleaning, mechanical abrasion, or complete removal of compromised coating layers. Power washing, chemical stripping, or mechanical abrasion each serve different purposes depending on the coating type and condition.
Environmental Considerations and Protection Strategies
Your coating's environment significantly impacts maintenance requirements and can reduce coating lifespan by 50% or more in severe conditions. Developing environmental protection strategies extends coating life and reduces total cost of ownership.
Climate-Specific Challenges
UV Radiation: Ultraviolet radiation breaks down polymer chains in coating systems, causing chalking, fading, and eventual failure. Coatings in high-UV environments benefit from UV-stable topcoats or periodic application of UV-protective treatments.
Temperature Extremes: Thermal cycling stresses coating systems through expansion and contraction. Facilities experiencing wide temperature swings (>50°F daily variation) may need flexible coating systems or stress-relief joints.
Humidity and Moisture: High humidity environments accelerate coating degradation and promote biological growth. Proper ventilation, dehumidification, and antimicrobial additives help combat these effects.
Chemical Exposure: Industrial environments with acid fumes, alkaline solutions, or organic solvents require specialized resistant coatings and more frequent maintenance.
Protective Measures
Sacrificial Topcoats: Apply renewable topcoats that can be periodically stripped and reapplied without affecting the underlying coating system. This approach works particularly well for high-wear areas.
Environmental Controls: Implementing humidity control, UV filtering, or chemical containment systems protects coating investments. While requiring initial investment, these measures often pay for themselves through extended coating life.
Drainage and Ventilation: Proper drainage prevents standing water that can cause osmotic blistering. Adequate ventilation reduces humidity and chemical vapor exposure.
Documentation: Your Maintenance Roadmap
Maintaining detailed records transforms reactive maintenance into strategic asset management. Comprehensive documentation enables data-driven decisions about maintenance timing, budgeting, and system optimization.
Record-Keeping Essentials
Installation Documentation: Maintain complete records of initial coating application including material specifications, environmental conditions, surface preparation methods, and application parameters. This baseline information proves invaluable for future maintenance decisions.
Maintenance Logs: Document all cleaning activities, inspection findings, and repair work with dates, materials used, and personnel involved. Digital systems with photo documentation provide the most comprehensive records.
Performance Tracking: Monitor coating performance metrics such as gloss retention, color stability, and wear patterns. This data helps predict maintenance needs and optimize recoating schedules.
Cost Analysis: Track maintenance costs over time to identify trends and cost-effective strategies. This information supports budget planning and helps justify maintenance investments to management.
Digital Maintenance Systems
Mobile Inspection Apps: Tablet-based inspection systems allow real-time data collection, photo documentation, and GPS location tracking. These systems improve inspection consistency and data quality.
Predictive Analytics: Advanced maintenance systems use historical data to predict coating failures and optimize maintenance schedules, potentially reducing maintenance costs by 15-25%.
Integration with Facility Management: Linking coating maintenance data with broader facility management systems provides holistic asset management and improves resource allocation.
Leveraging Manufacturer Expertise and Support
Coating manufacturers provide the most authoritative guidance for their specific products, backed by extensive laboratory testing and decades of field experience. These relationships extend far beyond initial product selection to encompass lifetime technical support and maintenance optimization.
Manufacturer Support Services
Field Technical Services: Manufacturers often provide on-site technical support for complex maintenance projects or problem resolution. This service proves particularly valuable for critical applications or when coating failures occur.
Training Programs: Comprehensive training programs for maintenance personnel ensure proper techniques and safety protocols. Well-trained maintenance teams can extend coating life by 20-30% through proper care and timely intervention.
Product Evolution: Manufacturers continuously improve their products based on field experience. Staying connected with manufacturer updates ensures access to improved formulations and maintenance techniques.
Specialized Maintenance Products
Companies like Tnemec publish comprehensive maintenance guidelines for their product lines, including specialized floor coating systems, marine coatings, and industrial protective systems. These resources provide specific care instructions, compatible cleaning products, and troubleshooting guides tailored to each coating system.
Maintenance Kits: Many manufacturers offer maintenance kits containing compatible cleaning products, touch-up materials, and detailed instructions. These kits ensure proper materials are used and simplify maintenance procurement.
Warranty Considerations: Following manufacturer maintenance guidelines often extends warranty coverage and ensures warranty claims are honored. Deviation from recommended practices can void warranties and result in denied claims.
