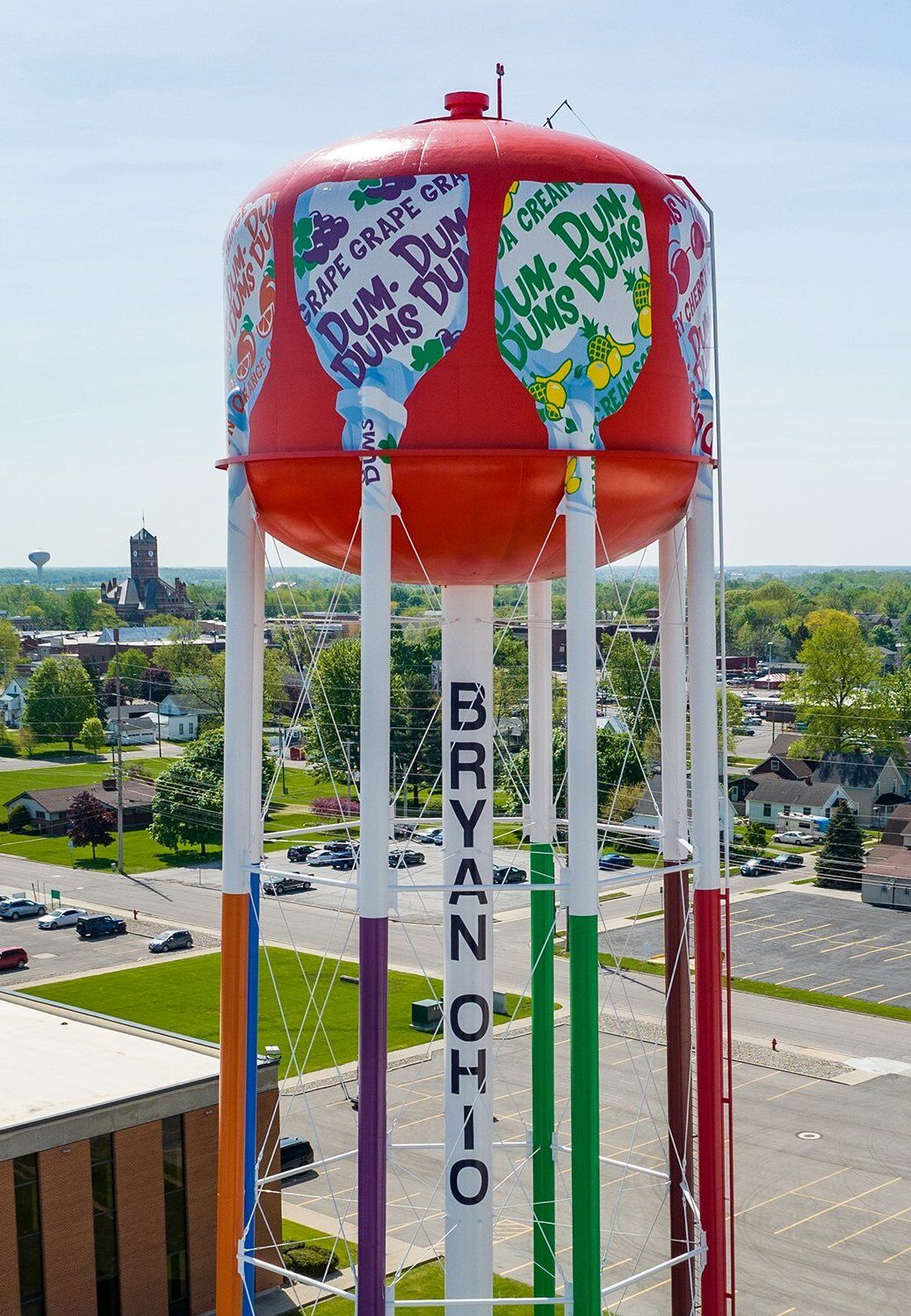
The Pros and Cons of Various Water Tank Coating Types
Discover the pros and cons of acrylic, polyurethane, fluoropolymer and epoxy coatings for water tanks to ensure durability and cost-effectiveness.
