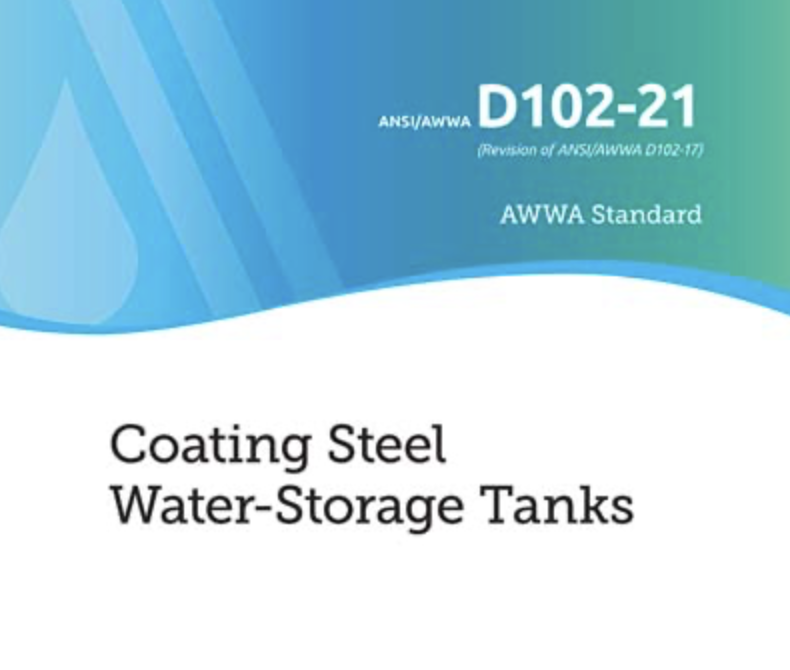
How to Meet AWWA D102 Water Tank Coating Standards
Ensuring the longevity and safety of water tanks is crucial, and meeting AWWA D102 coating standards is an essential part of this process. This blog provides a comprehensive guide on how to achieve these standards, including a detailed discussion on OCS and ICS systems.
- Rick Gilbreath
HOW TO MEET AWWA D102 WATER TANK COATING STANDARDS
Ensuring the longevity and safety of water tanks is crucial, and meeting AWWA D102 coating standards is an essential part of this process. This blog provides a comprehensive guide on how to achieve these standards, including a detailed discussion on OCS and ICS systems.
Understanding AWWA D102 Coating Standards
The AWWA D102 coating standards are established to ensure the comprehensive protection and extended longevity of water storage tanks, which are critical components in water supply systems. These standards provide detailed specifications regarding the types of coatings that should be utilized, the precise methods of application that must be employed, and the rigorous quality control measures that need to be adhered to throughout the process. By following these standards, the risk of corrosion is significantly minimized, which in turn reduces the frequency and cost of maintenance activities. Moreover, adherence to these standards plays a vital role in ensuring the safety and purity of the water stored within the tanks, safeguarding public health and maintaining the integrity of the water supply.
Meeting AWWA D102 standards is not a straightforward task; it requires a comprehensive and in-depth understanding of various coating systems, surface preparation requirements, and the environmental considerations that may impact the coating process. Construction companies and professionals involved in the maintenance and installation of water tanks must stay informed and updated with the latest revisions and amendments to these standards. This is crucial to ensure not only compliance but also the optimal performance and durability of the water tanks over time. By keeping abreast of these updates, companies can implement the most effective strategies and technologies to enhance the resilience and functionality of water storage systems, ultimately contributing to the reliability and efficiency of water distribution networks.
Overview of OCS (Outside Coating System) and ICS (Inside Coating System)
The AWWA D102 standard categorizes coating systems into two primary groups: Outside Coating System (OCS) and Inside Coating System (ICS). The Outside Coating System (OCS) is meticulously designed to protect the exterior surfaces of water tanks from a variety of environmental factors that can cause deterioration over time. These factors include harmful UV radiation from the sun, which can degrade materials, moisture from rain or humidity that can lead to rust and corrosion, and temperature fluctuations that can cause expansion and contraction, potentially leading to cracks or other structural issues. By providing a robust barrier against these elements, OCS plays a critical role in preserving the structural integrity and longevity of the water tanks.
