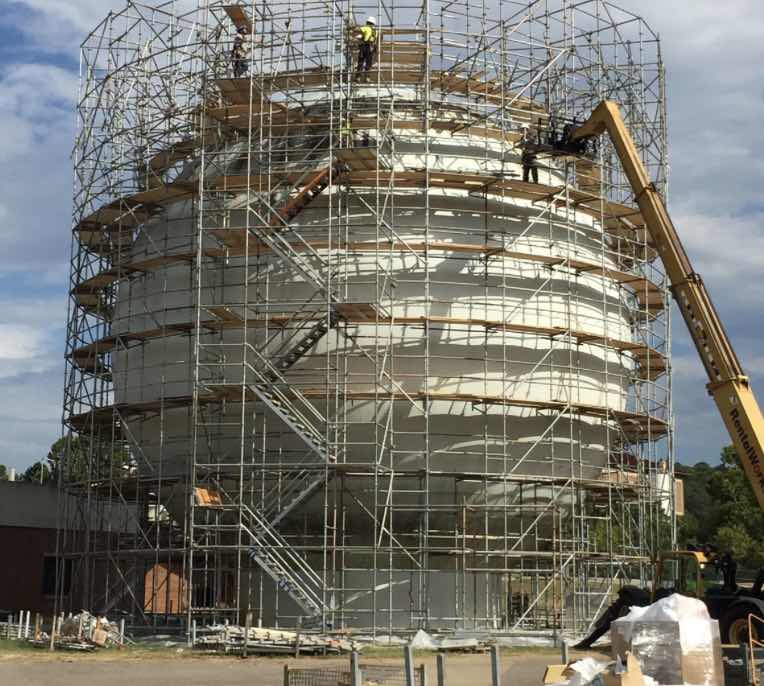
Tackling Common Challenges of Applying High Performance Coatings
The application of High Performance Coatings can present unique challenges that require careful consideration and expertise.
- High Performance Coatings
High performance coatings offer a multitude of benefits, including enhanced durability, corrosion resistance, and improved aesthetics. However, applying these coatings can present unique challenges that require careful consideration and expertise. In this blog post, we will explore some common challenges encountered when applying high performance coatings and discuss effective strategies to address them.
1. Surface Preparation:
Proper surface preparation is crucial for the successful application of high performance coatings. Challenges may arise when dealing with surfaces contaminated with oil, grease, rust, or other contaminants. Thorough cleaning, degreasing, and removing loose or deteriorated coatings are essential steps. It is important to follow recommended surface preparation guidelines and use suitable techniques such as abrasive blasting, chemical cleaning, or mechanical surface profiling to ensure a clean and properly prepared substrate.
2. Adhesion Issues:
Achieving strong adhesion between the coating and the substrate is vital for long-term performance. Incompatibility between the coating and the substrate, inadequate surface preparation, or insufficient priming can lead to poor adhesion. To address this challenge, it is crucial to select coatings specifically formulated for the substrate material and to follow the manufacturer's instructions regarding priming, curing times, and application conditions. Proper surface preparation, including profiling the substrate if necessary, helps promote adhesion.
3. Thickness Control:
Controlling the thickness of high performance coatings is essential to ensure their performance and longevity. Applying coatings too thin may compromise their protective properties, while excessive thickness can result in uneven curing, cracking, or poor adhesion. Utilizing proper equipment, such as calibrated spray guns or application tools, and following manufacturer guidelines regarding wet film thickness and dry film thickness measurements can help achieve the desired coating thickness.
4. Drying and Curing Time:
High performance coatings often require specific drying and curing times to achieve optimal properties. Insufficient drying or premature exposure to adverse conditions can lead to inadequate film formation or compromised performance. It is essential to follow the manufacturer's instructions regarding temperature, humidity, and curing time to allow the coating to fully cure and develop its desired properties.
5. Environmental Factors:
Environmental conditions, such as temperature, humidity, and air quality, can significantly impact the application and performance of high performance coatings. Extreme temperatures or high humidity can affect coating viscosity, drying time, and film formation. Inadequate ventilation may lead to trapped solvents or air bubbles in the coating. It is important to work within the recommended environmental conditions specified by the coating manufacturer and to adjust application techniques accordingly.
6. Safety and Health Considerations:
High performance coatings often contain chemicals that require careful handling and adherence to safety guidelines. Proper personal protective equipment (PPE), such as gloves, goggles, and respirators, should be used to protect applicators from potentially harmful substances. Adequate ventilation in the application area is essential to maintain air quality and prevent the accumulation of hazardous fumes. Compliance with safety regulations and proper training on handling and disposal of coating materials are vital to mitigate safety and health risks.
Applying high performance coatings comes with its fair share of challenges. By addressing these challenges proactively and following best practices, such as thorough surface preparation, ensuring proper adhesion, controlling coating thickness, adhering to drying and curing times, considering environmental factors, and prioritizing safety and health, these challenges can be effectively overcome. Collaborating with experienced coating professionals, following manufacturer guidelines, and staying updated with industry advancements will help ensure successful and long-lasting applications of high performance coatings, maximizing their benefits in terms of protection, durability, and aesthetics.
If you need advice from a team with over 200 years of combined experience, reach out to us here at High Performance Coatings.