- Rick Gilbreath
THE PROS AND CONS OF VARIOUS WATER TANK COATING TYPES:
Choosing the right water tank coating is crucial for durability and cost-effectiveness. Here’s a comprehensive comparison to guide your decision.
Understanding Water Tank Coatings: The Basics
Water tank coatings play a critical role in safeguarding the tank from a variety of environmental factors, such as extreme weather conditions, moisture, and temperature fluctuations, which can all contribute to the deterioration of the tank's structure over time. Additionally, these coatings are vital in preventing corrosion, a common issue that can lead to leaks and structural failures, as well as contamination, which can compromise the quality and safety of the water stored within the tank. To achieve these protective benefits, coatings are applied to both the exterior and interior surfaces of the tanks. This dual application not only extends the lifespan of the tanks by providing a robust barrier against potential damage but also ensures that the water remains safe and uncontaminated for consumption or use.
Selecting the appropriate coating involves a careful evaluation of several factors. The material of the tank, whether it is made of steel, concrete, or another substance, can significantly influence the type of coating that will adhere best and provide optimal protection. The tank's location is another crucial consideration, as tanks situated in coastal areas, for example, may require coatings with enhanced resistance to saltwater corrosion. The type of water stored, whether it is potable, wastewater, or industrial water, also dictates the necessary chemical resistance and safety standards of the coating. Lastly, budget constraints can impact the choice, as some coatings may offer superior protection but at a higher cost. By gaining a comprehensive understanding of the basic types of coatings available, along with their respective advantages and disadvantages, individuals can make a well-informed decision that aligns with their specific needs and ensures the long-term durability and safety of their water tanks.
Exterior Coatings: Acyrlic vs. Polyurethane vs. Fluoropolymer
Acrylic coatings, like Tnemec Series 1029 Enduratone, are water-based and eco-friendly, making them an excellent choice for projects that prioritize environmental sustainability. These coatings are formulated to minimize the release of volatile organic compounds (VOCs), which can be harmful to both the environment and human health. This eco-friendly nature makes acrylics particularly appealing for use in areas with strict environmental regulations or for projects aiming to achieve green certification. Additionally, acrylic coatings are relatively easy to apply, requiring minimal specialized equipment or training, which can reduce labor costs and application time. They dry quickly, allowing for faster project completion and less downtime, which is beneficial in time-sensitive situations. However, despite these advantages, acrylics may not offer the same level of durability and resistance to harsh environmental conditions, such as extreme temperatures, UV exposure, or chemical contact, as polyurethanes. This limitation can result in a shorter lifespan for the coating, necessitating more frequent reapplications and potentially increasing long-term maintenance costs.
Polyurethanes, like Tnemec Series 1095 Endura-Shield, are renowned for their exceptional durability and flexibility, making them a versatile choice for a wide range of applications. These coatings form a robust protective layer that is capable of withstanding harsh weather conditions, such as heavy rain, snow, and intense sunlight, which can otherwise cause significant wear and tear on exposed surfaces. Additionally, polyurethanes are highly resistant to abrasion, meaning they can endure physical impacts and friction without easily wearing down. This makes them particularly suitable for environments where surfaces are subject to frequent contact or movement. Another advantage of polyurethanes is their relative cost-effectiveness. They offer a balance between performance and affordability, which makes them a popular choice for many projects, especially those with budget constraints. However, it is important to note that the life cycle of polyurethane coatings can be shorter compared to fluoropolymers, particularly in extremely harsh environments .
Fluoropolymers, like Tnemec Series 701 Hydroflon, on the other hand, are distinguished by their superior longevity and remarkable resistance to a variety of environmental stressors. These coatings excel in protecting surfaces from UV radiation, which can cause fading and degradation over time, as well as from harsh chemicals and high temperatures that might otherwise compromise the integrity of the coating. While fluoropolymers tend to be more expensive than polyurethanes, their extended life cycle often justifies the higher initial cost. This is because they require less frequent reapplication and maintenance and stay cleaner longer, ultimately leading to cost savings over the long term. Fluoropolymers are an excellent choice for projects where long-term durability and minimal maintenance are priorities, such as in industrial settings or in locations with extreme environmental conditions. Their ability to maintain their protective properties over extended periods makes them a reliable option for ensuring the longevity and safety of the surfaces they cover.