On the other hand, the Inside Coating System (ICS) is specifically focused on safeguarding the interior surfaces of the tanks. This system is essential for protecting against water-borne contaminants that can compromise water quality, as well as preventing corrosion and other internal conditions that could damage the tank from the inside out. The ICS ensures that the water stored within the tank remains safe and pure, free from any harmful substances that could leach into the water supply.
Both the OCS and ICS are crucial for the overall integrity and functionality of the water tank. While the OCS ensures the structural durability by preventing external damage and degradation, the ICS is responsible for maintaining the quality and safety of the water stored within the tank. Proper selection and application of these systems are vital for meeting AWWA D102 standards, as they ensure that the tanks can withstand both external and internal challenges, thereby extending their service life and maintaining the reliability of the water supply system.
Key Differences Between OCS Systems
Recognizing these differences is crucial for choosing the right coating system based on environmental exposure and performance needs, as each type of Outside Coating System (OCS) is specifically engineered to address distinct challenges posed by various environmental conditions. For instance, some OCS types are designed to withstand extreme UV exposure, while others are optimized for high humidity or salt-laden environments. Each OCS type has unique application methods that require specific techniques and equipment to ensure proper adhesion and effectiveness. Additionally, the curing durations can vary significantly, with some coatings requiring extended periods to achieve full hardness and durability, which is essential for long-term protection.
Maintenance requirements also differ, with some systems necessitating more frequent inspections and touch-ups to maintain their protective qualities. Adhering to these specific application methods, curing durations, and maintenance requirements is essential to meet AWWA D102 standards, ensuring that the water tanks remain protected and functional over their intended lifespan.
Key Differences Between ICS Systems
The selection of an Inside Coating System (ICS) is a critical decision that hinges on several important factors, each of which can significantly impact the performance and effectiveness of the coating. One of the primary considerations is the type of water that will be stored within the tank. This includes evaluating whether the water is potable, non-potable, or contains specific minerals or impurities that could interact with the coating material. Additionally, the presence of any chemical additives, such as chlorine or other disinfectants used in water treatment processes, must be taken into account, as these chemicals can affect the integrity and longevity of the coating. Furthermore, the operational conditions of the tank, such as temperature fluctuations, pressure variations, and the frequency of water turnover, play a crucial role in determining the most suitable ICS. A thorough understanding of these factors is essential to ensure that the selected coating system can withstand the specific challenges posed by the tank's environment.
Proper application of the ICS is equally important, as it ensures that the internal surfaces of the tanks are adequately protected against corrosion, microbial growth, and other potential contaminants. This protection is vital for maintaining the quality and safety of the water stored within the tank, preventing any harmful substances from leaching into the water supply. Moreover, by safeguarding the internal surfaces, the ICS contributes to extending the lifespan of the tank, reducing the need for frequent repairs or replacements, and ultimately ensuring the reliability and efficiency of the water storage system over time.
Steps to Ensure Compliance with AWWA D102 Standards
Ensuring compliance with AWWA D102 standards involves several critical steps that are essential for the successful protection and longevity of water storage tanks. Firstly, it is imperative to conduct a thorough assessment of the tank's environment and operational conditions. This involves evaluating factors such as the local climate, potential exposure to corrosive elements, and the specific operational demands of the tank, such as pressure and temperature variations. This comprehensive evaluation is crucial for selecting the most suitable Outside Coating System (OCS) and Inside Coating System (ICS) that can effectively withstand the unique challenges posed by the tank's environment.
Once the appropriate coating systems have been selected, the next step is to prepare the surfaces meticulously according to the standard's guidelines. This preparation process is vital to ensure optimal adhesion and performance of the coatings. It involves cleaning the surfaces to remove any contaminants, rust, or old coatings, and may include abrasive blasting or other surface preparation techniques to achieve the desired surface profile. Proper surface preparation is a foundational step that directly impacts the effectiveness and durability of the coating systems.
The application of the coatings should be carried out by trained professionals who are well-versed in the specified methods and equipment required for the task. These professionals must follow precise application techniques to ensure uniform coverage and thickness, which are critical for the coatings to perform as intended. The use of specialized equipment, such as spray guns or rollers, may be necessary to achieve the desired results, and adherence to the manufacturer's instructions and AWWA guidelines is essential.