Economic Analysis: The True Cost of Coating Maintenance
Understanding the economics of coating maintenance helps justify proper care and demonstrates the value of proactive maintenance strategies. Well-maintained coatings deliver superior total cost of ownership compared to neglected systems.
Cost Comparison Analysis
Preventive Maintenance Costs: Regular cleaning, inspection, and minor repairs typically cost $0.50-$2.00 per square foot per year, depending on coating type and environmental conditions.
Reactive Maintenance Costs: Addressing coating failures after they occur costs $5-$15 per square foot, including emergency repairs, production downtime, and potential substrate damage.
Replacement Costs: Complete coating system replacement ranges from $3-$12 per square foot for standard systems to $15-$30 per square foot for specialized high-performance systems.
Hidden Costs: Coating failures often result in hidden costs including production downtime, product contamination, safety incidents, and regulatory compliance issues. These costs can exceed the direct coating replacement costs.
Advanced Maintenance Technologies
Emerging technologies are revolutionizing coating maintenance, offering new tools for assessment, repair, and life extension. These innovations provide more precise maintenance approaches and improved cost-effectiveness.
Non-Destructive Testing
Infrared Thermography: Thermal imaging identifies coating defects, moisture intrusion, and delamination before visible signs appear. This technology enables truly predictive maintenance.
Ultrasonic Testing: High-frequency sound waves detect coating thickness, delamination, and hidden defects without damaging the coating surface.
Impedance Spectroscopy: Advanced electrical testing methods assess coating integrity and predict remaining service life with high accuracy.
The Bottom Line: Strategic Maintenance Investment
Strategic maintenance transforms high-performance coatings from a one-time expense into a long-term asset that delivers sustained value. The data clearly demonstrates that proactive maintenance programs cost 40-60% less than reactive approaches while delivering superior performance and longer coating life.
Return on Investment: Proper maintenance typically delivers 300-500% return on investment through extended coating life, reduced replacement costs, and improved facility operations. This ROI calculation doesn't include the value of avoiding production downtime, safety incidents, or regulatory compliance issues.
Competitive Advantage: Well-maintained facilities project professionalism, ensure regulatory compliance, and provide safer working environments. These factors contribute to employee satisfaction, customer confidence, and operational efficiency.
Risk Mitigation: Proactive maintenance reduces the risk of unexpected coating failures, emergency repairs, and associated business disruptions. This predictability enables better planning and resource allocation.
Ready to optimize your coating maintenance strategy? The complexity of modern coating systems and the significant investments they represent make professional guidance essential. Contact a High Performance Coating Consultant to discuss your specific requirements and develop a customized maintenance plan that protects your investment while optimizing total cost of ownership.
Our certified coating consultants can perform comprehensive facility assessments, develop customized maintenance protocols, and provide ongoing technical support to ensure your coating systems deliver maximum value throughout their service life.
LET OUR KNOWLEDGE AND EXPERTISE HELP ENSURE YOUR NEXT PROJECT IS SUCCESSFUL
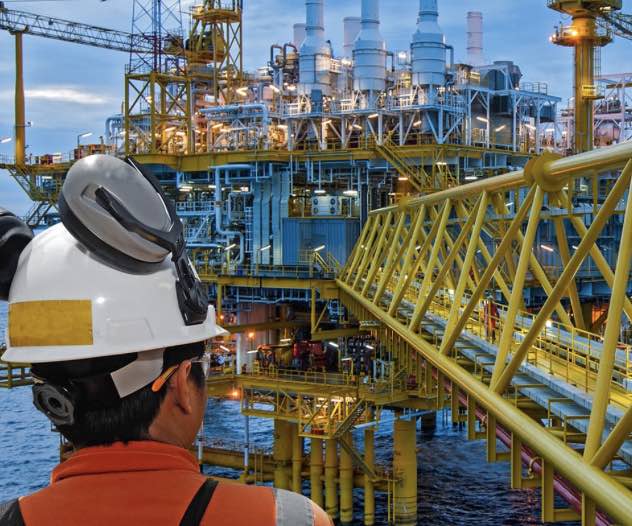
Exploring High Performance Coatings for Offshore...
Offshore and marine structures face relentless...

Safeguarding The Critical Infrastructure Of Oil...
Oil and gas pipelines and refineries form the...

What Is The Role of High Performance Coatings in...
Restoration projects play a vital role in...