Interior Coatings: Epoxies vs. Hybrid Urethanes
Epoxy coatings, like Tnemec Series 21 or Series 22, are widely used for interior water tank applications due to their excellent adhesion, chemical resistance, and durability. These coatings are formulated to create a hard, protective layer that adheres strongly to the tank's surface, effectively preventing corrosion and contamination by forming a barrier against water and other potentially harmful substances. This makes them particularly suitable for environments where the water quality must be maintained at a high standard, such as in potable water tanks. However, despite their many advantages, epoxies can be brittle and may not perform well under conditions of thermal or mechanical stress. This brittleness can lead to cracking or delamination when the tank is subjected to significant temperature fluctuations or physical impacts, potentially compromising the protective barrier and necessitating repairs or reapplications.
Hybrid urethanes provide flexibility, durability, and resistance to chemicals. These coatings are designed to endure a broader range of conditions, reducing the likelihood of cracking or peeling under stress. However, they tend to be more costly than traditional epoxy coatings, which can be a financial burden, particularly for large-scale projects. Furthermore, their effectiveness can fluctuate with environmental conditions, and they often require specific application methods and a plural component application to ensure proper adhesion and performance. If not applied correctly, they will not offer the same level of performance as other coatings, potentially affecting water quality.
Making the Right Choice for Your Water Tank
Choosing the right coating for your water tank is a multifaceted decision that requires careful consideration of various factors to ensure optimal performance and protection. First and foremost, you must evaluate the specific requirements of your project, which may include the type of water being stored, the material of the tank, and the intended use of the water. For instance, potable water tanks may necessitate coatings that meet stringent health and safety standards, while tanks used for industrial purposes might require coatings with enhanced chemical resistance.
Environmental conditions play a significant role in determining the appropriate coating. Factors such as temperature fluctuations, humidity levels, and exposure to UV radiation or saltwater can all impact the performance and longevity of a coating. Tanks located in coastal areas, for example, may benefit from coatings with superior resistance to saltwater corrosion, while those in regions with extreme temperatures might require coatings that can withstand thermal stress.
Budget is another critical consideration, as it can influence the choice of coating based on initial costs and long-term financial implications. While some coatings may be more expensive upfront, their durability and reduced maintenance needs can lead to cost savings over time. Conversely, more affordable coatings might require frequent reapplications, potentially increasing long-term expenses.
Long-term maintenance needs should also be factored into the decision-making process. Coatings that offer extended lifespans and require minimal upkeep can reduce downtime and maintenance costs, ensuring that the tank remains in optimal condition for years to come.
Understanding the pros and cons of each coating type is essential for making an informed decision that ensures the durability and safety of your water tank. Each coating has its unique advantages and limitations, and selecting the right one involves balancing these factors to meet your specific needs.
Our expertise in water tank coatings can provide valuable insights and guidance. We can help conduct a thorough assessment of your tank's needs, taking into account all relevant factors, and recommend the most suitable coating options. Whether you prioritize cost, longevity, environmental impact, or a combination of these factors, there is a coating option available that can meet your requirements and provide optimal protection for your water tank. By trusting us to carefully evaluate all these aspects, you can ensure that your water tank will remain durable, safe, and efficient in its operation. Contact us here for a free evaluation.