Regular inspections and quality control measures must be implemented throughout the coating process and beyond to detect any deviations from the standards. These inspections should include visual assessments, thickness measurements, and adhesion tests to verify that the coatings meet the required specifications. Any identified issues should be addressed promptly to prevent potential failures and ensure the long-term integrity of the tank.
Finally, maintaining detailed documentation of all procedures and inspections is crucial. This documentation serves as evidence of compliance with AWWA D102 standards and facilitates future maintenance activities. It should include records of the environmental assessment, surface preparation methods, coating application details, inspection results, and any corrective actions taken. By keeping comprehensive records, companies can ensure accountability, streamline maintenance efforts, and provide valuable information for future reference, ultimately contributing to the sustained performance and reliability of the water storage system.
Common Challenges and Solutions in Meeting Coating Standards
Meeting AWWA D102 coating standards can present several challenges, each of which requires careful consideration and strategic planning to overcome. One of the primary challenges is the environmental conditions that can significantly affect the application process. Factors such as temperature, humidity, and wind can influence the drying and curing times of coatings, potentially leading to uneven application or compromised adhesion if not properly managed. Additionally, the availability of suitable materials that meet the stringent AWWA specifications can be a hurdle, as not all products on the market are designed to withstand the specific demands of water tank environments. This necessitates a thorough evaluation of available materials to ensure they possess the necessary properties for durability and effectiveness. Furthermore, ensuring skilled labor for proper application is crucial, as the complexity of the coating process requires applicators who are not only trained but also experienced in handling the specific techniques and equipment involved. This expertise is vital to achieving the precise application required to meet the standards.
Moreover, maintaining compliance over the tank's lifespan is an ongoing challenge that demands regular inspections and maintenance. This involves not only routine checks to assess the condition of the coatings but also proactive measures to address any signs of wear or damage before they escalate into more significant issues. The dynamic nature of environmental exposure and operational conditions means that even the most robust coatings can degrade over time, necessitating a vigilant approach to maintenance.
To address these challenges effectively, several solutions can be implemented. Thorough planning and assessment before starting the project are essential to identify potential obstacles and develop strategies to mitigate them. This includes conducting a detailed analysis of the environmental conditions and selecting the most appropriate coating systems that can withstand these challenges. Selecting high-quality materials that meet AWWA specifications is also critical, as these materials are specifically engineered to provide the necessary protection and longevity. Investing in training for applicators is another key solution, as it ensures that the workforce is equipped with the knowledge and skills required to execute the coating process with precision and consistency.
Implementing a robust inspection and maintenance program is vital for the long-term success of the coating systems. This program should include regular inspections to monitor the condition of the coatings, as well as a schedule for maintenance activities to address any issues promptly. By identifying and addressing potential problems early, companies can prevent more significant failures and ensure the coatings continue to perform effectively throughout the tank's lifespan. This proactive approach not only helps maintain compliance with AWWA D102 standards but also contributes to the overall reliability and efficiency of the water storage system, safeguarding public health and ensuring a consistent water supply.
For a free inspection or specification assistance, we can help design the right system for any water tank, both concrete or steel. Reach out to us here, and we'll get back to you within 24 hours.
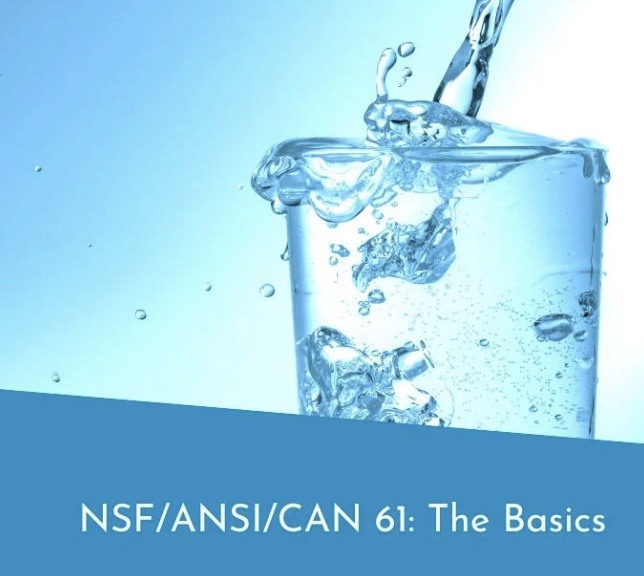
NSF-Approved Coatings for Potable Water Tanks
NSF-APPROVED COATINGS FOR POTABLE WATER TANKS
...