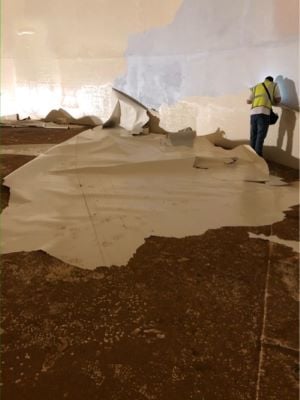
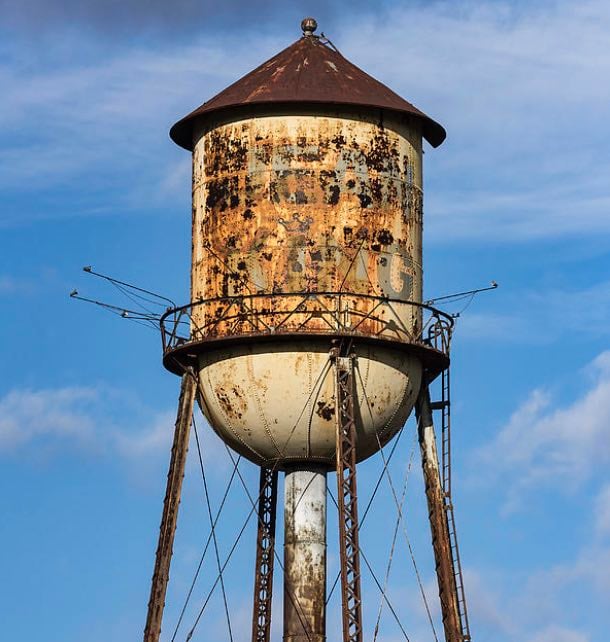
What Maintenance is Required with High...
Maintenance requirements for high-performance...
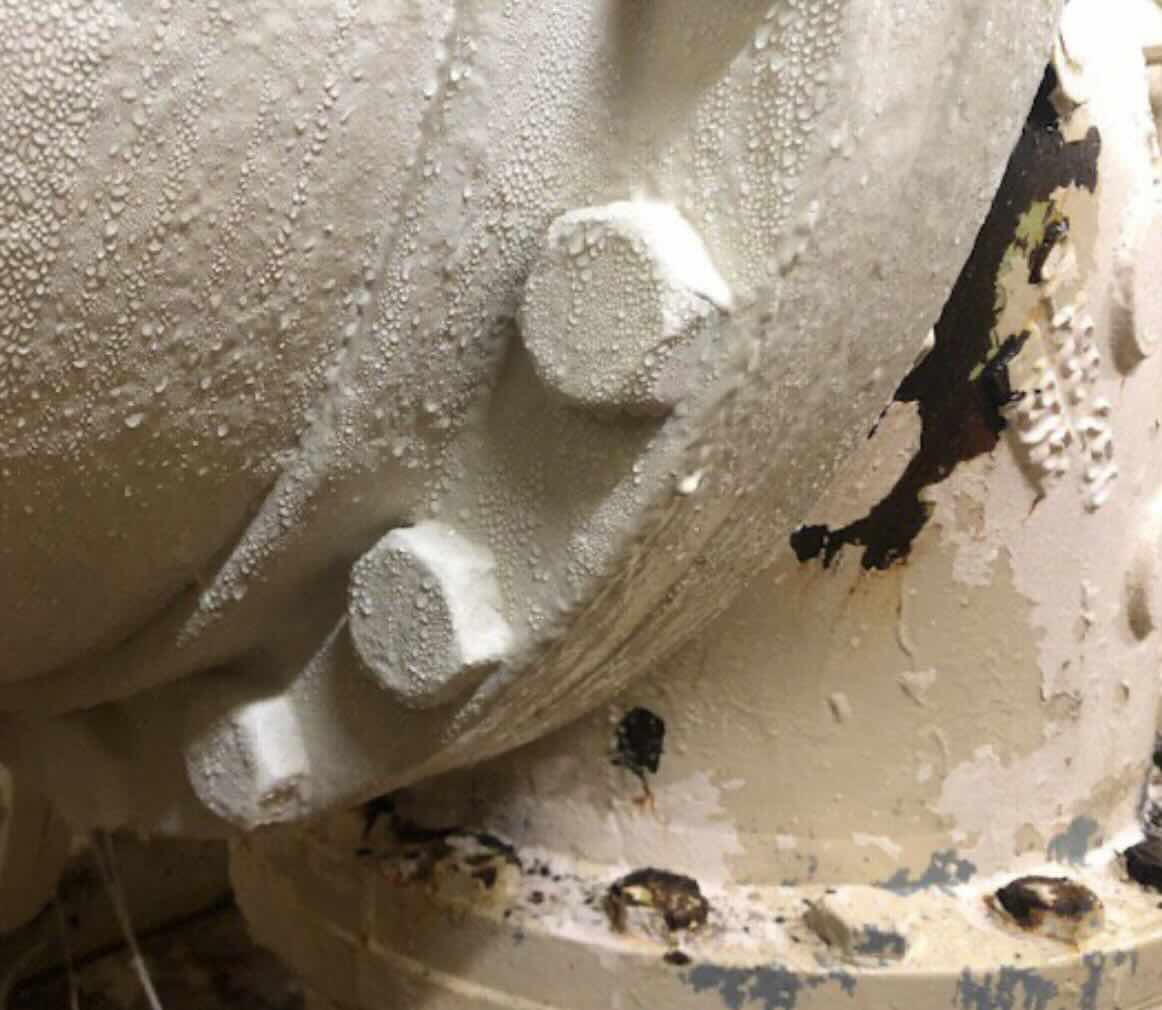
Ultimate Guide to Surface-Tolerant Epoxy Coatings
Discover the resilient world of surface-tolerant...