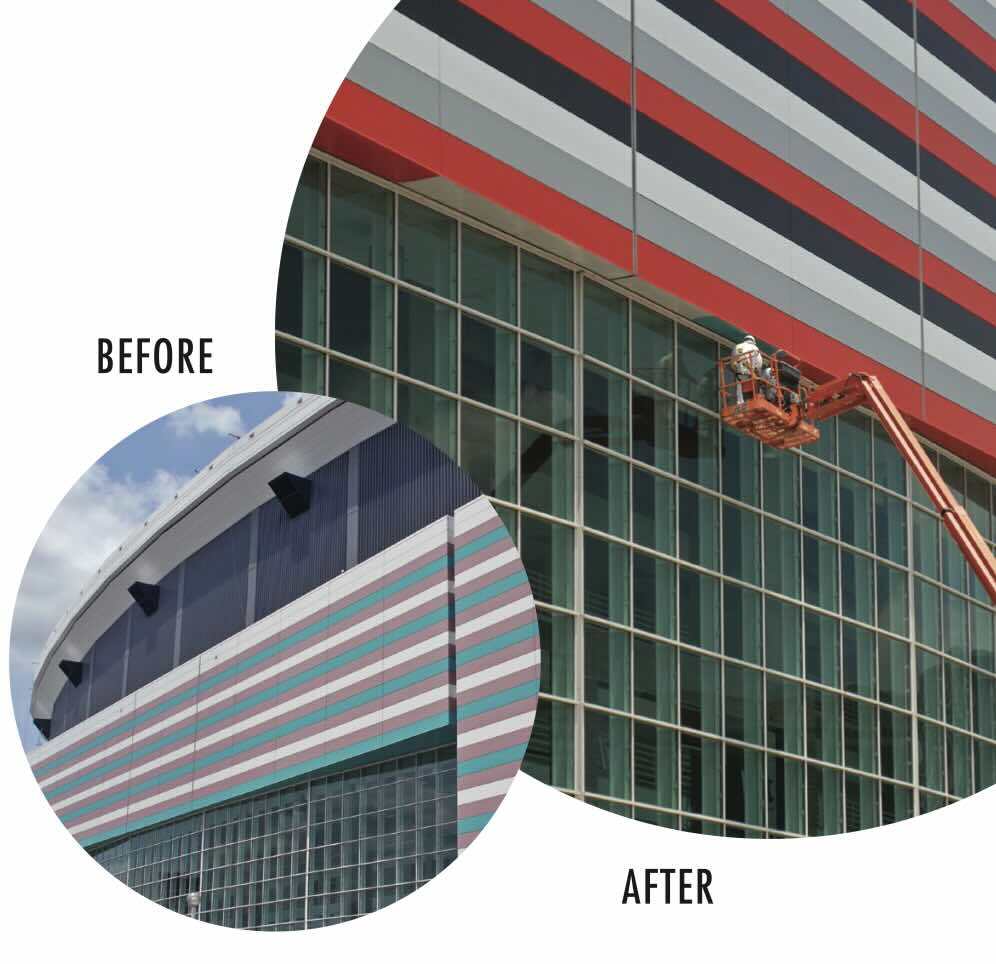
High Performance Coatings vs. Standard Interior...
Explore the dynamic world of high performance...
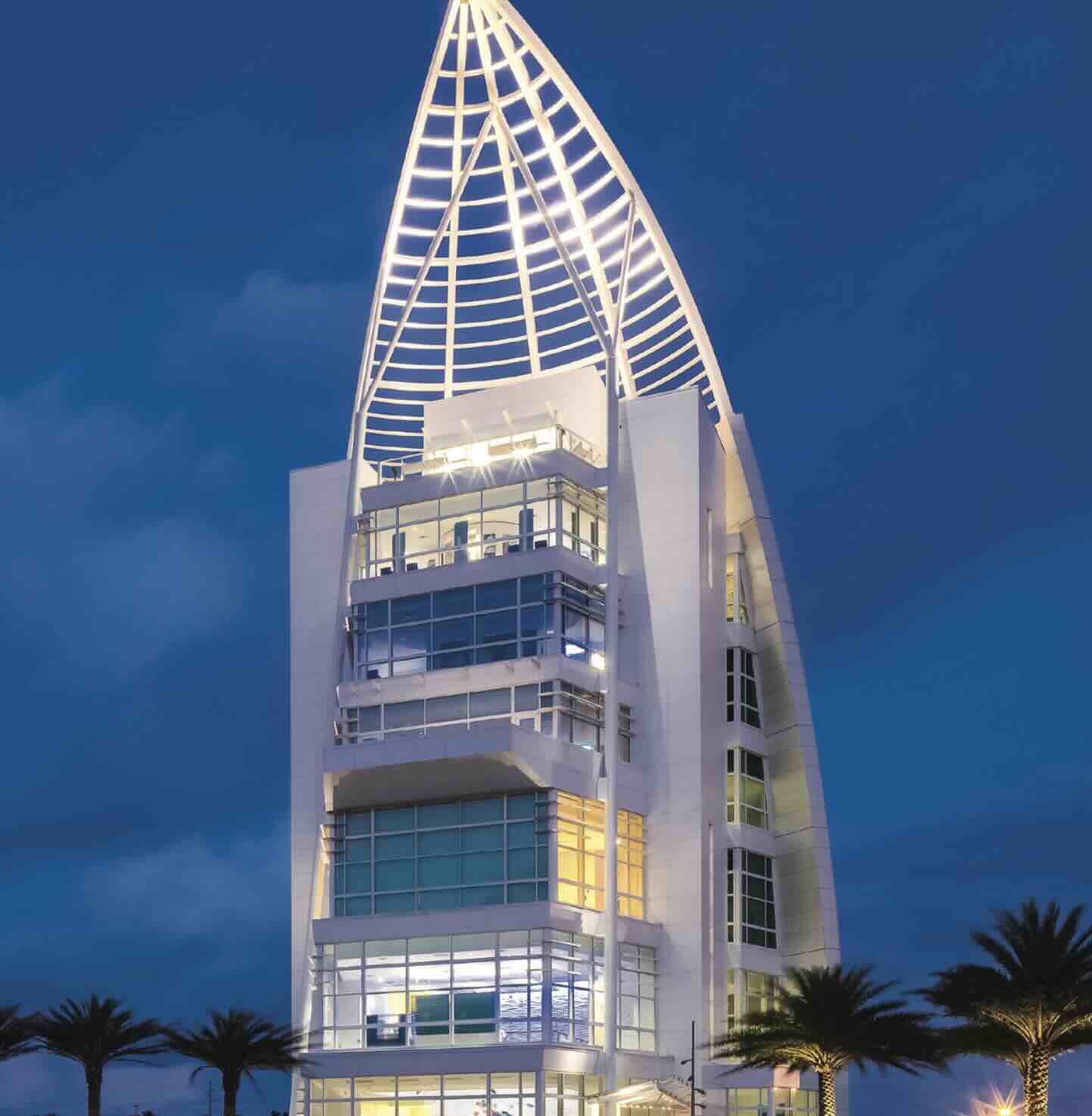
Decoding High Performance Coatings: A Comparative...