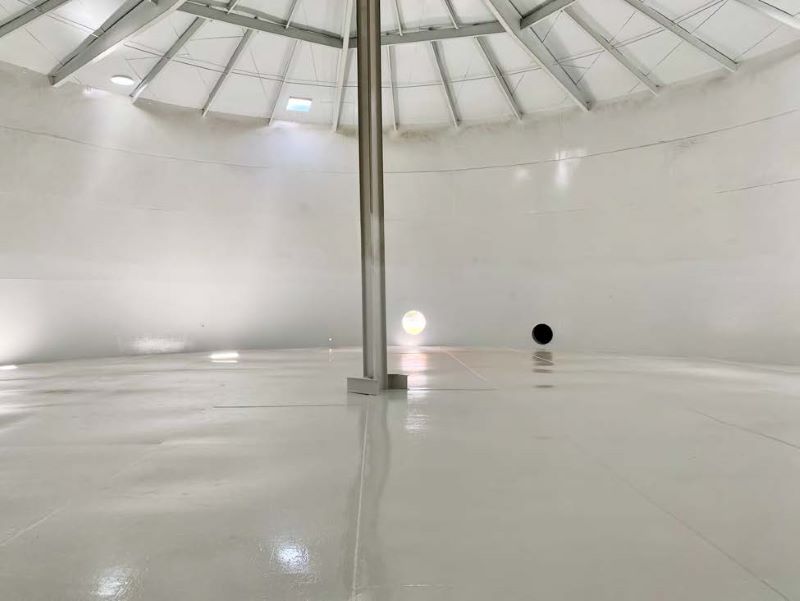
Interior Immersion Grade Coatings: Protecting...
Ensuring the longevity and safety of potable...
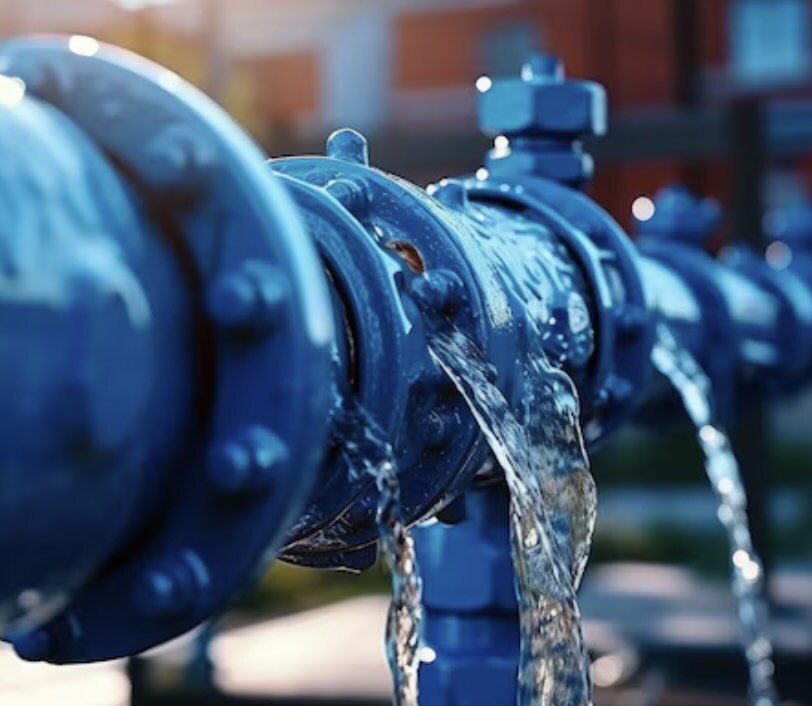
Exploring Coatings in AWWA C210 Standard
Unlock the secrets of enhanced pipeline longevity...