Explore the cutting-edge world of high...
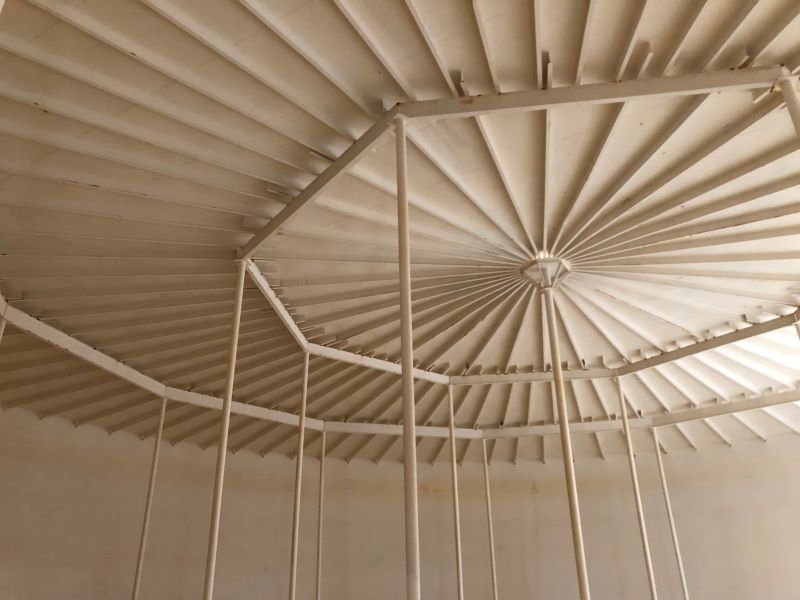
Why Interior Dry Space Coatings Are Essential for...
Ensuring the longevity and safety of potable...